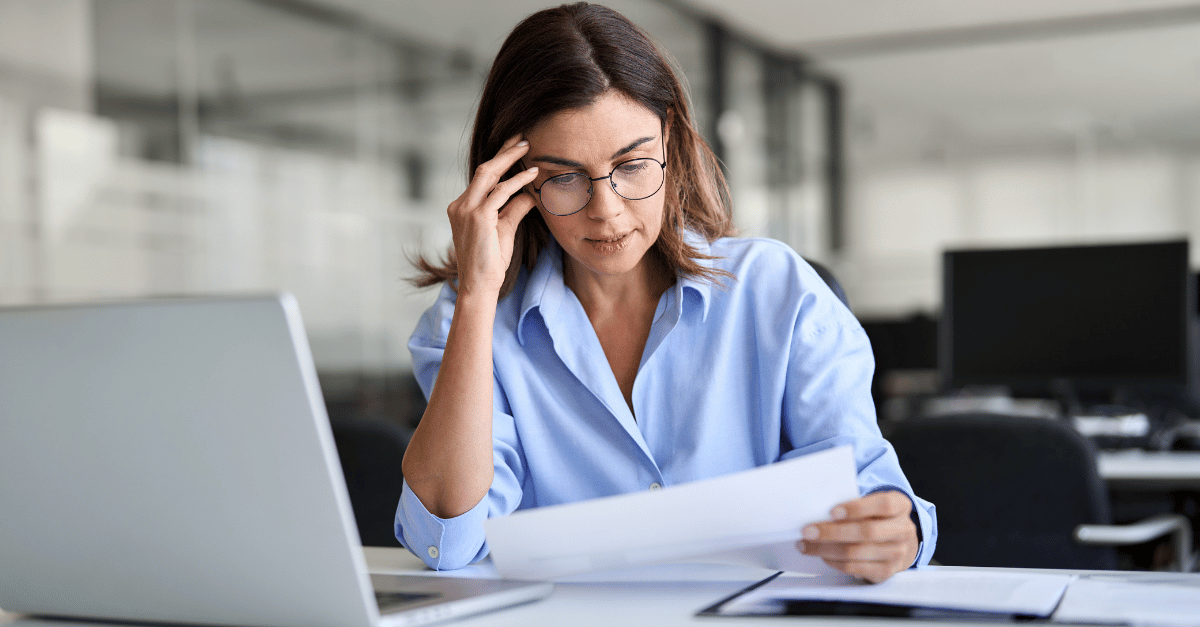
If you search the internet, you’ll find the following four types of Warehouse Management Systems: standalone WMS, cloud-based WMS, integrated Enterprise Resource Planning (ERP) modules, and Supply Chain Execution (SCE) modules. However, that really paints a short-sighted picture regarding your options for a WMS, as when you’re searching for one, the type of system is less important than thoroughly understanding your specific warehouse management needs.
Rather than starting with whether you need a cloud-based (also known as SaaS WMS), standalone, or a module in your ERP, it’s important to focus on the unique requirements of your business, such as the complexity of your warehouse processes, the demands of your industry, and technical structure or tech stack integration needs. By honing in on these factors, you can more easily identify the best WMS for your specific needs.
In this article, we’ll cover:
- The types of WMS systems based on complexity
- The types of WMS systems based on industry category requirements
- The types of WMS systems, according to Gartner
- How to find the right WMS for your business
Types of Warehouse Management Systems Based on Complexity: Tier System
Warehouse complexity and business requirements will determine what WMS tier is best for your operation. While highly complex warehouse environments will require robust functional breadth, simpler operations usually need less. Determining the complexity of your operations is an excellent place to start your search.
There are three tiers of warehouse management systems:
Tier 1: Advanced systems designed for large, complex organizations with multi-location operations and automation needs. This tier offers multiple functionalities, like task management, task interleaving, voice activation, RFID, wireless communication, and automation support that serve complex fulfillment networks. Large-scale operations will benefit from robust functionality, steady support, flexibility, and scalability.
While a Tier 1 WMS has high-volume capabilities and automation interfaces, it also comes at a significantly higher upfront cost, takes longer to implement, and usually boasts higher support and maintenance costs.
Tier 2: Mid-range systems for growing businesses that need more than basic functionality but do not require the complexity of Tier 1. Along with all the functionality included in Tier 3 capabilities, a Tier 2 WMS offers advanced business rules for more complex distribution environments, and can support multiple warehouses, multiple clients (3PL), and can include automation integration. These solutions may support complex internal processes, including kitting, replenishment, and different methods of counting, depending on the vendor.
A Tier 2 system can be scalable and adaptable to evolve as distribution needs change or grow, but that scalability will vary by vendor. Its integration abilities may note be as strong as a Tier 1 in highly automated facilities with high volumes.
Tier 3: Entry-level systems for small businesses with relatively simple operations. These systems provide basic receiving, picking, packing, and shipping. They are the perfect fit for operations with limited budgets and no plans for expansion. Tier 3 solutions are the easiest and least expensive to install, but usually cannot support multi-warehouse networks. With limited flexibility, warehouses with Tier 3 WMSs must match their processes to what the WMS can provide.
Types of Warehouse Management Systems Based on Industry Category Requirements
Each industry has a unique set of WMS requirements because operational needs, product characteristics, and regulatory demands vary significantly. For example, pharmaceutical companies require robust lot tracking and regulatory compliance features, while e-commerce retailers need rapid order processing and real-time inventory visibility. A WMS must be flexible enough to handle industry-specific challenges, whether it’s managing temperature-sensitive goods in cold storage or optimizing space for high-volume SKU environments in retail.
Warehouse management system requirement by industry:
Consumer goods companies need a WMS that provides real-time inventory visibility to track stock levels and help reduce shortages. It must also support high-volume processing with the functionality to handle seasonal peaks and demand surges efficiently. These companies also need the WMS to integrate with automated picking and packing systems while providing advanced reporting. Consumer goods distributors need a WMS that fosters scalability to accommodate business growth and changing product lines.
Ecommerce businesses need a WMS that can handle the complexities of modern online retail. Effective order management is crucial, allowing companies to intelligently aggregate and organize shipments based on a variety of characteristics, streamlining fulfillment. Value-added services (VAS) are also essential, enabling brands to enhance the consumer experience with options like custom packaging, inserts, etc. Additionally, a WMS must simplify returns processing, allowing brands to efficiently manage replacements, refunds, or restocking.
Food and beverage companies require a WMS with smart record-keeping, robust lot and expiration date tracking, and advanced sensors to ensure product freshness and compliance. The system must support real-time inventory visibility and temperature-controlled storage and handling to manage perishable goods effectively, especially for short-shelf-life products to prevent spoilage. Importantly, food and beverage distributors need traceability for recalls and regulatory audits and the ability to integrate with automated systems to optimize workflows for high-speed order processing and delivery.
Manufacturers need a WMS that offers real-time inventory visibility to manage raw materials, work-in-progress, and finished goods efficiently. It should support advanced features like lot and batch tracking, ensuring traceability and compliance with industry regulations. Seamless integration with ERP systems and production schedules is essential to synchronize supply and demand. Labor management tools that optimize workforce productivity and task interleaving are also critical for reducing downtime. Lastly, scalability and adaptability are key to handling fluctuations in production volume and evolving business needs.
Retail businesses need real-time inventory tracking across multiple locations to prevent stockouts and overstocks. The WMS must offer seamless integration with point-of-sale (POS) systems to ensure accurate order processing and fulfillment. Other features include support for omnichannel operations, such as in-store pickups and online orders. Finally, retailers benefit from advanced reporting and analytics for understanding demand patterns and optimizing stock levels, along with scalability and flexibility to handle seasonal peaks and changing product assortments.
A 3PL will benefit from a 3PL WMS that supports multi-client management to handle inventory for multiple customers in one system. The system must provide real-time visibility into inventory and order status and must be highly customizable to meet the diverse requirements of various industries and clients. The ability to integrate with transportation management systems (TMS) and robust billing and reporting features is needed to manage complex billing structures for every client.
Wholesale distributors need inventory management to handle large volumes and diverse SKUs. Real-time stock tracking and order processing ensure fast and accurate fulfillment. To manage inbound and outbound logistics, the system must seamlessly integrate with supply chain partners. Robust reporting and analytics are necessary for monitoring performance, optimizing stock levels, and improving order accuracy. Lastly, scalability is key to supporting fluctuating demand and business growth across multiple locations.
Types of Warehouse Management Systems, According to Gartner
Every year, Gartner evaluates different WMS providers to create a detailed report on WMS strengths and weaknesses. The report, Gartner’s Magic Quadrant for Warehouse Management Systems, categorizes the systems into four categories, niche players, challengers, visionaries, and leaders. It also distinguishes between standard WMS capabilities and optional/advanced capabilities:
Standard | Optional/Advanced |
|
|
Gartner also breaks WMS vendors into five types of vendors, four of which are covered in the report.
- Application mega vendors
- SCM suite vendors
- Specialist WMS suite vendors
- Material handling equipment/automation vendors
- Independent WMS component vendors that specialize in ISVs (mot covered by Gartner reporting)
If selecting a new WMS is on your to-do list, we believe the Gartner® Magic Quadrant™ for Warehouse Management Systems is a must-have!
Finding the Right WMS for Your Business
When searching for a Warehouse Management System (WMS), it’s easy to get caught up in the four common types of Warehouse Management Systems: standalone WMS, cloud-based WMS, integrated ERP modules, and Supply Chain Execution (SCE) modules. However, focusing solely on these categories can limit your decision-making. The true key to selecting the right WMS lies in understanding your specific operational needs—whether that involves complex warehouse processes, industry demands, or your technical infrastructure. By prioritizing these business requirements over system types, you’ll be better equipped to find the WMS that best fits your organization’s unique needs. To help you gain a better understanding of your unique business requirements, we’ve created The Ultimate WMS RFP Template for you to use. With over 250 functional and 100 technical requirements listed, the template gives you an excellent starting point to evaluate your business to determine your needs accurately.