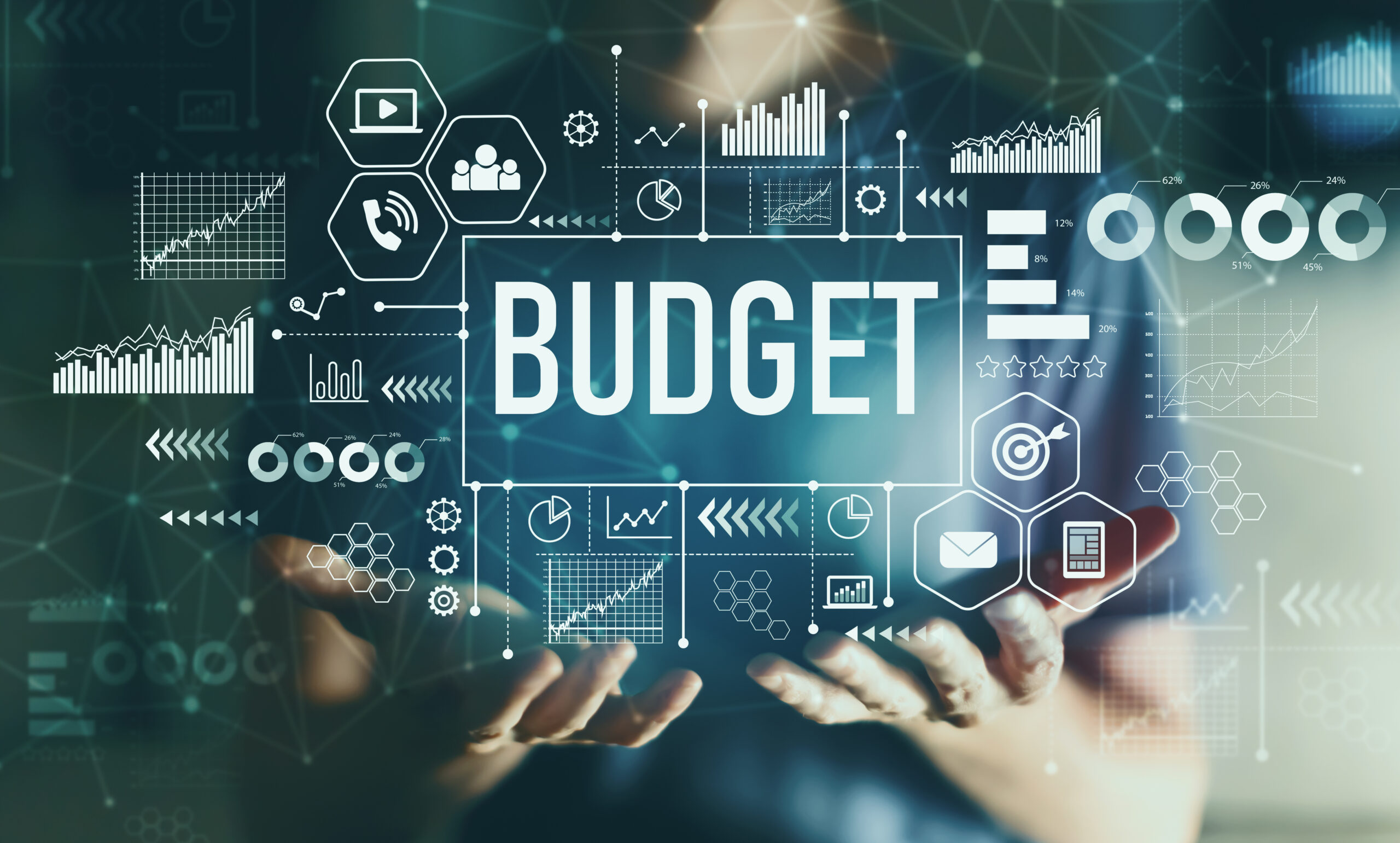
If you’re in the market for a new Warehouse Management System (WMS), one of your main concerns is likely, “How much does WMS software cost?” Many factors go into system pricing which can make it difficult to pinpoint the exact price of the best WMS for you.
To help you create an accurate budget for a new WMS, this post will guide you through all the essential considerations and variables:
- Understand the variables that affect WMS software cost
- Compare on-premise and cloud-based WMS solutions
- What WMS upgrades should you expect or evaluate?
- What are the implementation fees, and how long does it take to set up a WMS?
- Hidden WMS costs to consider
- WMS software cost: consider ROI and long-term savings
Understand the variables that affect WMS software cost
Before you can determine the best WMS solution for you, it’s critical to have a good understanding of your warehouse’s complexity and the importance of a warehouse management system. Highly complex facilities require more WMS functional breadth and depth to support their needs, while simpler operations often require less. There are three tiers of WMS solutions architected to meet the needs of these environments.
WMS providers summarize the three tiers of WMS solutions as follows:
Tier 1 WMS: Advanced needs, high volume capabilities and automation interfaces
Tier 1 warehouse management systems are the most comprehensive, and include all the capabilities of tier 2 and tier 3 WMS, plus more advanced business rules for real time picking, putaway, task interleaving, labor management and prioritization. Tier 1 solutions also support higher levels of complexity in warehouse automation, such as heavily automated facilities with AS/RS, Goods to Person, Voice, sortation, robotics and other MHE equipment. Tier one solutions are also recognized for their ability to support very high volumes and for scalability to grow as distribution needs change and networks grow.
- PERKS
- Most robust
- Offers multiple functionalities, like task management, task interleaving, voice activation, RFID, wireless communication, and automation support.
- Can be highly customized
- Offers connectivity that supports complex fulfillment network operations
- Excellent for large-scale operations
- Support steady growth and flexibility
- DRAWBACKS
- Higher upfront cost
- Take the longest to implement
- More extensive implementation process
- Support and maintenance costs can be higher
Tier 2 WMS: Intermediate level solution with comprehensive functionality
Tier 2 warehouse management systems provide all the capabilities of tier 3 WMS plus advanced business rules for more complex distribution environments, and can support multiple warehouses, multiple clients (3PL), and can include automation integration. Tier 2 WMS typically offer more flexibility in managing inventory attributes, and can run internal processes, such as kitting, replenishments and different methods of counting processes.
- PERKS
- Robust inventory management and fulfillment capabilities, with advanced business rules for more sophisticated processes and inventory attributes
- Can include automation system integrations with warehouse control systems (WCS) retrieval systems (ASRS), conveyors, replenishment systems, autonomous mobile robots (AMRs), etc.)
- Can manage multiple warehouses, multiple divisions, multiple clients (3PL)
- Supports more complex internal processes, such as kitting, replenishments and different methods of counting
- Implementation timeframes may be faster than tier 1, depending on the vendor
- Can be scalable and adaptable to evolve as distribution needs change or grow
- DRAWBACKS
- Cost more than a Tier 3 WMS system
- While these systems support integrations with other systems, automation and MHE, heavily automated facilities with very high volumes may need a tier 1 WMS
- Levels of scalability and adaptability will vary by vendor
Tier 3 WMS: Basic level solution for simple inventory control needs.
Tier 3 warehouse management systems provide very basic inventory management. Sometimes called locator systems, they will provide basic receiving, picking, packing and shipping. These solutions are a good fit for a single warehouse with very basic operations who have limited budgets and no plans for growth or expansion, nor needs for more complex features, like replenishment, VAS, billing and system or MHE integrations.
- PERKS
- Least expensive
- Basic inventory management
- Can move inventory from receiving through putaway, storage, picking, packing, and shipping
- Fastest, easiest, and least expensive to install
- DRAWBACKS
- Cannot usually support multi-warehouse networks
- May not support integrations with other systems, automation or MHE equipment, including RF
- Does not have sophisticated rules for picking, putaway, replenishment and fulfillment capabilities
- Limited flexibility, which means warehouse processes need to change to match what the WMS can provide
- Limited scalability
The WMS tier chosen will have a significant impact on your cost. The tier chosen should take future growth plans into consideration, along with business size and complexity. The last thing you want to do is undergo an expensive implementation process only to have to do it again a few years down the line.
The number of facilities you have will also have an impact on WMS software cost. A system for a single site will cost far less than a system being deployed across multiple DCs. However, if all facilities use similar processes, then costs will be less than implementing across locations with varied processes.
Compare on-premise and cloud-based WMS solutions
There are two standard WMS models: on-premise and cloud-based WMS solutions (also known as SaaS WMS solutions), both offer varying perks and potential drawbacks. The right model will largely depend on the specifics of your operation.
Cloud-based WMS solution – Subscription | On-premise WMS solution – Licensing |
|
|
Cost | Cost |
Most cloud-based solutions are subscription-based; with ongoing monthly payments for as long as the system is in use. This can be a good option for smaller operations, or those experiencing fast growth.
While the upfront cost is lower, they can add up. Sooner or later, usually around seven years in, the amount paid monthly in subscription fees will equal the cost of the initial cost of an on-premise solution and licensing. |
Most on-premise licensed solutions require a more significant upfront investment, but it’s a one-time fee without ongoing subscription fees.
With a licensed on-premise model, the system is yours and can be customized and changed, as needed, throughout the years. It requires a high degree of responsibility to run the system while providing more freedom. |
The subscription cost of a cloud-based WMS solution will vary depending on the number of users on the account. Some models will include tiered pricing, such as a certain fee for the first 100 users, and then a lower fee for any additional users. Others may offer a “view-only” subscription for a lower cost. Explore WMS highlights monthly fees from as low as $22/month per user to as high as $500/month per user.
Licensing costs for an on-premise solution will vary depending on the range of functionality, or WMS tier level selected. According to Explore WMS, cost can range between $2,500 to $10,000 per facility for limited automation and inventory support to $20,000 to $200,000 per facility for solutions offering the latest automation, robust integrations, advanced analytics, and more.
What WMS upgrades should you expect or evaluate?
Upgrading a Warehouse Management System (WMS) can significantly enhance the warehouse efficiency and effectiveness of your warehouse operations. Some key WMS upgrades you may want to consider include:
- Enhanced Automation Features: Implement automation for repetitive tasks such as inventory counts, order picking, and sorting. This can include the use of robotics, automated guided vehicles (AGVs), and automated storage and retrieval systems (AS/RS).
- Integration Capabilities: Ensure seamless integration with other enterprise systems such as Transportation Management Systems (TMS), Enterprise Resource Planning (ERP) systems, and Customer Relationship Management (CRM) systems for streamlined operations and better data flow.
- Real-Time Data and Analytics: Enhanced real-time data analytics and reporting capabilities can help with better decision-making by providing insights into inventory levels, order status, and warehouse performance.
- Advanced Inventory Management: Implement advanced inventory management features such as RFID tracking, barcode scanning, and cycle counting to improve inventory accuracy and reduce shrinkage.
- Labor Management: Incorporate labor management features to optimize workforce productivity. This includes tools for tracking employee performance, scheduling, and task assignment.
The cost of modifying a Warehouse Management System (WMS) can vary widely depending on the extent and complexity of the customizations. Basic customizations, such as minor interface changes and simple report modifications can range from $2,000 – $15,000, but full-scale customizations such as the development of custom modules can cost $100,000 – $500,000 per module.
What are the implementation fees, and how long does it take to set up a WMS?
When considering the cost of WMS software, it’s important to consider implementation fees as well as the cost of integrations with other systems like TMS or ERP, essential employee training, and ongoing support and maintenance costs. These fees can be significant and should therefore be included in your budget.
- Implementation support: Getting up and running includes a host of tasks including system design and configuration, integrations with existing systems like ERP and TMS, data migration, and system testing to ensure the accuracy and reliability of the new system. On-premise systems will have higher installation costs than cloud-based WMS solutions, but budgets for:
- Initial Setup and Configuration for a first warehouse: can range from $75,000 to $300,000. Additional warehouses will cost progressively less as the customer’s team are capable of taking on many roll-out responsibilities after learning from the first deployment. Normally, with a third or fourth facility the customer team is self-sufficient.
- Integration with Existing Systems: can range from $10,000 to $80,000.
- Integration to Automation and Robotics typically ranges from $30,000 to $150,000.
- Data Migration: can cost between $10,000 and $30,000
- Training: Employee training is essential for a successful deployment. Training ensures that all users are proficient with the new system and any issues are promptly addressed. Training costs can range from $5,000 to $50,000, depending on the number of users and the depth of training required. Many companies rely on internal resources, which reduces the overall cost of training and provides a self-sustaining training practice within the organization.
- Ongoing Support/Maintenance: On-premise WMS packages usually include a separate annual maintenance cost in the contract. This is used to cover updates, upgrades, security patches, and tech support.
For SaaS subscriptions, the cost of support and maintenance is included as part of the services offering.
For On-premise, perpetual licenses, the annual maintenance cost range usually from 22% to 25% of your WMS’ license cost. These numbers can change depending on the vendor and usually increase with each new contract.
In terms of the time it takes to complete a WMS implementation, this estimate can vary a lot. According to Amit Levy, Made4net’s EVP of Sales and Strategy, “This is where configurability on a common platform provides tremendous value through a streamlined set up and implementation process and a better overall fit for the customer’s distribution processes.” Levy explains that, “Made4net’s standard implementation timeframe is 20 weeks, whereas other vendors can take nine months to a year, or longer.”
Hidden WMS Costs to Consider
Finally, there are hidden WMS software costs that aren’t always easy to determine. These will change based on the solution selected, but knowing about them will help you keep an eye out for them to avoid nasty surprises down the line. You can ask the WMS vendor you’re working with about these during the selection process, and use their answers to determine whether their solution is the best WMS for you.
- Hidden licensing fees associated with extra users, devices, or modules
- Infrastructure costs, if there is a need for new servers or networking equipment
- Costs of scaling up the system
- Upgrading software as business grows
- Continued user training and support if not included in the initial contract
- Data migration, cleanup, and arrangement (complications in this process may be costly)
- Unused or underutilized features
WMS Software Cost: Consider ROI and Long-Term Savings
Selecting the right Warehouse Management System (WMS) is a significant decision that can greatly impact your operations and bottom line. Understanding the total WMS costs, including licensing, implementation, training, and ongoing support, is crucial. The type of WMS, whether cloud-based, saas-based, or on-premise, will influence the initial investment.
To make an informed decision, evaluating the Return on Investment (ROI) is essential. The Made4net WMS ROI Calculator can assist in this process by analyzing your current operations and projecting potential savings and performance improvements with a new WMS. This tool considers all aspects of WMS software costs, from software fees to maintenance costs, helping you weigh risk versus reward effectively.