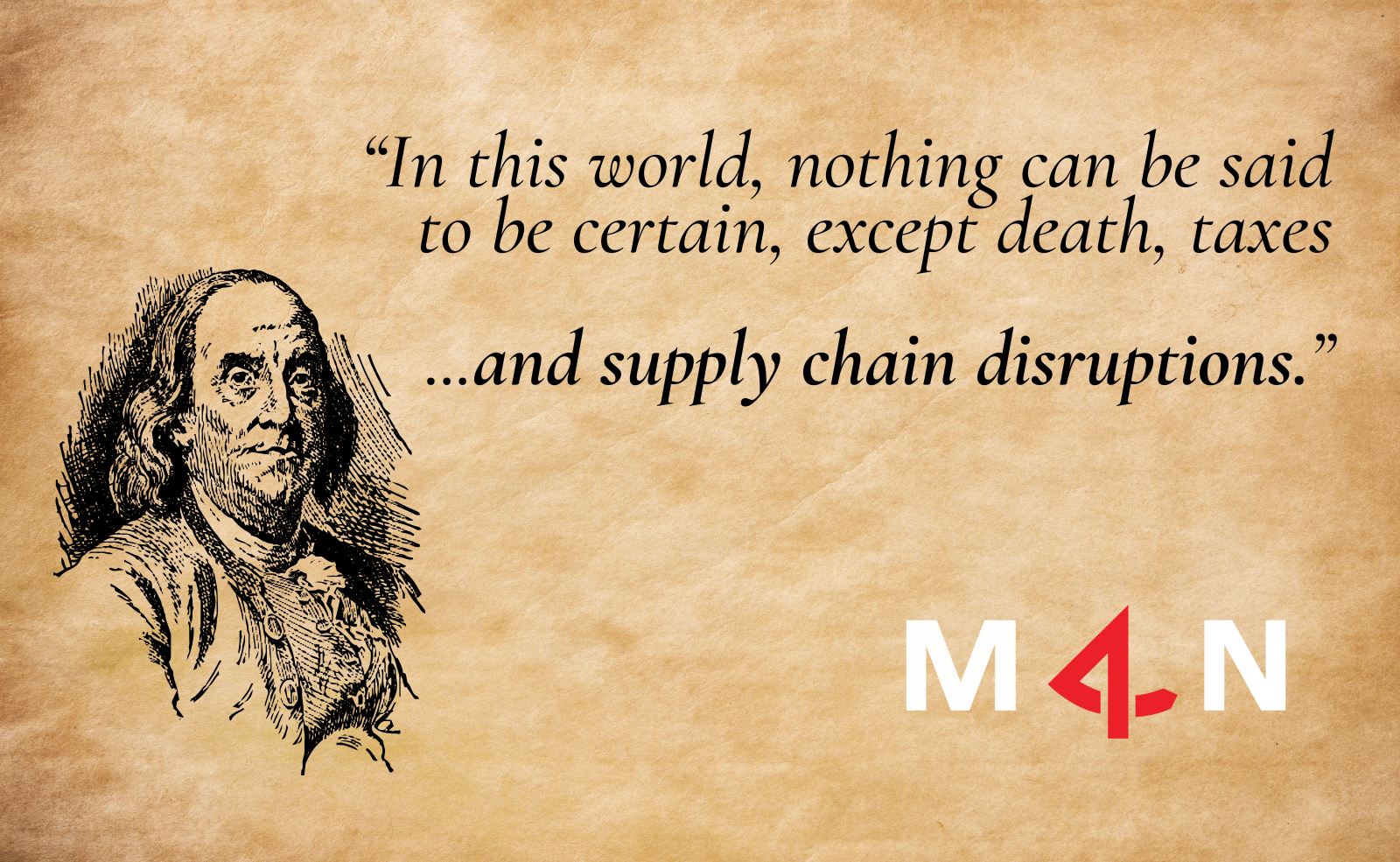
Supply chains worldwide have come to terms with the fact that they are in the business of volatility, unpredictability, and tension. Ensuring goods and services move across the market seamlessly, in light of everything else that is going on in the world is nothing short of a miracle. Yet, time and again, it gets done. As we enter 2025, we’re exploring the top five trends and concerns supply chain executives have for the year. If you’ve been paying attention over the last five years, none of this will come as a surprise—though you might still be struck by various nuances.
Supply Chain Disruptions
Benjamin Franklin’s famous words, “In this world, nothing can be said to be certain, except death and taxes,” were insightful—but not entirely complete. If he had foreseen the complexities of 21st-century global supply chains, he might have revised his statement to include: “In this world, nothing can be said to be certain, except death, taxes, and supply chain disruptions.”
These disruptions are largely unavoidable, and when they arise, there is nothing we can do but face them. Climate plays a massive role in these supply chain disruptions. According to The Economist, “Today, a billion-dollar extreme weather event occurs every three weeks. Four decades ago, one occurred every four months.” Flooding, for example, has been so unpredictable it has surprised nations with cutting-edge weather warning systems, caught off guard by sudden flash floods. According to a report by Everstream Analytics, “in 2024, flooding events contributed to 70% of the weather disruptions.” These events aren’t the only ones that leave a mark:
- Extreme temperatures can lead to unplanned blackouts forcing the closure of factories, railroads, and other critical operations.
- Storms have the power to sideline ships and destroy ports, forcing the diversion of essential deliveries.
- Fires in many parts of the world, including the Western U.S. and Canada, lead to the closure of major transportation routes and the destruction of warehouses and essential goods.
And we all know that supply chain disruptions don’t end there. Geopolitical tensions, tariffs, tensions with China, and cybersecurity all play their part in destabilizing the complex logistics networks we all work so hard to maintain.
Geopolitical Instability
Political upheaval around the globe carries its own set of implications. Full-on wars and skirmishes all play a part in destabilizing political and economic relations. With ongoing tension in the Middle East and elsewhere, the impact on logistics is unavoidable.
The same report by Everstream Analytics explains, “Even if the traffic along the Suez Canal route returns to full throttle in 2025, this shift would cause weeklong processing delays, container backlogs, and a spike in congestion at many European seaports due to the sudden increase in cargo volume.” Geopolitical instability leads to a wellspring of supply chain complications:
- Shipping delays
- Increased costs, either due to higher shipping fees, tariffs, or the need to reroute a shipment at the last minute.
- Political tension can disrupt suppliers’ operations, leading to shortages and production halts, ultimately rendering those suppliers unreliable.
- Geopolitical tension may lead to increased capacity constraints, driving up costs and delaying shipments.
Political tension can have significant economic implications. The interconnected nature of our supply chains means disruptions in one area can quickly turn into one that affects another area entirely. That’s just it—politics isn’t just politics. In the supply chain world, it’s a complex web of challenges, and supply chain professionals are the ones tasked with untangling it all and finding solutions. Hand in hand with geopolitical tension are tariffs, and there are quite a few of those on the horizon.
Tariffs
Tariffs are poised to remain a critical factor shaping global supply chains, as trade tensions and protectionist policies show little sign of abating. The U.S. administration has unveiled plans for a 25% tariff on imports from Mexico and Canada, citing objectives such as addressing illegal immigration and curbing the flow of illicit drugs, such as fentanyl. There are also proposals for a 10% tariff on Chinese imports, signaling an escalation in trade tensions with one of the world’s largest economies.
Tariffs run the risk of leading to trade wars due to retaliatory measures from the affected countries. The volatile trade environment borne of that tension complicates supply chain management and effective decision-making, while simultaneously leading to more uncertainties for businesses around the world.
The increased tensions between the U.S. and its trading partners will have a significant effect on the automotive, semiconductor, and manufacturing industries, all of which are inextricably intertwined with cross-border supply chains. While tariffs are a strategic tool to protect domestic industries, they come with significant downstream effects on supply chain operations. For businesses, tariffs often translate into higher costs, as imported goods and raw materials become more expensive. These additional expenses are typically passed down the supply chain, affecting manufacturers, distributors, and ultimately consumers.
Beyond cost, supply chain managers must navigate complex compliance requirements to ensure adherence to evolving trade regulations. Tariffs also drive companies to reconsider their sourcing strategies, often leading to shifts in supplier bases or the relocation of manufacturing facilities. While nearshoring or reshoring initiatives can mitigate reliance on tariff-heavy regions, such moves are time-intensive and costly, requiring significant adjustments to logistics networks and supplier relationships.
Relationship with China
In addition to tariffs, continued tension between the U.S. and China impacts the global supply chain in myriad ways. China’s central role in manufacturing and trade and the two countries’ interdependent economies mean tension introduces volatility and uncertainty into the supply chain.
Delays and supply chain disruptions are the price to pay with increased slowdowns at customs due to stricter inspections and regulatory hurdles, causing delays at ports and extending lead times for goods. To further confound matters, companies in China may be reluctant to engage with U.S. buyers due to fears of sanctions or payment issues, further complicating procurement.
The growing tension has encouraged many U.S. companies to reduce their dependency on China by bringing manufacturing closer to home. The implication, of course, is higher costs. There’s a reason China has been the mecca for manufacturing for as long as they have — it’s cheap. Shifting to other countries also means the potential for more delays and inefficiencies as those countries don’t have the same robust infrastructure China has had decades to create and perfect.
While geopolitical tensions introduce significant challenges to the supply chain, they are not the only source of vulnerability. Increasingly, cybersecurity threats pose a growing risk, targeting the digital infrastructure that underpins global trade, thus exposing new avenues for disruption.
Cybersecurity
While the increase in the use of Artificial Intelligence (AI) has led to more accurate forecasting in the supply chain as a whole, the reliance on AI and cloud computing is opening up new avenues for bad actors to make their moves. Everstream Analytics summarizes that a “company’s cybersecurity front doors may be double-bolted, but there are more unlocked back doors than ever available to increasingly sophisticated attackers.”
The rapid proliferation of Internet of Things (IoT) connected devices and weak and outdated security protocols leave companies vulnerable to attacks via phishing, software connection links, and ransomware attacks. These attacks appear more commonly in the electronics, logistics, and consumer goods industries, targeting procurement and manufacturing operations.
These attacks can lead to system outages, compromised data, financial losses, and increased insurance costs. But that’s not all, they impact automated processes leading to equipment malfunction as well as backups and delays. A breach in one link of the supply chain (e.g., a supplier or logistics provider) can have a cascading effect, compromising the entire network, which, unfortunately, leads to brand damage. Customers will quickly move away from a company they feel is incapable of keeping their data safe, which in our increasingly online world, is a dealbreaker.
Take Control with a WMS
In the supply chain world, there is so much you can’t control, but with a Warehouse Management System (WMS) you can guarantee control over processes, labor, and inventory. A Warehouse Management System enhances operational efficiency, accuracy, and productivity. And in this world of uncertainty and fluctuating needs, it also offers supply chain executives much-needed control. A WMS provides:
- Inventory control: With accurate inventory levels and real-time updates on stock levels, locations, and movements, operations can more accurately control the movement of goods to suit their needs throughout the day.
- Automation: A WMS fosters efficiency and productivity by automating picking, packing, and shipping, allowing the warehouse to control how space and resources are utilized for faster fulfillment.
- Cost reduction: The byproduct of overall efficiency is a reduction in overall operating costs.
- Forecasting: The valuable data and analytics provided by a WMS help businesses make data-centric business decisions in areas that need improvement.
- Integrative abilities: A WMS can integrate with other business systems such as Enterprise Resource Planning (ERP) systems, Transportation Management Systems (TMS), Labor Management Systems (LMS), e-commerce platforms and Customer Relationship Management (CRM) systems, allowing operations to have improved oversight and better control over the entire operation.
The ability to streamline every aspect of an operation provides certainty and control in an industry where that is largely unattainable. While we can’t control what items will be tariffed or how geopolitical tensions will impact the movement of goods, a WMS can provide control over mission-critical tasks.
Supply chains in 2025 will continue to operate in a landscape defined by volatility, uncertainty, and complexity. The supply chain industry possesses a remarkable ability to adapt, innovate, and overcome obstacles, and with the right technology, it can go even further. While supply chain disruptions can’t always be controlled, using a WMS to streamline operations, optimize resources, and enhance decision-making ensures that businesses remain resilient and competitive in an ever-changing world. If you need help navigating uncertainty and building resilience In the supply chain, we’re here to help.