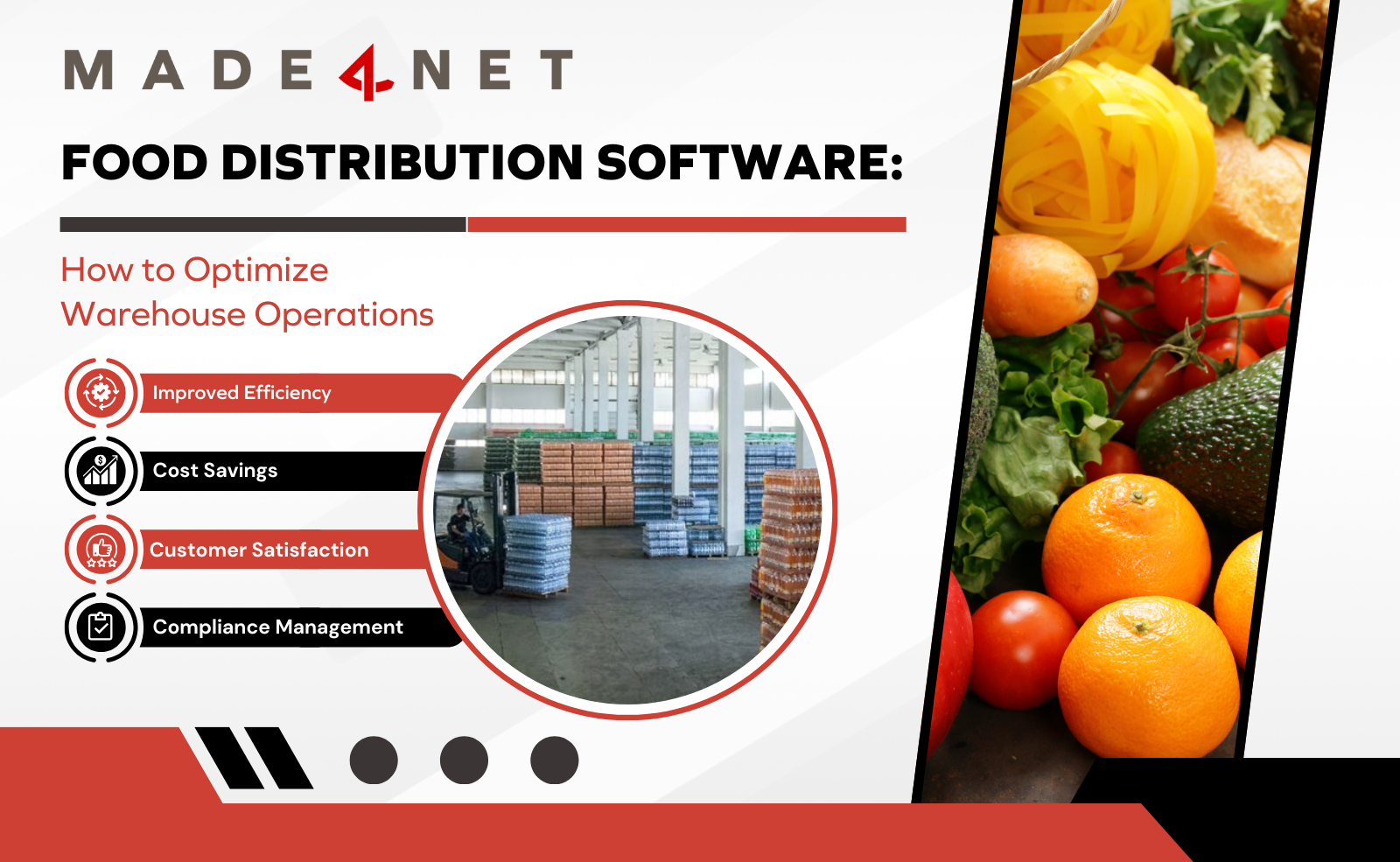
Food safety is a critical component of food distribution in the supply chain. Maintaining the safety and freshness of perishable goods takes a well-organized approach, best supported by a robust food and beverage warehouse management system. With ever-changing standards and regulations for perishable and fresh food delivery, food distributors need systems in place to track expiration dates and rotate inventory accordingly to keep up with customers’ service-level agreements (SLAs). The process is complicated, but the right food distribution software can make all the difference.
In this article, we’ll cover:
- What is food distribution software?
- Why is it important for companies and wholesalers to use food distribution software?
- What are the benefits of food distribution software?
- Key features of food distribution software
- ERP vs. WMS: Which Technology Do I Need For Effective Food Distribution?
- Examples of Food Distribution Software in Action
What is Food Distribution Software?
Food distribution software is a specialized type of software designed to streamline and optimize how an operation manages its distribution of food and beverage products. These solutions cater to the unique challenges faced by food distributors, such as regulatory compliance, inventory management for perishable goods, and supply chain efficiency. Made4net’s food and beverage WMS, for example, provides smart record-keeping, robust lot and expiration date tracking, and the ability to integrate with advanced sensors to ensure product freshness and compliance. Key features of food distribution software include:
- Inventory management
- Order management
- Regulatory compliance
- Traceability
- Route optimization
- Analytics and reporting
These systems empower food distributors to navigate the complexities of their industry while maintaining high standards for quality, safety, and customer service.
Why Is It Important for Companies and Wholesalers to Use Food Distribution Software?
Companies and wholesalers looking to maintain freshness and safety need food distribution software to help them face the unique challenges the industry presents. With the right software, operations can ensure products move safely, efficiently, and quickly through the supply chain. Here’s why it is critical:
- Safety and Compliance: Perishable goods come with strict standards and regulations regarding storage, transportation, and delivery. Food distribution software helps operations stay compliant with the industry’s ever-changing rules, ensuring proper temperature control, accurate tracking of expiration dates, and adherence to food safety protocols. This reduces the risk of spoilage, contamination, or regulatory violations.
- Efficiency and Profitability: Food distribution has a median profit margin of 3.9%. This means every process must be optimized to eliminate errors that could further impact the operation’s bottom line. Food distribution software streamlines warehouse operations, optimizes routes for faster delivery, and reduces waste, helping companies cut costs while boosting ROI.
- Real-Time Inventory Tracking: Effective inventory management is a non-negotiable component of food distribution to prevent overstocking, minimize waste, and ensure fresh products reach customers. Food distribution software enables businesses to track inventory levels, monitor product rotation (FIFO/FEFO), and gain real-time visibility into stock. This helps operations make better decisions regarding a product’s journey through the supply chain to ensure freshness and safety.
- Customer Satisfaction: Meeting consumer demand for fresh, high-quality products is critical. The right food distribution software ensures on-time deliveries and accurate order fulfillment while supporting omnichannel needs like direct-to-consumer or wholesale distribution.
- Adaptability: Fluctuating demand, seasonal variability, and the need for traceability are just a few of the challenges food supply chains face. Food distribution software enables companies to navigate these issues with ease, through advanced forecasting, traceability from source to shelf, and tools to adapt to disruptions quickly.
- Drive Long-Term Growth: Beyond operational efficiency, food distribution software supports scalability. As businesses grow, the software can handle increased order volumes, additional warehouses, and new regulatory requirements without missing a beat.
What Are the Benefits of Food Distribution Software?
Food and beverage companies need traceability for recalls and regulatory audits. They must be able to easily integrate with automated systems for optimized workflows and high-speed order processing and delivery. Food distribution software provides operations with that functionality through one centralized source. The main benefits of utilizing food distribution software are:
- Improved Efficiency: Automates time-consuming tasks, reducing manual errors.
- Cost Savings: Optimizes inventory and delivery processes to reduce waste and operational costs.
- Enhanced Customer Satisfaction: Ensures timely and accurate deliveries.
- Better Compliance Management: Minimizes the risk of fines or legal issues related to food safety regulations.
Key Features of Food Distribution Software
Strict control and safety requirements, limited shelf lives, and increased regulatory scrutiny mean food distribution operations are under constant inventory stress. As such, there are a handful of food distribution software features that help these businesses remain compliant while improving their efficiency in the process.
- Smart Record-Keeping: Food and beverage distribution companies can proactively protect their business with meticulous and smart record-keeping. Detailed information on all products allows operations to respond to any changes, as needed, helping them avoid spoilage, expiration, and other conditions that could ruin a product or lead to a hazardous situation.
- Advanced Sensor Support: Food distribution companies require features that track and trace products to manage expiry dates and unique requirements at every location in the operation. This includes sophisticated sensors to track temperature data for every step of the product’s journey as even a slight temperature fluctuation could have a severe impact on the product’s safety.
- Corrective and Preventive Process Tools: The FDA has a series of requirements to foster food safety. These requirements encompass hazard analysis, corrective and preventative actions, and many conditional elements that point to specific hazards around food, its processing, and storage. The right food distribution software will help operations adhere to these policies by creating custom reports the FDA can review.
- Retail Automation Tools: Specific offerings and shipments may require custom packaging or kitting that combines multiple products. The right food distribution software will provide operations with the ability to develop and track unique SKUs and product combinations without slowing down the operation.
- Dynamic Routing & Transport Management: Flexible distribution operations are critical to maintaining a business’ reputation as a reliable partner that can meet unexpected demands while continuing to fulfill standard order volumes. Dynamic routing and transport management capabilities integrated with adaptable inventory allocation rules enable real-time visibility (via Proof of Delivery software and more) into inventory and quick action to address urgent needs without compromising ongoing operations.
Food distribution operations require software that will provide them with the most effective tools and reporting capabilities to make the most of their available inventory.
ERP vs. WMS: Which Technology Do I Need For Effective Food Distribution?
Warehouse Management Systems and Enterprise Resource Planning (ERP) software serve fundamentally different purposes and are designed to achieve distinct goals.
A WMS focuses specifically on managing and optimizing the operations within a warehouse or distribution center. It handles inventory management, order fulfillment, receiving, putaway, labor management, and space utilization. | An ERP system is a broader software solution that integrates various core business processes across an organization. It provides a unified platform for finance, human resources, supply chain management, manufacturing, customer relationship management (CRM), procurement, and more. |
Food distribution software must focus on every painstaking detail of a product’s distribution, which a WMS is uniquely qualified to address. A WMS is designed to focus on detailed warehouse operations, managing real-time inventory tracking, optimizing picking and packing processes, managing complex warehouse workflows, and integrating with material handling equipment for optimal performance.
And ERP, on the other hand, is not designed for detailed work. It offers a broad range of functions and can only take on the most basic of warehouse management processes. It lacks the advanced features that make a WMS qualified to handle food distribution effectively.
Examples of Food Distribution Software in Action
Sprouts Farmers Market, Inc., a Phoenix-based grocery chain dedicated to providing fresh produce and natural and organic foods, was still using manual, paper-based processes when they hit the 40-store mark. They were looking for ways to manage their new growth, increased volume, and complex warehouse operations, and to offer a next-day delivery guarantee on all orders.
After adopting Made4net’s WMS and mobile RF scanners, they recorded a 32 percent improvement in inventory accuracy in the same six-month period over the previous year. The technology empowered them to:
- Streamline and standardize processes in distribution centers
- Assign LPN barcode labels to pallets to facilitate quality control
- Increase picking efficiency by 25 percent
- Support higher fulfillment volumes
- Increase productivity gains using existing labor forces
- Improve order accuracy
With shorter fulfillment cycles, automated quality control, and the ability to control the flow and traceability of perishable inventory, Sprouts has now grown to three distribution centers servicing more than 400 retail locations nationwide. Food distribution software can be how an operation stands out from its competition to achieve new heights.
Ready to learn more? Contact Made4net for a free demo using food and beverage data.