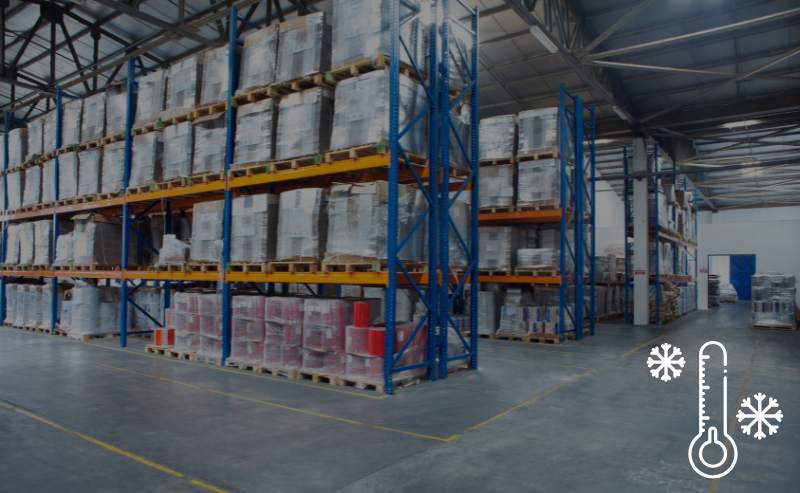
Cold storage is essential for preserving the quality, safety, and shelf life of temperature-sensitive products like food, pharmaceuticals, and certain chemicals. As consumer demand for fresh and perishable goods rises, and regulatory standards grow stricter, cold storage, supported by a cold storage Warehouse Management System (WMS) or a food and beverage WMS, has become a critical component of the modern supply chain.
In this post, we’ll explore why cold storage matters, the challenges it presents, and how to ensure your cold chain operations stay efficient, compliant, and reliable.
- The Unique Demands of Cold Storage
- Key Features Your Cold Storage WMS Should Have
- Key Considerations for: Slotting and Order Picking Optimization in Cold Environments
- Key Considerations for: Automation & Real-Time Monitoring in Cold Storage Optimization
- What You Need to Know About Compliance and Traceability in Cold Storage Management
- Best Practices for Cold Storage WMS Implementation
- Getting Started with a Cold Storage Warehouse Management System
The Unique Demands of Cold Storage
Cold storage comes with several unique demands that set it apart from standard warehousing. Some of the most critical requirements include:
- Precise Temperature Control
Different products require specific temperature ranges—frozen foods, fresh produce, pharmaceuticals, and biologics all have different needs. Maintaining these strict conditions is non-negotiable to ensure product safety and compliance. - Regulatory Compliance
Cold storage facilities must meet stringent industry regulations such as FDA, USDA, and GMP standards, especially when storing food or pharmaceuticals. This includes detailed documentation and traceability. - Energy Efficiency and Sustainability
Cold storage facilities consume significantly more energy than ambient warehouses. Operators must find ways to optimize energy use—like insulated doors, energy-efficient refrigeration systems, or solar integration—to control costs and meet sustainability goals. - Shorter Handling Windows
Temperature-sensitive products often have shorter shelf lives and must move quickly through the supply chain. This puts extra pressure on picking, packing, and shipping processes to be fast and accurate. - Specialized Equipment and Infrastructure
Cold environments require durable, insulated materials, moisture-resistant equipment, and specialized forklifts and automation designed to operate in freezing conditions. - Workforce Challenges
Labor in cold environments is difficult to sustain. Workers need special gear, shift limits, and frequent breaks, which adds complexity to labor planning and productivity. - Zoning and Temperature Mapping
Many cold storage facilities must manage multiple temperature zones (e.g., chilled, frozen, deep freeze) under one roof. This demands careful layout planning and sophisticated monitoring systems. - Cold Chain Continuity
The integrity of the cold chain must be maintained during transfers between storage, transportation, and end-users. Any break can lead to spoilage, lost inventory, and regulatory penalties.
These demands require careful planning, investment in the right infrastructure and technology, and experienced operational management to ensure reliability and efficiency.
Key Features Your Cold Storage WMS Should Have
A cold storage warehouse management system (WMS) must go beyond standard capabilities to meet the unique demands of temperature-sensitive operations. One of the most critical features is real-time temperature and humidity monitoring, which ensures environmental conditions remain within safe thresholds and triggers alerts when deviations occur. Equally important is advanced inventory control and expiration management—using lot tracking, batch control, and FIFO or FEFO strategies to reduce waste and maintain compliance for products like food and pharmaceuticals. Regulatory compliance and audit readiness are also essential; a robust cold storage WMS automates documentation, maintains audit trails, and generates reports to meet FDA, USDA, and FSMA standards with minimal manual effort.
To support operational efficiency, the WMS should offer optimized order fulfillment and picking capabilities, minimizing the time products spend outside controlled environments and improving labor productivity through strategies like wave or zone picking. Cold chain visibility is another key feature, with integration to transportation management systems (TMS) and real-time tracking tools that ensure product integrity from warehouse to delivery. Finally, seamless integration with ERP systems, IoT sensors, and compliance platforms enables end-to-end visibility and smarter decision-making. Together, these features empower cold storage operations to reduce risk, enhance efficiency, and deliver consistently high-quality service across the supply chain.
Key Considerations For Slotting and Order Picking Optimization in Cold Environments
- Organize inventory by temperature zones for speed and safety.
- Store fast-moving items near access points to reduce travel time.
- Group items with similar temperature needs together to minimize temperature changes.
- Use wave and batch picking to boost efficiency.
- Redesign layouts to shorten pick paths and reduce worker exposure.
- Equip pickers with voice tech and wearable devices so they can work safely with gloves on.
- Supplement human efforts with automation for faster, safer picking.
Key Considerations For Automation & Real-Time Monitoring in Cold Storage Optimization
- Use AS/RS and robotic systems built for sub-zero conditions to limit human time in freezing areas.
- Install insulated conveyor belts designed to withstand extreme cold and prevent brittleness.
- Implement sensors for real-time temperature alerts to quickly detect issues.
- Automate inventory updates to keep stock accurate without manual checks.
- Maintain detailed temperature logs for compliance and audit readiness.
- Combine these technologies to reduce staff turnover and meet customer service goals reliably.
What You Need to Know About Compliance and Traceability in Cold Storage Management
In cold storage management, compliance and traceability aren’t optional—they are foundational to protecting product integrity, meeting regulatory standards, and ensuring smooth, transparent operations across the supply chain. From the moment a product enters your facility to the time it reaches the customer, you must be able to track, document, and prove every step it takes.
Compliance involves adhering to strict guidelines from regulatory agencies such as the FDA, USDA, and FSMA, particularly when handling temperature-sensitive goods like pharmaceuticals, fresh produce, and frozen items. A modern cold storage WMS plays a key role in meeting these standards by automating digital documentation—capturing and storing critical data like receiving logs, inventory levels, and shipping records. This not only reduces the risk of human error but also allows for quick data retrieval during audits, ensuring companies stay audit-ready at all times.
Traceability ensures that every item in your facility can be tracked by lot, batch, or serial number through its entire lifecycle. If there’s a recall or quality issue, your team must be able to instantly identify where affected inventory is stored, where it’s been, and where it’s going. A WMS enhances this process by managing detailed product histories, expiration dates, and stock rotation strategies like FIFO or FEFO.
Integrated IoT sensors take compliance to another level by monitoring temperature and humidity conditions in real time. When deviations occur—such as a temperature excursion—the system issues immediate alerts, allowing staff to take corrective action before product quality is compromised. The WMS can also notify users of upcoming product expirations, helping prevent the distribution of spoiled or ineffective goods.
In short, compliance and traceability in cold storage aren’t just about checking boxes—they’re about enabling trust, reducing risk, and keeping the entire cold chain running smoothly. With the right WMS in place, cold storage providers can ensure they meet regulatory requirements while improving visibility, accountability, and responsiveness throughout the supply chain.
Best Practices for Cold Storage WMS Implementation
While implementing a WMS in cold storage facilities comes with its share of challenges, there are tried and true strategies that will ensure optimal performance.
- Involve stakeholders early: Engaging all relevant stakeholders from the outset fosters collaboration and ensures that the system meets the specific needs of each department. It also facilitates better planning, resource allocation, and buy-in, which are critical for successful implementation.
- Choose WMS vendors experienced in cold storage: Selecting a vendor with a proven track record in cold storage solutions is vital. They understand the intricacies of temperature-controlled environments and can offer tailored features like multi-temperature zone management and compliance with food safety regulations.
- Pilot in one zone before scaling: Conducting a pilot implementation in a single zone allows you to identify and resolve potential issues before a full-scale rollout. This approach minimizes disruptions and provides valuable insights that can inform broader deployment strategies.
- Prioritize training and ongoing support: Comprehensive training ensures that staff are comfortable and proficient in using the new system, which is essential for maximizing its benefits. Ongoing support and refresher training sessions help maintain high performance levels and adapt to any system updates or changes in operational procedures. It has the added bonus of communicating to your employees that you value their time and are invested in their success.
Getting Started with a Cold Storage Warehouse Management System
Implementing a WMS with these considerations in mind can significantly enhance compliance, efficiency, and overall operational effectiveness in cold storage environments. The right cold storage warehouse management system is your ticket to customer satisfaction, cost savings, and seamless compliance. If you’re ready to take your cold storage and distribution efforts to the next level, you’ve come to the right place. Learn how Made4net’s Food and Beverage WMS can help you achieve greater accuracy, efficiency, and control.