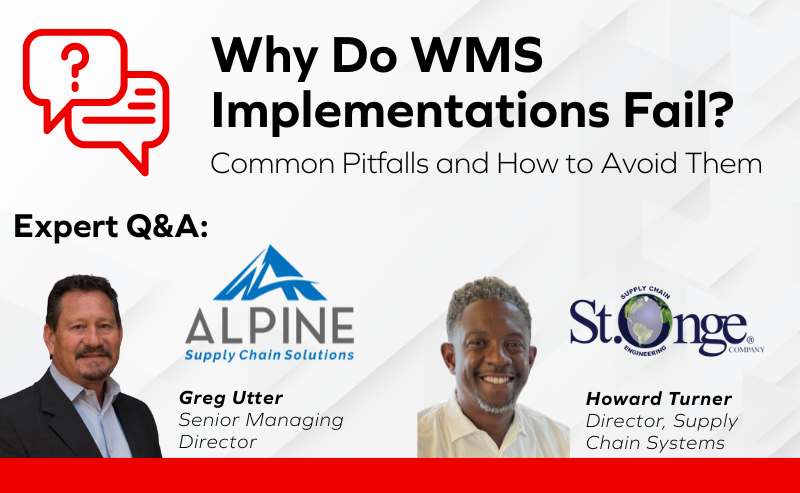
Warehouse Management System (WMS) investments are on the rise as companies look to modernize operations, improve efficiency, and better manage growing complexity across their supply chains. But while the right WMS can unlock major gains in productivity and performance, these projects are far from plug-and-play. From over-designing the solution to misjudging integration needs, there are several pitfalls that can derail ROI and delay value realization.
In this Q&A-style post, two experts share real-world lessons and reveal the most common missteps companies make during WMS selection and implementation—and how to avoid them. Whether you’re just starting your search or already mapping out your project plan, their insights can help you stay focused, aligned, and set up for long-term success.
Q: What are some of the biggest pitfalls during WMS selection and implementation?
Howard Turner, Director Supply Chain Systems, St Onge
- Overdesigning the system: Trying to solve every rare or historical edge case leads to complexity and scope creep. It’s critical to focus on core functionalities first and avoid building in solutions for every “what if” scenario outside your immediate warehouse operations.
- Lack of a well-rounded project team: A WMS impacts multiple parts of a business — not just IT or operations. Without including cross-functional representatives (finance, customer service, leadership, and especially warehouse floor workers), important needs can be missed, and buy-in suffers.
- Poor design workshops: The initial design sessions set the foundation for how the system will operate. If these workshops are rushed or poorly structured, you risk building a solution that doesn’t fit your real needs or validate the vendor’s approach adequately.
- Unrealistic goals: Expecting 100% productivity on day one is a recipe for disappointment. There is always a ramp-up period after go-live, so set achievable milestones and prepare for an adjustment phase.
Q: How important is it to have a well-defined project team with clearly understood roles and responsibilities during a WMS implementation—and how can this impact the success of the project?
Greg Utter, Senior Managing Director, Alpine Supply Chain Solutions
Vital. Create a detailed RACI matrix (Responsible, Accountable, Consulted, Informed) early on to clarify who does what. This exercise often helps clients quickly realize they likely don’t have enough people to fill all the roles required for the project’s success.
Q: What is one of the top mistakes you see companies make during WMS implementation?
Greg Utter, Senior Managing Director, Alpine Supply Chain Solutions
A common mistake is not involving warehouse floor workers early enough in the process. Because implementing a new system brings significant change management challenges, it’s vital to include the people who will actually be using the system from the start. Bringing them in early helps address their concerns and ensures smoother adoption, as they better understand how the new WMS will affect their daily tasks and roles.
Q: What additional benefits does involving warehouse workers early in a WMS project offer?
Greg Utter, Senior Managing Director, Alpine Supply Chain Solutions
From experience, we’ve seen many cases where warehouse workers describe how operations actually run—but when this information is shared with leadership, there’s often a complete disconnect. Sometimes, leadership isn’t even aware of how tasks have been handled for years right outside their office doors. Involving floor workers early ensures you get an accurate and realistic picture of your true requirements, which is crucial for a successful implementation.
Q: What are your top tips for avoiding the common missteps that can derail a WMS project?
Howard Turner, Director Supply Chain Systems, St Onge
- Keep the scope focused on core needs, not every edge case
- Run thorough well-planned design workshops to define and validate requirements.
- Set realistic, phased goals for implementation and productivity.
Greg Utter, Senior Managing Director, Alpine Supply Chain Solutions
- Develop a RACI matrix to align responsibilities and commitments.
- Build a diverse, cross-functional project team early, including warehouse staff.
Ready to learn more?
Watch the full conversation: Let’s Talk WMS: 2025 Gartner® Magic Quadrant™ Findings and Market Analysis.