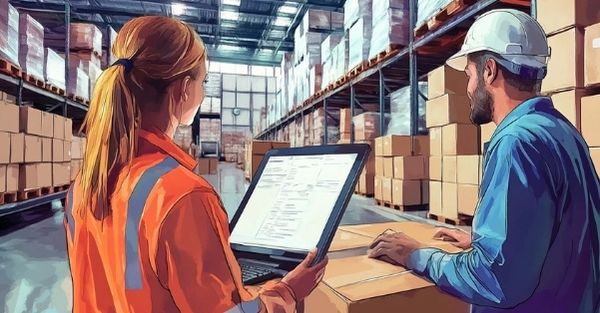
A warehouse management system (WMS) is the brain of a distribution center, powering the backbone of efficient warehouse management. In this post, we’ll cover the purpose of a WMS solution, common challenges a WMS helps tackle, how a WMS system works, core system features and more.
- What Does WMS Stand For? What Does WMS Mean?
- What is a Warehouse Management System (WMS)?
- What is the Purpose of a Warehouse Management System?
- How Does a Warehouse Management System (WMS) Tackle Top Challenges?
- What Does a Warehouse Management System Do? How Does it Work?
- Conclusion
What Does WMS Stand For? What Does WMS Mean?
The definition of a warehouse management system or WMS is as follows: Software designed to optimize and manage warehouse operations, including inventory tracking, order fulfillment, and labor management, to improve efficiency and accuracy.
What is a Warehouse Management System (WMS)?
A WMS solution plays a pivotal role in supply chain operations, overseeing everything from receiving goods to shipping them out. A WMS system provides businesses with real-time visibility into inventory, both on-hand in the warehouse and in transit. With a wide range of tools for tasks like picking, packing, and analytics, it helps companies optimize workflows, reduce errors, and enhance overall productivity.
What is the Purpose of a Warehouse Management System?
We like to view a WMS solution as “command central” for modern distribution centers, responsible for running the show and doing everything possible to improve inventory visibility, optimize picking, increase labor efficiency and minimize errors.
What Are Common Challenges in Warehouse Management?
Managing a warehouse is no easy task and presents a wide range of daily challenges. These obstacles can create significant disruptions in operations, impacting both productivity, efficiency and customer satisfaction. A few common warehouse management challenges are:
- Inaccurate order fulfillment: Errors in picking, packing, and shipping can result in increased returns, unhappy customers, and missed sales opportunities. These mistakes often stem from relying on manual processes or managing large, complex SKU volumes.
- Receiving and putaway bottlenecks: Lack of coordination between the receiving and storage departments in a warehouse can often lead to delays in productivity.
- Season fluctuations: Scaling operations during peak season isn’t always easy. Without the appropriate staffing, warehouses end up dealing with backorders, delayed shipments, and an overwhelmed staff.
- Omnichannel complexity: Businesses offering omnichannel order fulfillment must contend with more complex inventory tracking, returns management, and order fulfillment, as each channel may have different requirements.
- Ongoing labor shortage: Labor shortages, especially in areas with low unemployment, create challenges in hiring and retaining skilled warehouse employees. Labor expenses can make up 70% of the total warehouse budget, which means high turnover further increases training costs and reduces productivity.
With so many different aspects to take care of, it’s clear that manual warehouse management processes aren’t enough to empower businesses to grow and thrive. This is where a warehouse management system comes in. By automating some of the most critical aspects of the warehouse, businesses can keep track of all operational details and overcome the many challenges associated with warehouse management.
How Does a Warehouse Management System (WMS) Tackle Top Challenges?
A WMS solution addresses top warehousing challenges in several ways:
- Inventory Accuracy: WMS systems improve inventory tracking by using real-time data, reducing human errors and ensuring precise stock counts, which minimizes stockouts and overstocking.
- Order Fulfillment Speed: With features like automated picking, packing, and routing, a WMS streamlines order fulfillment, accelerating processing times and improving delivery efficiency.
- Space Optimization: A WMS solution maximizes warehouse space by recommending the best locations for storage based on item popularity and dimensions, making it easier to manage high-volume inventory.
- Labor Efficiency: By optimizing workflows, providing task prioritization, and tracking performance, a WMS system reduces manual labor, improving worker productivity and reducing operational costs.
- Scalability: A WMS adapts to growing business needs, handling increased order volumes and more complex supply chain operations without requiring a complete overhaul of the system.
What Does a Warehouse Management System Do? How Does it Work?
The core functions of a WMS system add up to create a robust system that operations can rely on to run their warehouse processes. The way a WMS solution works will vary based on the system selected, but they will all follow this general flow:
- First, the WMS solution oversees inventory levels to ensure that the correct quantity of each product is available for order fulfillment. Through advanced automation, it tracks the movement of goods throughout the facility in real time, enabling precise inventory tracking.
- Next, the WMS software manages tasks by assigning activities to warehouse staff based on their roles, expertise, and current workload. This ensures that each person is working on the right job at the right time, reducing delays and minimizing errors. The system also monitors staff performance, helping to identify training needs or areas where additional staffing may be required.
- The WMS assigns a unique digital identifier to every bin, pallet, and product in the warehouse, making it easy to locate items at any moment. It verifies that the correct items are picked for shipment and generates labels to keep items clearly identifiable.
- Finally, the WMS system optimizes storage and shipping with cartonization functionality, which helps determine the best way to store and package items. This maximizes space utilization and can significantly reduce shipping costs.
What Are the Core Features of a Warehouse Management System?
When it comes to WMS solutions, there are various solution tiers. While some systems offer basic inventory management, others include advanced capabilities such as cartonization, task interleaving, optimized scheduling, labor management, cycle counting, and more. Regardless of complexity, we believe a WMS system should offer the following core functionality:
- Inventory Management: Provides real-time tracking and management of inventory levels, encompassing all stages of receiving, putaway, and storage within the warehouse.
- Order Management: Oversees the full order process, from picking and packing to shipping, ensuring precise and prompt order fulfillment.
- Receiving and Putaway: Streamlines inbound logistics by optimizing the receipt of goods and guiding items to optimal storage areas based on warehouse layout and space availability.
- Picking and Packing: Enables effective picking and packing operations, incorporating various strategies like wave, batch, and zone picking for increased efficiency.
- Shipping and Transportation Management Integration: Supports outbound logistics by coordinating shipments and often linking to transportation management systems (TMS) for seamless delivery management and shipment tracking.
- Barcoding and Scanning Integration: Enhances accuracy by using barcode scanning and RFID technology, allowing for reliable tracking of goods throughout each warehouse process and reducing the risk of human error.
Conclusion
We hope this post answered the question, “What is a WMS?” While much has changed since warehouse management systems first emerged in 1975, they remain the backbone of warehouse operations. No matter how much automation, robotics, or artificial intelligence (AI) companies bring into their fulfillment centers, a WMS system is essential to orchestrate every step of a product’s journey—from its arrival onsite to its final load onto a delivery truck. If you’d like to see Made4net’s powerful, tier-one warehouse management software in action, contact one of our experts today.