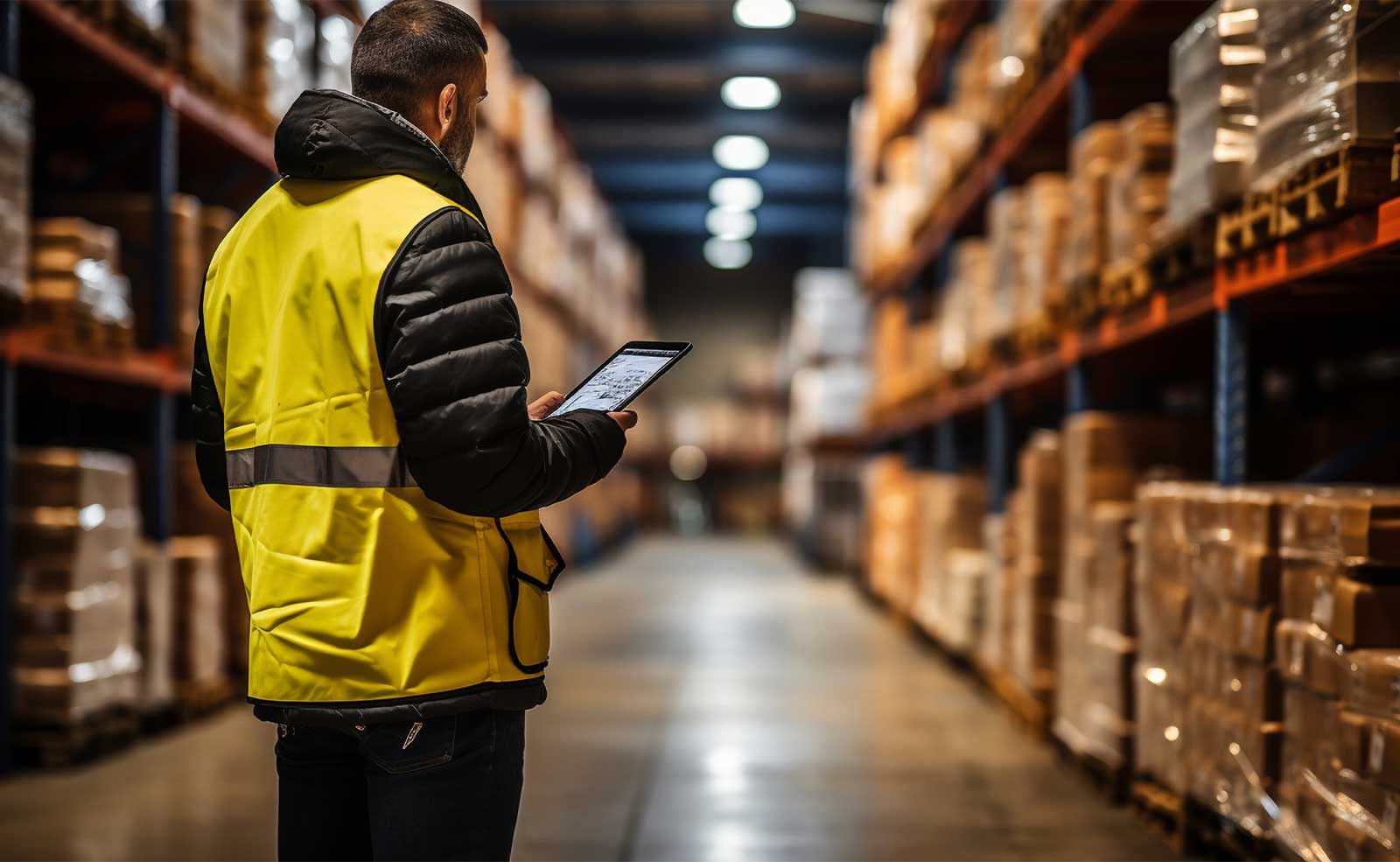
In today’s ever-changing business landscape, the efficiency and adaptability of your supply chain execution are critical for staying competitive. International supply chain incidents have demonstrated that every business is interconnected, where a single issue halfway across the globe can impact your operations for months. This networked world presents both opportunities and challenges. To thrive, businesses must build flexible organizations that adapt effortlessly to changing environmental conditions.
The retail and product distribution landscape has evolved dramatically, transitioning from the “Field of Dreams” approach to the dynamic omnichannel era, where companies must be omnipresent, offering products and services seamlessly, with short delivery windows and high order volumes. This means today’s market is all about speed and agility, and Warehouse Management System features need to be flexible, and easily handle three key tasks: prioritization, attributes, and workflows.
Prioritization
Prioritization gives you the ability to react differently to different types of orders. When done right, prioritization can lead to a seamless integration of various activities, creating a process that allows more important tasks to take precedence. For example, an e-commerce order with a 4-hour delivery window will have different prioritization requirements than one with a 2-day delivery window, altering how a WMS should manage one order over another. Seeing as 26% of retail purchases are expected to happen online by 2026, operators, equipment, and processes must keep evolving to meet demand, and that starts with prioritization.
Prioritization should be addressed at the WMS level to ensure adaptability. However, not all WMS solutions are created equal when it comes to prioritization. Simpler WMS platforms often have priorities hardcoded into their systems. While this approach may work initially, it can prove to be an Achilles’ heel in a rapidly changing operational landscape.
For example, consider a highly automated warehouse that embeds prioritization logic into their integrated hardware and software systems. If these priorities cannot be modified, accommodating new or additional client requirements becomes a formidable task. The resulting changes can be not only costly but also time-consuming, making it challenging for managers to advocate for system modifications that may only be relevant for a short period in a dynamic environment.
Made4net offers a WMS solution that delivers configurable and adaptable priority levels for tasks, clients, vendors, orders, resources (human or otherwise), space, equipment, and more, positioning our customers to meet evolving challenges and opportunities presented by today’s dynamic market.
Attributes
Attributes are a set of parameters that serve as a means to categorize and differentiate various data elements based on their unique characteristics. The ability to associate attributes with items, orders, tasks, and more provides a powerful tool for simplifying decision-making and maintaining a sharp focus on your operations. When attributes are designed with flexibility in mind, they become the linchpin for adapting processes to new requirements.
Attributes play a critical role in WMS, not only by allowing users to filter data in different ways to fulfill orders but also by offering the versatility to accommodate changing needs as they arise. Simple WMS platforms limit attributes to the item level, with each item having a predefined set of attributes associated with it. These attributes may not be shared across multiple items or categories, restricting the system’s adaptability to evolving demands.
A WMS with strong attribute management capabilities will enable users to easily associate multiple units of measure (UOM) with a single item. More importantly, it will enable users to link attributes to specific portions of inventory, a feature particularly valuable when requirements change from one shipment to the next.
Imagine a scenario where a company manages the same item in various units of measure or packs. Top WMS systems with robust attribute management capabilities will enable users to sort, filter, and even “convert” items into manageable packs tailored to specific needs. This capability aligns with the “Receive in every pack size, and ship it in your way” approach sought after by many e-commerce operations.
Made4net offers a WMS solution with robust attribute management capabilities that can manage an unlimited number of attributes at both the item and inventory levels. This includes a hierarchical attribute structure, a game-changer for warehouse management.
Workflows
A workflow is a pre-defined sequence of tasks that automates the movement and processing of inventory for optimal efficiency. Workflows are the heartbeat of how teams must operate and interact. Every workflow should make sense independently and harmonize within the context of other workflows that may overlap. It’s a complex choreography where a WMS must be capable of defining workflows that adapt to operational requirements.
Many WMS solutions struggle to keep pace with the complexity of modern warehouse operations. Most legacy systems have workflows hardcoded into their codebase, offering users limited or no options for adjustment. The challenges of hardcoded workflows include an inability to adapt to new business requirements, seasonal fluctuations, or unexpected events. This rigidity may result in missed opportunities for optimization and improvements that rely on workflow adjustments. Any changes to workflows require IT involvement, leading to potential delays, backlogs, and increased costs. WMS users may have limited autonomy, and hardcoded workflows may not efficiently scale or integrate with other systems, hindering growth and restricting data exchange and automation opportunities. Additionally, identifying and fixing bugs in hardcoded workflows can be complex, requiring specialized expertise.
For businesses aiming for a more flexible and adaptive operational setup, the solution lies in seeking a WMS that offers a rich palette of workflow options. It’s not just about having predefined workflows; it’s about the ability to change, add, or enhance these workflows to cater to specific needs, strategies, and market dynamics. A WMS should be as easy to configure and change as it is to test, deploy, train personnel, and adjust to different physical layouts, and product requirements.
Made4net offers a WMS solution that empowers businesses to transform their internal culture from a “system-limited mentality” to an “ever-changing mentality” fueled by the flexibility and capabilities of the platform.
CONCLUSION
Where adaptability is key, three key functionalities emerge as the hallmarks of a must-have WMS: prioritization, attributes, and workflows — PAW. These pillars enable a strategic mindset that facilitates agility and responsiveness in an ever-changing business landscape. By mastering PAW, businesses can not only navigate an ever-changing market but also thrive within it.
Prioritization ensures agility by assigning orders their rightful urgency, while flexible attributes empower data-driven decision-making tailored to specific needs. Customizable workflows, free from the burden of hardcoding, unlock a realm of optimization and growth. The future of warehousing lies in systems like Made4net, where adaptability isn’t just a feature, it’s the driving force.
By embracing these WMS must-haves, businesses can shed the limitations of yesterday and confidently step into a tomorrow brimming with opportunity. Flexibility is the key to success, and a well-equipped WMS is the perfect partner.
We know that you’re looking for ways to not only keep up with the ever-changing supply chain, but to be on the forefront of all it brings. We invite you to have a conversation with one of our supply chain experts to talk through your specific challenges and discover how Made4net can help you address those and more. We look forward to working with you.