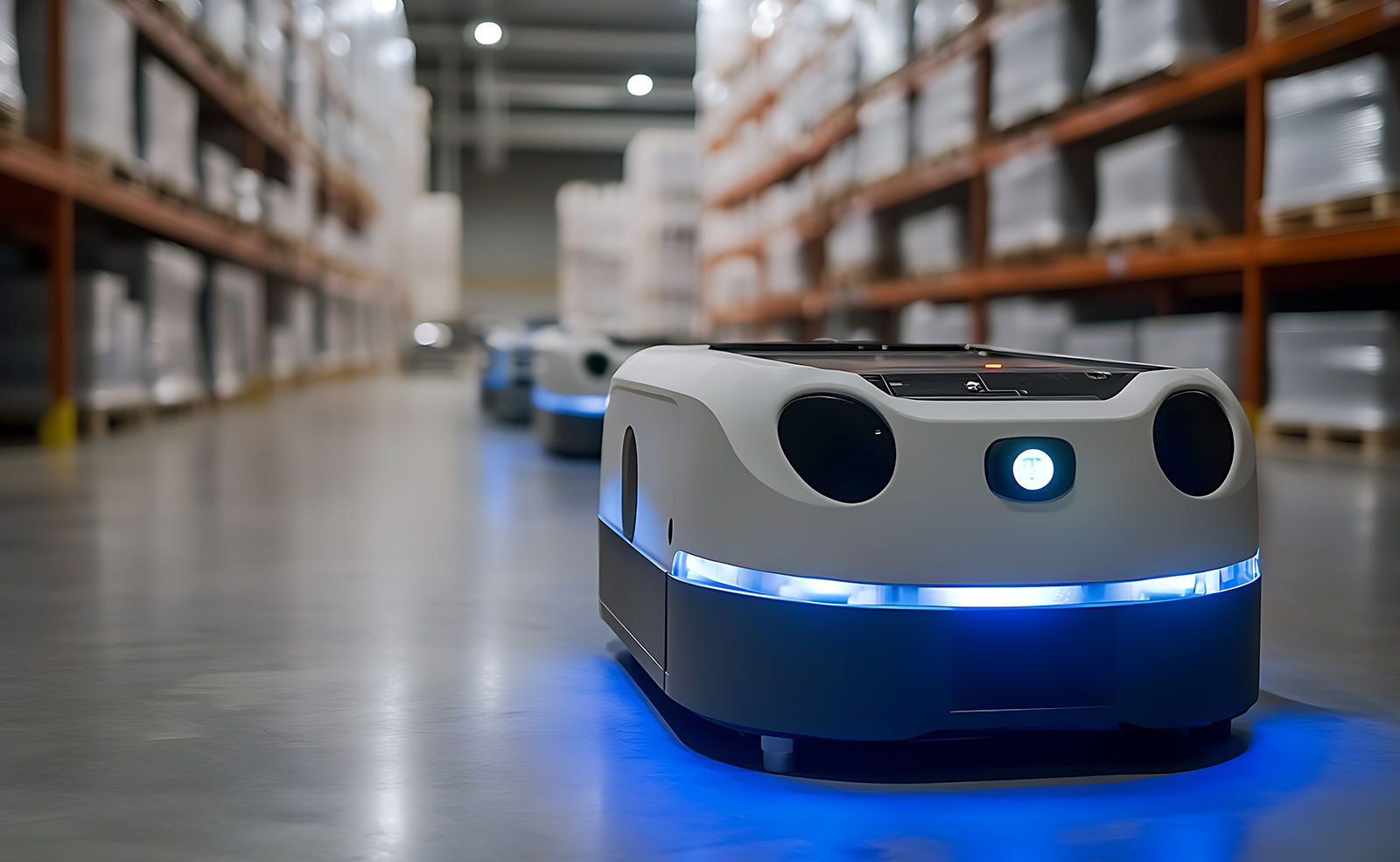
Warehouse operations are the backbone of any successful supply chain, ensuring goods are efficiently received, stored, picked, packed, and shipped. As warehouses adapt to evolving industry demands, understanding and optimizing these operations is key to staying competitive in today’s fast-paced logistics environment. From leveraging a warehouse management system (WMS) to implementing clear Standard Operating Procedures (SOPs), warehouse operations are not just about moving goods—they’re about creating a seamless, efficient ecosystem that supports broader business goals.
In this article, we’ll cover everything you need to know about warehouse operations, including:
- What is Warehouse Operations?
- 7 Warehouse Operations Processes
- What is Warehouse Operations Management?
- Warehouse Operations Job Descriptions and Responsibilities
- What is Standard Operating Procedure (SOP) at a Warehouse?
What is Warehouse Operations?
Warehouse operations is the term used to refer to all the components in a warehouse that work together to keep the operation running, including storage, inventory management, order fulfillment, etc. Warehouse operations are critical to the broader supply chain and have a direct impact on efficiency, customer satisfaction, and profitability. Key examples of warehouse operation activities are receiving, putaway, picking, packing, and shipping.
7 Warehouse Operations Processes
While warehouses will differ based on industry, geography, and size, almost all of them are responsible for a standard set of core processes. These processes all feed into one another to create a working ecosystem that guides a product’s journey throughout the supply chain.
The seven core warehouse processes include:
- Receiving: Goods inspection, unloading, and reconciliation with purchase orders.
- Putaway: Efficiently storing items in designated areas to optimize space.
- Inventory Management: Cycle counting, inventory accuracy, and replenishment.
- Picking: Types of picking (e.g., wave picking, batch picking).
- Packing: Ensuring items are packaged securely and labeled correctly.
- Shipping: Carrier management, routing, and dispatch.
- Returns/Reverse Logistics: Handling returns and restocking or disposing of products.
These tasks are most successful when there are systems in place to ensure they are integrated to share relevant data. This allows for efficient workflows, the elimination of double work, and greater accuracy. With the right tools in place, warehouse operations can be how an operation stands out from its competition.
What is Warehouse Operations Management?
Warehouse operations management includes the planning, organizing, and optimization of daily activities. Strategies for effective management involve:
- Process Streamlining: Use flowcharts and checklists to eliminate unnecessary steps.
- Capacity Planning: Align labor and storage space with fluctuating demands, like during peak seasons.
- Labor Management: Incorporate strategies like shift optimization, cross-training, and performance tracking.
- Technology Integration: Use tools like a WMS to automate repetitive tasks and provide real-time insights.
To determine whether your warehouse operations management is hitting the mark, it’s important to establish and measure against objective Key Performance Indicators (KPIs). Some KPIs to consider are:
- Order Accuracy Rate: Percentage of orders shipped correctly.
- Storage Utilization: Percentage of warehouse space being utilized effectively.
- Dock-to-Stock Time: Time it takes to receive and store goods.
- Inventory Turnover: A measure of how quickly inventory is sold and replaced.
- Fulfillment Speed: Time from order receipt to shipping.
- Damaged Goods Rate: Percentage of items received that are damaged.
- Days on Hand (DOH): Average number of days inventory is held before being sold or used.
- Lines Picked Per Hour: Number of order lines picked by employees per hour.
- Packing Accuracy: Percentage of orders packaged correctly, without damage or errors.
- Employee Turnover Rate: Percentage of employees leaving the warehouse over a given period.
Not all KPIs will be relevant to every warehouse. Select KPIs based on operational goals, technology capabilities, and customer service level agreements. A balanced set of KPIs ensures comprehensive tracking and helps drive continuous improvement in warehouse operations.
Automating Warehouse Operations
Warehouse automation is a critical component of warehouse operations management. Automation is revolutionizing warehouse operations by fostering a more streamlined process, thus reducing costs and improving accuracy. The most impactful tools of the day include:
- WMS: A robust WMS optimizes inventory management, order processing, and labor allocation. It provides real-time visibility into operations, ensuring smoother workflows and quicker decision-making.
- Robotics: Robots are transforming tasks like picking, packing, and sorting. Autonomous mobile robots (AMRs) navigate warehouses to retrieve and transport items, reducing reliance on manual labor.
- Conveyor Systems: Conveyors automate the movement of goods within the warehouse, improving efficiency in sorting and shipping. They are especially valuable for high-volume operations.
- Automated Guided Vehicles (AGVs): AGVs transport pallets or goods across the facility using pre-programmed paths or advanced navigation systems, minimizing bottlenecks and maximizing productivity.
The main point of automation is to reduce the amount of low-value manual tasks an operator needs to complete so they are free to perform more critical tasks, like picking items or performing value-added services. It allows employees to perform tasks that can’t be delegated to an automation solution, such as:
- Inspecting for damage or quality control checks on items that require visual judgment
- Picking and packing fragile items that require careful handling
- Adapting to unexpected situations like damaged packaging or incorrect inventory counts
- Breaking down and rebuilding boxes for specific packing needs
- Managing customer-specific packing requests with unique requirements
- Identifying and resolving inventory discrepancies or missing items
- Complex product assembly or customization that requires human dexterity
- Responding to rapidly changing orders or product layouts
Leveraging Data Optimization in Warehouse Operations
Data optimization is an excellent strategy for warehouses to improve order accuracy and fulfillment speed. With technologies such as IoT-enabled sensors, RFID tags, and WMSs, warehouses can monitor inventory levels, track goods throughout the facility, and instantly identify discrepancies. Real-time tracking and live visibility into operations support dynamic decision-making, empowering managers to reallocate resources as needed to address bottlenecks as they arise.
Advanced WMS solutions provide operations with dashboards and advanced reporting tools, which present warehouse managers with a clear overview of KPIs and operational metrics. For example, a dashboard might highlight picking delays in a specific area, prompting a review of that workflow. Data becomes even more valuable when paired with machine learning, which can go a step further to uncover patterns to make tailored recommendations. Machine learning can identify recurring inefficiencies, such as high error rates in certain picking zones or excess travel time for specific SKUs.
Predictive analytics, real-time data tracking, and machine learning tools provide warehouses with a competitive edge by enabling smarter, faster, and more efficient decision-making.
Improving Warehouse Operations
There are various ways to improve warehouse operations efficiency and productivity. Automation is a key area to explore, and it’s no longer a “nice to have” but a necessity in today’s fast-paced logistics environment. From streamlining workflows to reducing errors, automation will remain a cornerstone of operational success as technology continues to evolve. Other ways to improve warehouse operations include:
- Wage improvement: Your labor force is your operation’s most valuable asset, they must be treated as such. Paying your workforce what they are worth is critical to hiring and retaining valuable talent who will be with you for the long haul. Employees are far more likely to stay with a company that demonstrates its appreciation for their work in tangible ways. If a similar operation offers better pay, workers won’t hesitate to move to where their efforts are better recognized and rewarded.
- Gamification: Incentivise your workforce to go above and beyond with gamification in the warehouse. A gamified experience will add levity to the workday, and offering fun prizes to compete for will only up the stakes. Having employees compete for extra vacation days, a new TV, or flexible time off is an excellent way to motivate employees, foster team building, and show employees they’re valued.
- Cross-training: Encourage employees to explore other roles within the warehouse. Cross-training provides workers with a broader understanding of operations and can increase flexibility during peak times. It also demonstrates your commitment to their professional growth, which can boost morale and reduce turnover.
Other ideas involve partnering with a 3PL, implementing lean strategies, and periodically checking in with employees to learn what suggestions they may have. Their day-to-day experience on the floor can provide you with valuable insights to ensure you’re not missing out on productivity enhancements they could really use.
Warehouse Operations Job Descriptions and Responsibilities
While technology plays a critical role in how well a warehouse functions, the people who run the shop are just as important. Their expertise guides the entire operation. The three main operational roles a warehouse depends on are:
The Warehouse Operations Supervisor is responsible for managing teams on the ground, ensuring employees meet daily performance goals and that schedules are properly coordinated. They serve as the first line of defense for troubleshooting issues, whether it’s a system error or a workflow bottleneck, and play a pivotal role in maintaining morale and productivity.
The Warehouse Operations Manager oversees processes such as receiving, putaway, picking, packing, and shipping to ensure operations run smoothly and efficiently. They are also tasked with ensuring compliance with safety regulations and protocols and monitoring KPIs to identify areas for improvement to drive operational success.
The Director of Warehouse Operations is focused on the strategic alignment of warehouse activities with broader business goals, such as resource allocation, budgeting, and implementing long-term plans to enhance operational performance. They oversee the implementation of new technologies and ensure innovations align with company objectives.
What is Standard Operating Procedure (SOP) at a Warehouse?
SOPs in a warehouse are structured guidelines that define how specific tasks should be performed to ensure consistency, safety, and efficiency. They act as a foundational framework for day-to-day operations, enabling teams to perform tasks with minimal confusion while adhering to regulatory and safety standards. SOPs empower warehouses to remain adaptable in an ever-changing industry.
In a dynamic warehouse environment, SOPs help streamline processes, minimize errors, and maintain operational continuity—even when onboarding new staff or facing fluctuating demands. Key components of effective SOPs include:
- Detailed information on why a specific process is vital to the operation.
- Step-by-step instructions to ensure tasks like picking, packing, or shipping are executed with precision.
- Clearly defined roles and responsibilities so every team member understands their part in the process and how their work aligns with the operation’s goals.
- Safety protocols, such as adhering to OSHA standards, to help prevent workplace injuries and ensure compliance with legal requirements.
Regular reviews and updates of SOPs are essential to address changes in technology, regulations, or operational needs. Performing an annual audit of SOPs is good practice, though it’s also recommended SOPs be reassessed after certain milestones, such as following a technology or process change, after a safety incident, during significant operational shifts, or when regulations or standards change.
Conclusion
Running a warehouse takes impeccable organization, teamwork, and a willingness to keep learning and growing. Efficient warehouse operations are critical to a company’s ability to deliver value to its customers while maintaining profitability. By streamlining workflows, leveraging technology, and fostering a skilled and motivated workforce, warehouses can achieve operational excellence.