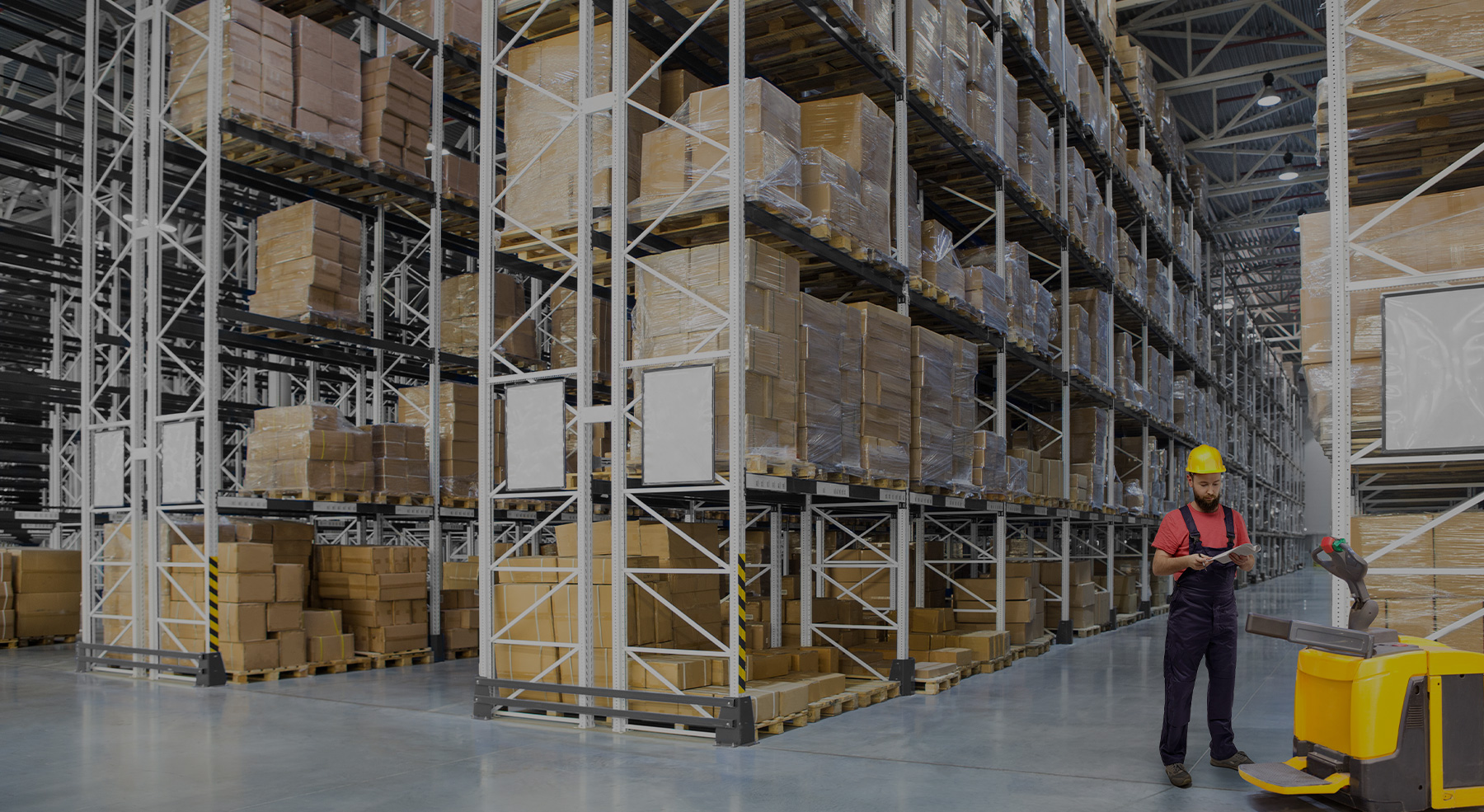
The best WMS for your business will unlock operational efficiency, increase productivity, and optimize your processes for success and growth. However, not all warehouse management systems are created equal. Getting the WMS selection right and then adhering to proper WMS implementation protocol is critical to ensuring the new tech will power your warehouse operations <effectively.
In this article, we’ll cover:
- What is a WMS Implementation and Why is it Important?
- How Long Does it Take to Implement a WMS?
- How Can You Effectively Implement a WMS?
- Understand Your Requirements
- Understand the Commitment
- Ask the Right Questions
- Commit to Training and Strong User Adoption
- Test
- Prepare for Change Management
- WMS Implementation is a Big Undertaking
What is a WMS Implementation and Why is it Important?
A WMS implementation is the process of setting up the software you’ll use to manage your warehouse. The implementation includes integrating with the rest of your tech stack, setting up relevant rules and processes in your WMS, and onboarding and training your employees.
There are many advantages and benefits to using a warehouse management system. But, it’s important to get your WMS implementation right from the beginning; otherwise, you risk hours or wasted time and frustrated employees working with a broken system to complete their tasks.
How Long Does it Take to Implement a WMS?
The length of time it takes to deploy a WMS implementation varies based on supply chain complexity, data quality, and required integrations, but on average companies spend between six to eight months on deployment. So, does that mean a WMS deployment is always costly and complex?
Thru-Put Partners Project Executive, Kevin Hume says it’s a mixed bag. “The answer is yes and no, quite honestly. I’m quite passionate about this. So yes, from the fact that any technology deployment has some level of complexity to it. The no component of that complexity is defined by the level of detail you have. You can take the most complex tasks and break them down into more discrete components that, in my opinion, don’t make them complex. So yes and no relative to complexity.”
The vendor you choose to go with will also have an impact on complexity and cost. While some WMS deployments take nine to twelve months or longer, Made4net’s cost-effective and rapid deployment process is based on a flexible, rules-based platform that supports a user-personalized implementation for an average go-live time of about 20 weeks.
With regard to the expense, Hume states, “If you’ve done an appropriate business case, you’ve identified the value, and you’ve justified the investment that you’re going to make in this initiative. But absolutely, a WMS implementation is expensive. It’s a cross-functional task. It’s going to pull resources across the organization. It’s going to bring in technology providers. There’s also a tremendous amount of risk to it as well, but it’s all about tying it back to that business case and the value to execute that plan.”
How Can You Effectively Implement a WMS?
In addition to Hume, we tapped three more industry experts for their tips on a successful WMS implementation. Collectively, these industry veterans have implemented software and automation in hundreds of warehouses, solving distribution challenges for their customers. Their list of challenges encountered is long and their methodologies run deep. Here’s their top advice are the top missteps to watch out for with your software implementation.
WMS Implementation Tip #1: Understand your requirements
Director of Services and Alliances for Bricz, Tyler Linderman, believes, “you cannot start a WMS selection [and implementation] project if you don’t have your own business requirements documented in a well and easy-to-read fashion.” Having clear insight into your requirements is critical in ensuring the WMS you invest in achieves all your goals while setting you up for future growth. He recommends visiting all buildings in your operation, establishing what requirements there are, and creating a master document that can be shared with any WMS vendor for clarity.
He also encourages companies to think beyond the present and plan for the next 5, 10, 15, and 20 years. Technology changes very fast, so you need to be planning around the features and functionality you might need down the road. How a system integrates with robotics and automation or various parcel shipping providers may not matter currently, but this could be very important in the future.
WMS Implementation Tip #2: Understand the commitment
We may be stating the obvious, but implementing a WMS is a big commitment, which means planning is of the utmost importance. For Supply Chain Advisor, John Sidell, the number one need is “understanding the commitment that you as an organization are making for deployment.” This means “vetting the right vendors to make sure that the requirements you have as an organization align nicely with the capabilities of that software package.”
This goes hand in hand with having the right team on board for the process. Creating an internal resource plan that includes insight from the entire organization including your warehouse team, your IT group, and executive leadership is crucial. Neglecting this step is often what leads to delays and complications down the line.
WMS Implementation Tip #3 Ask The Right Questions
It’s important to come prepared with the right questions to ensure there’s nothing missed during the process. What questions should you ask for a successful WMS implementation?
- Do you have relevant implementation experience in my industry? Look for a vendor with a background in your specific industry; this will yield a higher quality experience for you.
- Can you handle core WMS functions as well as any advanced features required in my operation? This includes cartonization, task interleaving, optimized scheduling, labor management, cycle counting and more.
- Can you integrate with my ERP? Your WMS needs to be interoperable with your ERP. One way to ensure ease of integration is to determine whether or not a WMS is built around an open architecture. (Understand the difference between ERP vs. WMS.)
- What’s the average implementation time and average number of modifications required during an implementation?
- What level of service will I receive during the implementation and after go-live?
- Will you be in business in a decade? The average lifespan of a WMS is 8-10 years. Research a vendor’s solvency to ensure they’ll remain in business well into the future.
- Can you support my unique needs? Be prepared to discuss any unique challenges to your business, and keep in mind future growth and expansion plans.
WMS Implementation Tip #4: Commit to Training and Strong User Adoption
WMS solutions are complex and gaining the requisite knowledge takes time and requires hands-on involvement in the software implementation process. Sidell shares that, “Training starts at the beginning of the project and continues throughout – from initial vendor software orientation and setup / configuration training, to design discussions, conference room pilots, configuration of the software by operational project team members, development of standard operating procedures, training program development, supervisory and end-user training, testing and startup support.”
The goal is to train the users within one week of go-live by utilizing multiple trainers to ensure the information is fresh and training is comprehensive. This also provides the added benefit of reassuring that the trainers are prepared and ready to support their teams at go-live. It exponentially shrinks the ramp up time and improves the time to ROI realization. Project leaders should consider including tests or exams as part of the training process to verify the users truly understand the capabilities and use of the system.
Several experts stressed the importance of having your staff involved in the hands-on training. “Training is a process, and final end-user training and the education of the supervisory leads should be developed and conducted by company resources,” said Sidell. “In order to help facilitate company-wide acceptance of the new system, the operations team needs to play an active role.”
WMS Implementation Tip #5: Test!
The importance of testing came up with every one of our experts. The rule of thumb: test the system and then test it again. Below are some of the areas that need to be tested. Often, these areas are managed by separate groups of people and skill sets.
- Testing – End-to-End Validations
- Test data – Ensure that the data you are testing is validated and accurate. This would include; Item Master, including all critical dimensions for every available Unit of Measure that will be received, stored, picked and shipped. This becomes even more critical when using dimensional data for key WMS functions, such as Order Cubing, Putaway Algorithms, Replenishment Levels, etc.
- System and Integration Testing – Integration is often the “long pole” in the tent. If integration between systems (WMS, TMS, LMS, ERP, etc.) is compromised, the Implementation will fail.
- Volume Testing – Oftentimes, testing is done with only a small subset of orders, receipts, etc. Make sure that you “stress” the system with volume tests to ensure that all systems and interfaces will “hold the load.”
- Include a “day in life” test scenario – prepare a day’s worth of real data which can be used to cross test the system, end to end (data, integration, processes) and include your key users (shift leads) to validate the test results.
- User Acceptance Testing (UAT) – Often overlooked, or saved until last, most go-lives struggle because there was not enough User Testing. Confidence in the system will likely fail if you have not engaged the actual users.
“Every company plans some level of testing,” explains Sidell. “What’s often missed or not fully considered during the development of the implementation testing plans are the testing the organization is required to perform; the effort it takes to prepare granular test scripts and/or testing mechanisms; the level of documentation required; and the resources and man-hours required to perform each level of testing.”
You need an adequate timeline for testing. If you rush, you can go in with a defective project. And integration testing is when things can really start to fall apart with a snowball effect.
WMS Implementation Tip #6: Prepare for Change Management
Preparing staff for change is far more than just training. People can be naturally resistant to change and may be worried about their job security. Software implementations frequently impact staffing levels, roles, responsibilities and sometimes pay scales. Failure to deal with human resources-related changes may impact user adoption.
“Resistance to change is common because certain people are entrenched in processes and they may be afraid or worried,” said EnVista’s Senior Director of Technology Christian Nixel. “There is a concern for job security and worry whether they will still be relevant. Some people may even sabotage the project. There are other changes to consider, as well. Are you going to a new building? Are you changing shifts? Whose lives get changed? Are there changes to seniority? Identify the obstacles to change and then determine your paths to adopting.”
Sidell commented that many WMS project charters fail to recognize the need for change management until late in the project, or simply believe that change can be managed through training alone.
“New software impacts not only the distribution center (DC), but other departments in the company, as well as customers, carriers, and suppliers,” said Sidell. “Additionally, most organizations must meet inbound, outbound, labor and other key performance indicators (KPIs) during the transition, or shortly thereafter.”
WMS Implementation is a Big Undertaking
It’s undeniable, implementing a new WMS is a big undertaking, but you don’t have to go at it alone. We’d love to help you calculate the ROI of your investment and provide other advice that can get you started off on the right foot.
For more expert advice on current and future supply chain issues, check out our Ask the Expert Series recorded at ProMat. Check out our tips for improving warehouse efficiency here.
And, learn how to choose a warehouse management system that’s perfect for your needs.