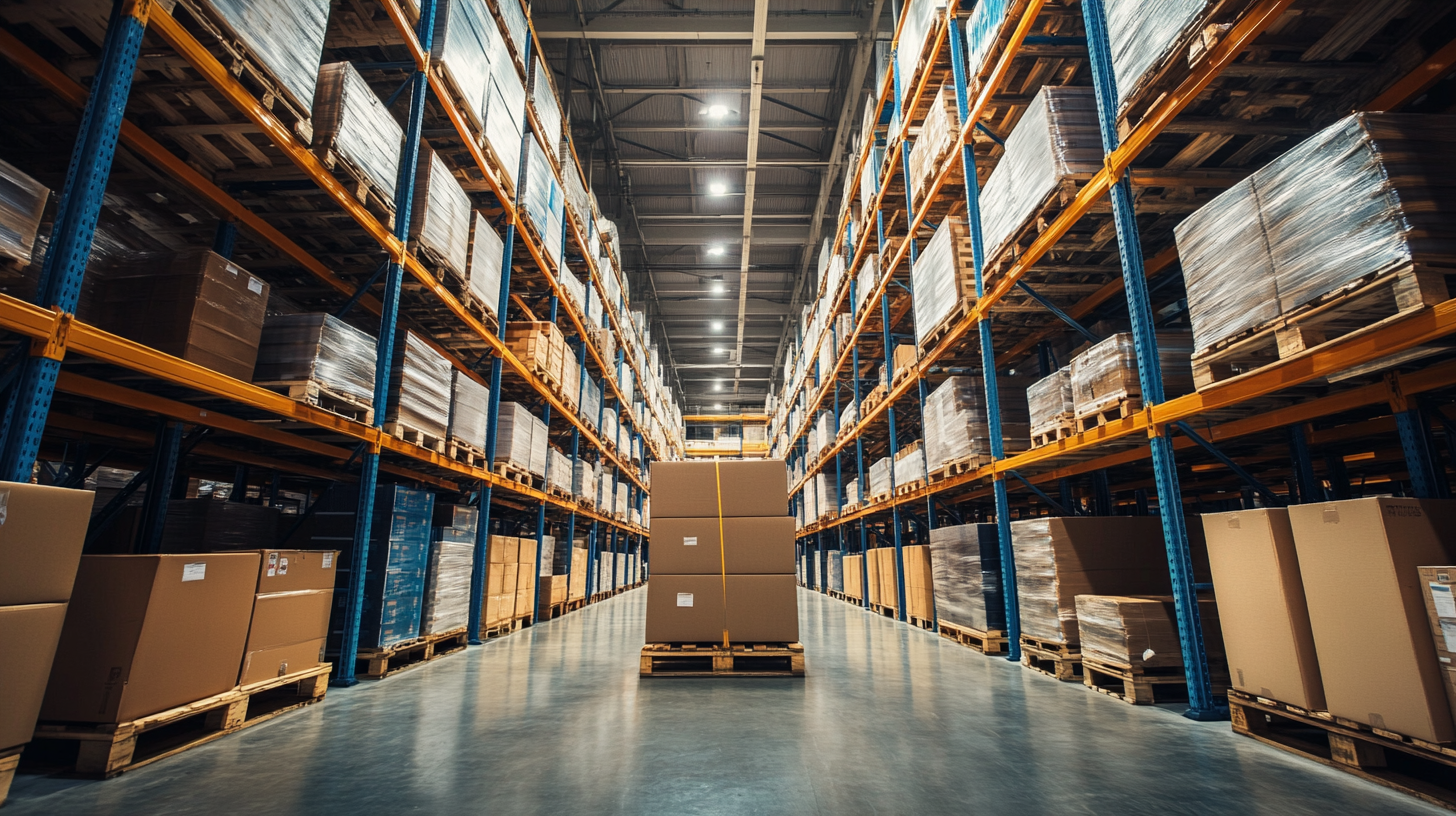
Warehouse management is a critical component of how warehouses are set up to succeed. It refers to the processes, strategies, and technologies, like a warehouse management system, that are used to control and optimize operations within a warehouse or distribution center. Warehouse management involves the coordination of storage and the movement and handling of goods and materials, to ensure they are properly received, and efficiently stored and shipped to meet customer demand and business objectives. It’s a complicated process, but with the right tools in place, it can be how businesses stand apart from their competition.
In this article, we’ll cover:
- What is warehouse management?
- Challenges with warehouse management
- The benefits of warehouse management
- 7 important warehouse management processes
- Important technology and systems for effective warehouse management
- Popular industries that require warehouse management
- Important stakeholders in warehouse management
- Warehouse management trends to watch
What is Warehouse Management?
While warehouse management may vary by industry, certain core functions are essential across the board. To meet the demands of today’s complex supply chains, businesses should ensure their warehouse management processes address these key components:
- Inventory Control: Tracking and managing stock levels to ensure the right products are available in the right quantities.
- Receiving and Putaway: Coordinating the efficient receipt of goods and placing them in designated storage locations.
- Order Picking and Packing: Managing the process of retrieving items for orders and preparing them for shipment.
- Shipping and Distribution: Ensuring goods are shipped to the correct destinations promptly and cost-effectively.
- Space Utilization and Layout Optimization: Designing warehouse layouts and storage strategies to maximize warehouse space utilization and streamline operations.
- Labor Management: Scheduling and supervising warehouse staff to ensure productivity and safety.
- Technology Integration: Using Warehouse Management Systems (WMS) and other software tools to automate and improve processes, including barcode scanning, RFID, and real-time data tracking.
- Safety and Compliance: Implementing measures to ensure worker safety and compliance with industry regulations.
The goal of effective warehouse management is simple, it’s a way for businesses to reduce operational costs, improve accuracy, and enhance order fulfillment. Businesses with effective warehouse management only stand to benefit, as without it, the challenges can have a severe impact on the bottom line.
Challenges With Warehouse Management
There are a variety of warehouse management challenges that can affect an operation’s overall business performance. The most common ones are inaccurate inventory, poor space utilization, inefficient order fulfillment, and problematic labor management, but there are many others with just as severe an impact.
-
- Inadequate Technology Integration: Operations that rely on manual or paper-based processes instead of a Warehouse Management System (WMS) are far more prone to errors. Additionally, the inability to integrate warehouse operations with other supply chain systems creates inefficiencies and bottlenecks.
- Seasonal Fluctuations: Managing seasonal peaks and valleys is a significant challenge, often resulting in either overstocking or stockouts. These missteps can directly increase operational costs and strain resources.
- High Operational Costs: Inefficient warehouse management can lead to soaring labor, energy, and transportation costs. Outdated equipment and processes only exacerbate the issue, quickly driving expenses out of control.
- Reverse Logistics Challenges: Handling returns and exchanges is inherently complex and resource-intensive. Without a streamlined reverse logistics process, operations can face disruptions that damage customer trust and the company’s reputation.
- Safety: Maintaining a safe working environment while adhering to regulatory requirements is a persistent challenge. Failing to comply can lead to fines, legal complications, and operational downtime, impacting both efficiency and worker well-being.
A combination of technology, skilled personnel, strategic planning, and implementation of continuous improvement strategies to optimize warehouse operations will enhance supply chain performance. And it all begins with the right warehouse management system.
The Benefits of Warehouse Management
Implementing a WMS has a direct, positive impact on a business’s operations, profitability, and reputation. After all, no one has ever complained about a business being “too organized” and that is exactly what warehouse management offers, a roadmap to organization, allowing businesses to plan for all potential contingencies to safeguard their operational efficiency and strengthen their supply chain. So, what benefits can one expect after investing in a WMS?
Improved Inventory Accuracy
- Precise tracking reduces errors in stock levels
- Real-time inventory visibility helps to minimize overstocking or stockouts and ensures inventory is available to fulfill orders.
Enhanced Order Fulfillment
- Faster order turnaround due to accelerated picking, packing, and shipping processes.
- Reduces errors in order fulfillment, leading to higher customer satisfaction.
Better Space Utilization
- Smart layouts and improved slotting strategies help operations maximize storage capacity.
- Reducing unnecessary movement within the warehouse allows for improved workflows.
Cost Savings
- Optimized labor and resource use leads to lower operational costs.
- Reduces losses from damaged or misplaced goods.
- Improves space utilization, delaying or avoiding the need for warehouse expansion.
Increased Operational Efficiency
- Enterprise technology, like a WMS, streamlines operations.
- Automation helps to reduce manual work and human error.
Stronger Supplier and Partner Relationships
- Accurate and timely data exchange helps to facilitate smoother communication and transactions with vendors and partners.
- Ensures on-time order processing, strengthening trust and reliability.
Improved Decision-Making
- Detailed reporting and analytics provide better insights into performance metrics.
- Enables proactive adjustments to demand fluctuations and supply chain disruptions.
Higher Customer Satisfaction
- Elevates brand reputation with accurate and on-time deliveries.
- Offers better tracking and transparency, enhancing the customer experience.
Scalability and Adaptability
- Supports business growth with flexible systems and processes that can scale with demand.
- Adapts quickly to market changes or supply chain challenges.
Compliance and Safety
- Different technologies, like a WMS, help ensure businesses adhere to industry regulations and standards, reducing legal risks.
- Promotes a safe working environment, decreasing the likelihood of workplace accidents.
With the right plan, technology, and tools in place, businesses can foster smoother daily operations while having a strategic advantage in a competitive marketplace. The best way to address warehouse management is to invest in a WMS that can address your current business requirements and growth goals, like Made4net’s configurable cloud-based WMS.
7 Important Warehouse Management Processes
Core WMS functionality includes inventory management, order management, receiving and putaway, picking and packing, shipping and transportation management, and barcoding and scanning integration. Beyond these core functionalities, a WMS can deliver added capabilities that elevate operations to the next level, offering solutions tailored to modern challenges and opportunities.
- Task Interleaving, which allows operations to adjust tasks in real-time, enabling them to stay responsive to changing priorities throughout the day.
- Labor management, which not only tracks task assignments and monitors productivity but also recommends and manages incentive programs, delivers accurate labor forecasting and planning, supports employee training and skill development, and enhances workplace safety
- Cycle counting, which classifies items and performs inventory counts without shutting down the entire operation.
- Cartonization involves analyzing all items to be packed and optimizing packaging to reduce waste and shipping costs while ensuring the protection of items during transit.
- Omnichannel functionality, enabling businesses to manage a variety of order types all from within the same facility.
- Adaptability, allowing businesses to customize the WMS to fit their needs as they grow throughout the years.
- Cloud-based functionality, which offers access from anywhere with an internet connection, and doesn’t require a significant upfront cost like an on-premise solution.
Important Technology and Systems for Effective Warehouse Management
When selecting a SaaS WMS solution for your operation, one of the biggest decisions made is whether to deploy a cloud-based WMS or an on-premise solution. Both systems have their pros and cons, and how well they work will depend on your specific needs. For example, businesses in remote locations without reliable access to the internet will most likely choose an on-premise solution, as the risk of losing connectivity during operations is not worth taking. On the other hand, companies facing sudden, exponential growth may not have the capital or IT infrastructure needed to invest in an on-premise solution, making the cloud-based offering more feasible as it doesn’t require costly hardware and can be deployed remotely.
Advantages of cloud-based WMS | Concerns with cloud-based WMS |
|
|
Cloud-based solutions have come a long way in addressing these challenges, particularly around data security. Many vendors now offer dedicated private clouds, allowing companies to host their systems in isolated environments managed by the WMS provider, ensuring data separation. In terms of customization, solutions using microservices architecture allow clients to access enhanced adaptability through low-code/no-code configurations, making it easier to tailor the system to specific needs.
The long-term cost perception argument, often used against cloud solutions, deserves a closer look. While subscription costs can add up, cloud systems provide continuous updates, keeping the software current. This eliminates the need for costly migrations to new versions every few years—migrations that can sometimes cost as much as the initial implementation.
As supply chains become increasingly more complex and cyber threats become more sophisticated, cloud-based solutions are becoming more attractive. With SaaS innovations addressing perceived rigidity, cloud-based solutions are better equipped to handle unique business needs as they arise. Hybrid approaches, such as private cloud, are bridging gaps for organizations with specific security or operational needs.
Popular Industries That Require Warehouse Management
There are a variety of industries that require a WMS, and every industry will have a unique set of needs that a WMS will have to fulfill. A WMS must be adaptable and flexible to be able to handle a variety of differing business requirements, from retail to wholesale distribution to manufacturing. A WMS is most often implemented by one of the following industries:
Consumer goods: These companies use a WMS to gain real-time inventory visibility to track stock levels and help reduce shortages. They also use a WMS to support high-volume processing, season peaks, and demand surges. The WMS will typically also integrate with warehouse automation to assist with picking, packing, shipping, and reporting.
E-commerce: A WMS in e-commerce is used for effective order management so that companies may aggregate and organize shipments based on multiple characteristics, streamlining fulfillment. The WMS will also help companies with managing refunds, replacements, or restocking.
Food and Beverage: These companies rely on a WMS to adhere to strict regulatory requirements. It must provide smart record-keeping, robust lot and expiration date tracking, and advanced sensors to ensure product freshness and compliance. Food and beverage companies need traceability for recalls and regulatory audits and must be able to easily integrate with automated systems for optimized workflows and high-speed order processing and delivery.
Manufacturing: Manufacturers rely on a WMS to maintain tight control over their operations, ensuring efficiency from raw material storage to the final product. Real-time inventory visibility allows them to track materials through every stage—raw, in-process, or finished—while lot and batch tracking ensures compliance with stringent industry regulations and traceability requirements.
Retail: The most important feature of a WMS for a retail operation is its ability to provide real-time inventory tracking across multiple locations to prevent stockouts and overstocks. In addition, seamless integration with the business’ point-of-sale (POS) is a must, to ensure accurate order processing and fulfillment. Retailers also require advanced reporting, scalability, and support for omnichannel operations, like in-store pickups and online orders.
Third-Party Logistics (3PL): 3PLs require a WMS that seamlessly supports multi-client management so they can handle inventory from multiple customers in a single system. They also need real-time visibility into inventory and order status and a system that is easily customizable to meet the varying demands of different industries and clients. More importantly, 3PLs require a WMS that provides robust billing and reporting to manage the complex billing structure needed for every client they serve.
Wholesale distribution: These companies need inventory management, real-time stock tracking and order processing, and the ability to manage inbound and outbound logistics. A WMS is also useful for them to support the ever-fluctuating demand and business growth across multiple locations.
Important Stakeholders in Warehouse Management
The stakeholders in a WMS project include a diverse group of individuals and teams whose roles and responsibilities intersect with the system’s design, implementation, and operation. When selecting and implementing a WMS, it’s important to have a well-balanced roster of individuals in various departments of the business to ensure there are no blind spots. Here’s a breakdown of key WMS stakeholders:
Internal Stakeholders
- Executive Leadership: These leaders set the tone for the entire project. They approve funding, outline the big-picture goals, and ensure the WMS aligns with the company’s long-term strategy.
- Examples: CEO, CFO, CIO, COO, or VP of Operations.
- Supply Chain and Operations Teams: These are the boots on the ground when it comes to defining what the WMS needs to do. They know how the system should function day-to-day and what’s required to streamline operations.
- Examples: Supply Chain Directors, Warehouse Managers, and Operations Managers.
- IT and System Administrators: The tech experts are the ones who make everything click behind the scenes. From integrating the WMS with existing systems to managing data migration and ongoing updates.
- Examples: IT Directors, System Engineers, and Database Administrators.
- Warehouse Staff: Those who use the WMS daily play a massive role in its success. From receiving shipments to picking, packing, and shipping orders, they need a system that’s intuitive and reliable.
- Examples: Forklift operators, inventory clerks, and supervisors.
- Finance Teams: The finance team makes sure the WMS delivers on its promises. They monitor the budget, analyze cost savings, and track ROI to show the value of the investment.
- Examples: Controllers, Budget Analysts.
- Human Resources (HR): They organize training, manage workforce adjustments, and help navigate the challenges that come with automation.
External Stakeholders
- WMS Vendors: Vendors will provide software solutions, ongoing support, and system upgrades.
- Implementation Partners: These industry experts offer consulting services for system selection, customization, and implementation. They take on the task of overseeing the selection and implementation to ensure it goes well so you can focus on running your business.
- Third-Party Logistics Providers (3PLs): 3PLs will work to ensure compatibility if the WMS integrates with 3PL operations or is implemented in a 3PL facility.
- Suppliers and Vendors: These stakeholders will interface with the WMS for streamlined receiving processes and inventory tracking.
- Customers: Though they are indirect stakeholders, customers are the ones who benefit from improved accuracy, faster delivery, and better service enabled by the WMS. They are also the ones who will be most negatively affected should something go wrong.
- System Integrators and Hardware Providers: These professionals supercharge your WMS by supplying and integrating devices like scanners, RFID, printers, and conveyor systems into the system.
- Regulatory Agencies: Oversee compliance with labor laws, safety regulations, and industry standards.
Each stakeholder group has unique priorities, and successful WMS projects require collaboration and communication across all these roles to ensure alignment and smooth implementation.
Warehouse Management Trends to Watch
Businesses are focusing on having a more resilient, tech-driven, and sustainable supply chain in the years ahead, and effective warehouse management is one of the steps needed to work toward that goal. Warehouses are at the heart of supply chain operations, and the trends shaping their management reflect the broader push for agility, innovation, and responsibility. Below are the trends we’ll be looking out for in the years to come.
- Enhanced automation for greater efficiency
- AI and predictive analytics in warehouse management
- Sustainability in warehouse operations
- Collaborative and transparent supply chain networks
- Decentralized warehousing
- Risk management
Businesses that embrace these trends can ensure their warehouses are not only more efficient but better prepared to face the evolving demands of the modern supply chain. One thing is for certain, a WMS is an excellent step toward improved efficiency, transparent supply chain processes, and minimized risk. To find out which WMS is best for your needs, simply reach out.