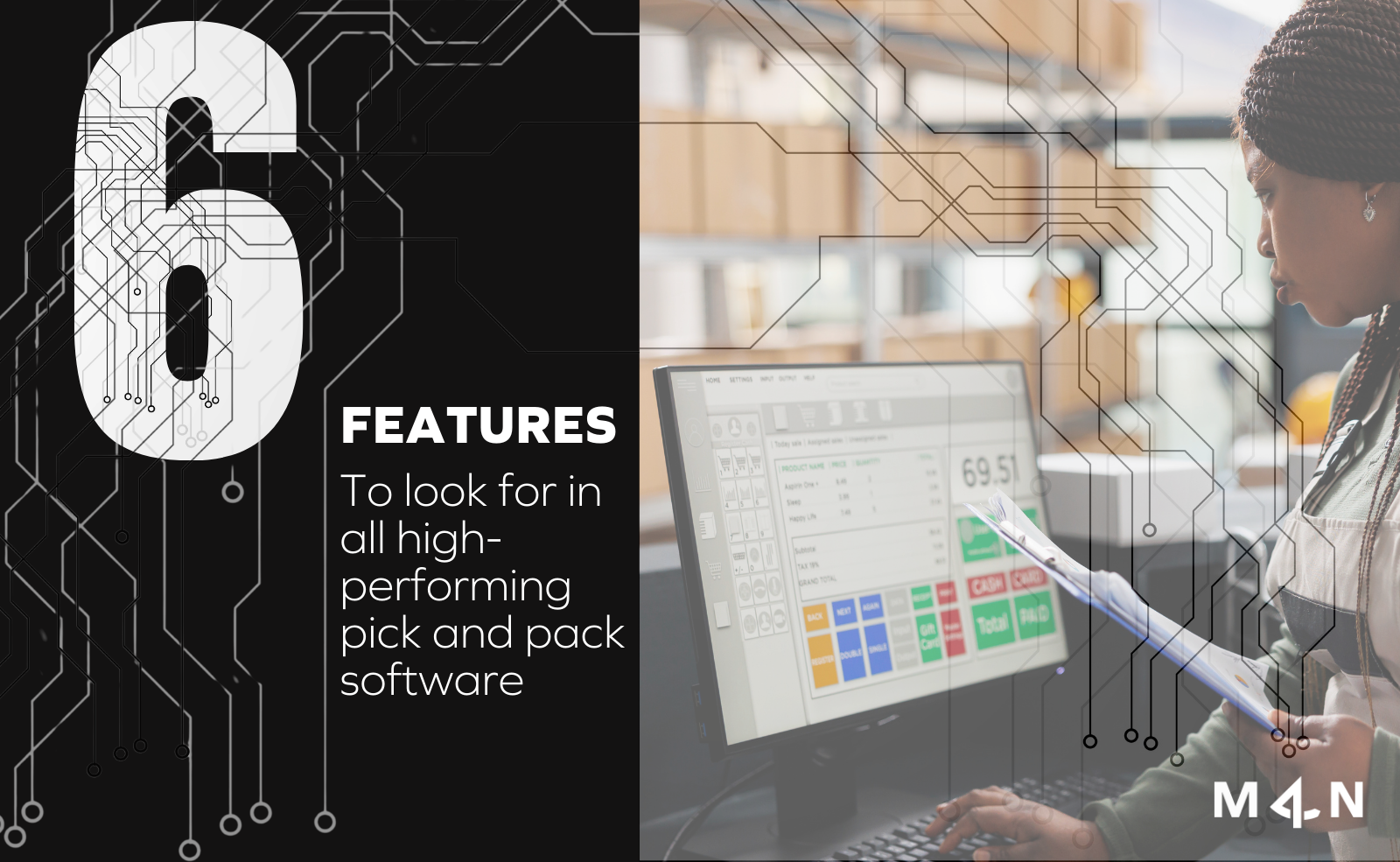
A cloud-based warehouse management system (WMS) and Pick and Pack Software are both vital tools for managing warehouse operations, but they serve different purposes and scopes. A WMS is a comprehensive software solution that manages all aspects of warehouse operations, including inventory management, receiving, putaway, picking, packing, shipping, labor tracking, and sometimes even yard management. Pick and Pack Software is more focused and specializes in streamlining the picking, packing, and shipping processes within the warehouse or distribution center.
In this article, we’ll cover:
- What is pick and pack software?
- Who uses pick and pack software?
- What is the pick and pack process?
- Key features to look for in a pick and pack system
- Important integrations for your pick and pack software
- Benefits of Effective Pick and Pack Software for High-Volume Warehouses
- The Best Pick and Pack Software for Your Business
What is Pick and Pack Software?
Pick and Pack Software is a specialized tool designed to streamline the order fulfillment process in warehouses, distribution centers, and eCommerce operations. Key functions include guiding workers through efficient picking paths, suggesting optimal packing methods and materials and integrating with shipping carriers for label generation and tracking. By optimizing workflows, reducing errors, and improving overall productivity, this software ensures the efficient picking, packing, and shipping of customer orders.
Who Uses Pick and Pack Software?
- eCommerce Retailers: To handle high volumes of online orders efficiently.
- 3PLs (Third-Party Logistics): To serve multiple clients with varied fulfillment needs.
- Wholesalers and Distributors: To manage bulk orders across multiple locations.
- Direct-to-Consumer Brands: To streamline in-house fulfillment operations.
What is the Pick and Pack Process?
The pick and pack process involves selecting items from inventory (picking) and preparing them for shipment (packing). Here’s how it typically unfolds:
- Order Receipt: Orders are received from sales channels and entered into the system.
- Picking: Warehouse staff locate and retrieve the items from inventory, guided by software that suggests the most efficient route.
- Packing: Retrieved items are packed securely using recommended materials and box sizes.
- Shipping: Packages are labeled and shipped via integrated carrier services, with tracking updates sent to the customer.
This process, when managed with software, is significantly faster and more accurate than manual methods.
Key Features to Look for in a Pick and Pack System
Pick and Pack Software Feature #1: Order Management Integration
- Integrates with sales channels (eCommerce platforms, ERP systems) to receive and process orders.
- Prioritizes and groups orders based on urgency, location, or shipping method.
Pick and Pack Software Feature #2: Picking Optimization
- Guides workers through the most efficient path to pick items in the warehouse.
- Supports picking methods such as batch picking, zone picking, or wave picking.
- Reduces errors by verifying product details (e.g., barcodes or RFID tags).
Pick and Pack Software Feature #3: Packing Assistance
- Suggests the right packing materials and box sizes for orders.
- Ensures items are packed securely, with weight and dimensions recorded for shipping.
- Prints shipping labels directly.
Pick and Pack Software Feature #4: Integration with Shipping
- Connects to carriers (FedEx, UPS, USPS) for real-time rate comparisons and tracking.
- Automates shipping label generation and updates customers with tracking information.
Pick and Pack Software Feature #5: Inventory Tracking
- Updates inventory levels in real-time as items are picked and packed.
- Prevents overselling by syncing with stock across multiple sales channels.
Pick and Pack Software Feature #6: Analytics and Reporting
- Provides data on order accuracy, fulfillment speed, and employee productivity.
- Helps identify bottlenecks and areas for improvement.
Important Integrations for Your Pick and Pack Software
By integrating with other tools, pick and pack software ensures seamless and efficient order fulfillment. Here are some key integrations to consider:
- Sales Platforms: Sync orders from Shopify, Amazon, or other platforms directly into the system.
- Shipping Carriers: Access real-time shipping rates and automated label printing.
- Accounting Software: Simplify invoicing and financial tracking.
- Customer Relationship Management (CRM): Enhance customer service by keeping order details at your team’s fingertips.
Benefits of Effective Pick and Pack Software for High-Volume Warehouses
Improved Accuracy: Minimizes picking and packing errors, leading to fewer customer complaints and returns.
Faster Order Fulfillment: Optimizes workflows to ensure orders are picked, packed, and shipped quickly, improving customer satisfaction.
Cost Savings: Reduces labor costs by increasing efficiency and avoiding overuse of packing materials.
Scalability: Supports growing operations by handling increased order volumes seamlessly.
Enhanced Customer Experience: Accurate and timely order fulfillment boosts brand loyalty and customer retention.
The Best Pick and Pack Software for Your Business
Selecting the right pick and pack software depends on your business needs, order volume, and existing tech stack. Look for a solution that integrates with your current systems, supports your preferred picking methods, and offers robust analytics to drive continuous improvement. Investing in the right software can transform your operations, positioning your business for long-term success. Need help? Reach out to one of our supply chain experts to learn if a WMS or pick and pack solution is right for your business.