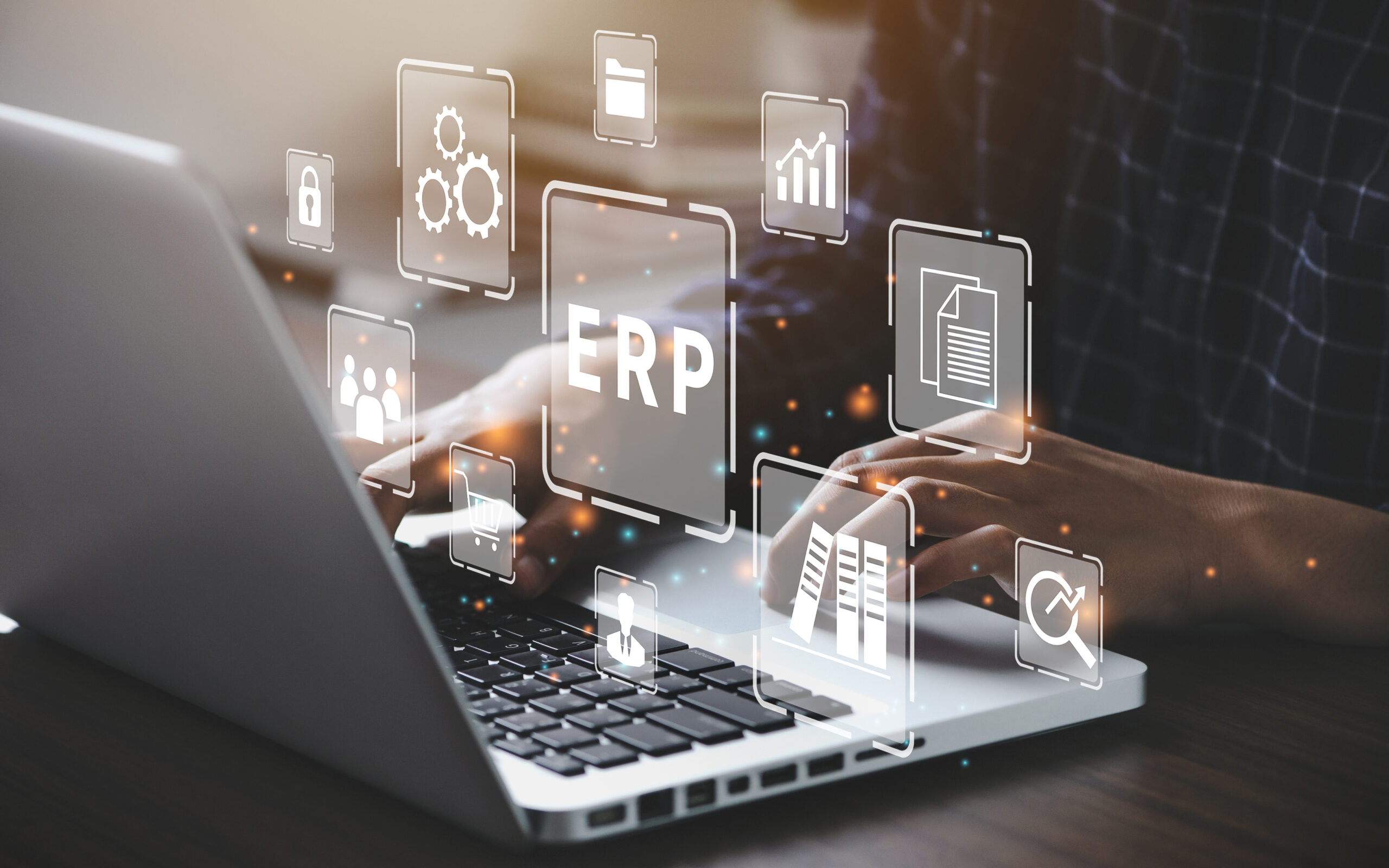
Choosing the right software for your supply chain operations can be a daunting task, especially as there are several types of Warehouse Management System (WMS) solutions available—standalone WMS, cloud-based warehouse management system, Integrated WMS with ERP, and Supply Chain Execution (SCE) Suites—each catering to different business needs. In this blog post, we’ll focus on two primary options: ERP and standalone WMS solutions. We’ll dive into the pros and cons of each, helping you determine the best wms for your organization. Curious which software is right for your supply chain? Read on to find out.
In this article, we’ll cover:
- What is an ERP system?
- What is a WMS?
- What is the difference between WMS and ERP systems?
- ERP vs. WMS: Finding the Right Fit for Supply Chain Operations
- Picking the Right WMS for Your Business
What is an ERP System?
An Enterprise Resource Planning (ERP) system is a type of software that organizations use to manage and integrate the essential parts of their business operations. An ERP system consolidates various business processes into one comprehensive system to streamline information and manage functions like:
- Finance and Accounting: Automating and managing financial transactions, budgeting, and reporting.
- Supply Chain Management: Overseeing procurement, inventory, production, and distribution processes.
- Human Resources: Managing employee information, payroll, benefits, and recruitment.
- Customer Relationship Management (CRM): Handling customer data, sales, marketing, and service activities.
- Manufacturing: Managing production schedules, quality control, and shop floor operations.
- Procurement: Overseeing purchasing processes and supplier management.
By centralizing these functions into a single system, an ERP allows for better visibility, coordination, and efficiency across an organization. It helps ensure that different departments can easily share information, leading to improved decision-making, reduced costs, and enhanced productivity.
What is a WMS?
A Warehouse Management System (WMS) is a specialized software application designed to optimize and manage the operations within a warehouse or distribution center. It provides tools for controlling and automating various warehouse processes, ensuring efficient management of inventory, labor, and space.
Key functionalities of a WMS include:
- Inventory Management: Tracking inventory levels, locations, and movements within the warehouse to ensure accurate stock control.
- Order Fulfillment: Streamlining the processes of picking, packing, and shipping orders to improve accuracy and speed.
- Receiving and Putaway: Managing the receipt of goods and their placement in the appropriate storage locations within the warehouse.
- Labor Management and MHE / Automation optimization: Optimizing workforce and MHE, automation and robotics allocation and productivity by orchestrating and tracking tasks and performance.
- Space Utilization: Efficiently organizing storage locations to maximize warehouse capacity and reduce handling times.
- Reporting and Analytics: Providing insights and data on warehouse operations, helping managers make informed decisions to improve efficiency.
A WMS integrates with other systems, such as ERP, Transportation Management Systems (TMS) and e-commerce solutions, to facilitate seamless operations across the entire supply chain. By automating and optimizing warehouse tasks, a WMS helps reduce errors, increase productivity, and improve overall warehouse performance.
What is the Difference Between WMS and ERP Systems?
The main difference between a Warehouse Management System (WMS) and an Enterprise Resource Planning (ERP) system lies in their scope, functionality, and focus within an organization:
1. Scope and Focus: WMS vs. ERP
WMS: A WMS is specialized software that focuses specifically on managing and optimizing the operations within a warehouse or distribution center. It handles tasks such as inventory management, order fulfillment, receiving, putaway, labor management, and space utilization. The primary goal of a WMS is to improve the efficiency, accuracy, and speed of warehouse operations.
ERP: An ERP system is a broader software solution that integrates various core business processes across an organization into a single system. It typically includes modules for finance, human resources, supply chain management, manufacturing, customer relationship management (CRM), procurement, and more. The goal of an ERP is to provide a unified platform for managing the entire organization, improving coordination and decision-making across different departments.
2. Functionality: WMS vs. ERP
WMS: A WMS focuses on detailed warehouse operations, providing advanced functionality for tasks like real-time inventory tracking, optimizing picking and packing processes, managing complex warehouse workflows, and integrating with material handling equipment.
ERP: An ERP offers a broader range of functions across various business areas but may include only basic warehouse management features. An ERP’s warehouse module might handle inventory tracking and basic order processing, but it typically lacks the advanced features and deep specialization of a standalone WMS.
3. Integration: WMS vs. ERP
WMS: A WMS often integrates with an ERP system to ensure that warehouse data is aligned with other business processes, such as accounting, purchasing, and sales. For instance, the WMS might provide real-time inventory data to the ERP for better stock management and order processing.
ERP: An ERP serves as the central hub for various business functions, including finance, HR, manufacturing, and supply chain management. While it can have a warehouse module, it often needs to integrate with a standalone WMS for companies that require advanced warehouse capabilities.
ERP vs. WMS: Finding the Right Fit for Supply Chain Operations
While both WMS and ERP systems are essential for managing business operations, a WMS is focused on the specific needs of warehouse management, while an ERP provides a broader, organization-wide management solution. Often, companies with complex warehousing needs will use both systems, with the WMS handling the detailed warehouse functions and the ERP managing overall business processes. Many companies start with an ERP and progress to adding a WMS when the ERP is no longer able to handle their distribution needs.
Use Case: WMS vs. ERP
A standalone WMS solution is best suited for organizations with complex or large-scale warehouse operations, where advanced functionality and real-time control over warehouse processes are critical. According to Patrick Prasinos, VP of Business Development at Made4net, “Today’s market is all about speed and agility. Businesses need warehouse management systems that are flexible and can easily handle three key tasks: prioritization, attributes, and workflows. Prioritization ensures agility by assigning orders their rightful urgency, while flexible attributes empower data-driven decision-making tailored to specific needs. Customizable workflows, free from the burden of hardcoding, unlock a realm of optimization and growth.” These types of tasks are enabled by tier-one warehouse management software that offer core WMS functions and advanced features such as cartonization, task interleaving, optimized scheduling, labor management, cycle counting, and more.
An integrated WMS with ERP is ideal for organizations looking to integrate all business processes into one system, providing a comprehensive overview of the entire organization. However, integrated systems may lack the specialized features or flexibility of standalone WMS solutions, potentially limiting the ability to adapt to specific warehouse operations or industry needs.
Companies often begin by relying solely on their ERP system to manage supply chain needs. However, as supply chain execution becomes more complex, ERP-level solutions alone may not be sufficient to address all the challenges. At this stage, the ERP serves as a crucial backbone, laying the foundation for the successful adoption of a Warehouse Management System (WMS).
When companies use both an ERP and a WMS, they benefit from a more structured environment. The ERP provides the necessary infrastructure, ensures data integrity, and integrates processes that enable the WMS to function effectively. Without a robust ERP system in place, a WMS is better able to deliver the efficiency, accuracy, and scalability required for modern warehouse operations.
Moreover, adopting a WMS opens up a new chapter of processes and functionalities that were not possible with just an ERP. This transition allows companies to tackle the advanced complexities of warehouse management, enhancing their overall supply chain execution. For a deeper understanding of these complexities, Made4net has reviewed the advanced dimensions of warehouse operations in the blog Warehouse complexity counts when you’re selecting a new WMS, indicating the 10 dimensions a WMS brings to the companies adopting this approach.
WMS vs. ERP: Market Overview
If you’re evaluating ERP or standalone WMS solutions, a great starting point is to review the top solutions in the Gartner® Magic Quadrant™ for Cloud ERP for Product-Centric Enterprises and the Gartner® Magic Quadrant™ for Warehouse Management Systems (WMS). These reports are invaluable resources for any company in the market for an ERP or standalone WMS solution. Supply chain technology leaders can use this research to understand the current state of the markets and gain key insights into recognized vendors.
Picking the Right WMS for Your Business
If your company operates multiple warehouse facilities, integrating all the necessary Supply Chain Execution processes into an ERP system can be a daunting task. This challenge is even greater when each facility varies in complexity, depending on the types of products and the clients they serve, and the regions they operate in.
One of the major issues is the lack of inventory visibility across different facilities. When some warehouses are managed by a full-fledged WMS while others rely solely on the ERP system, it can result in discrepancies in processing times and, more critically, variations in client service levels. This inconsistency makes it challenging to align customer experiences, as the fulfillment of products may vary significantly depending on which facility handles the order.
Most Warehouse Management System (WMS) solutions are designed to cater to specific segments or levels of complexity. They are typically equipped to handle the most sophisticated requirements, leaving the simpler and smaller sites to be managed by the ERP system. This approach, however, can create significant issues.
If your company’s operations involve a mix of smaller, less complex sites alongside more advanced warehouses, it becomes crucial to choose a solution that can handle all these levels effectively. The right WMS—whether that’s a SaaS WMS or an on-premise solution—should be adaptable enough to meet the needs of simpler environments while still providing the critical functionalities required for basic operations.
Additionally, it’s important to select a WMS that allows for different functional scopes at each location, ensuring that each site can operate efficiently according to its specific needs. At the same time, the WMS should maintain the benefits of a unified system, particularly global inventory visibility and customer experience standards which are essential for seamless operations across all facilities.
If a better understanding of ERP vs. WMS has led you to believe that a standalone WMS is the right choice for your business, there is still lots to consider when it comes to picking the right solution. The average lifecycle of a Warehouse Management System (WMS) typically ranges from 7 to 10 years, so it’s a big decision that will have lasting impact on your organization.
If you need support, check out our 2024 Warehouse Manager’s Guide to Picking a WMS or get in touch with one of our WMS experts.