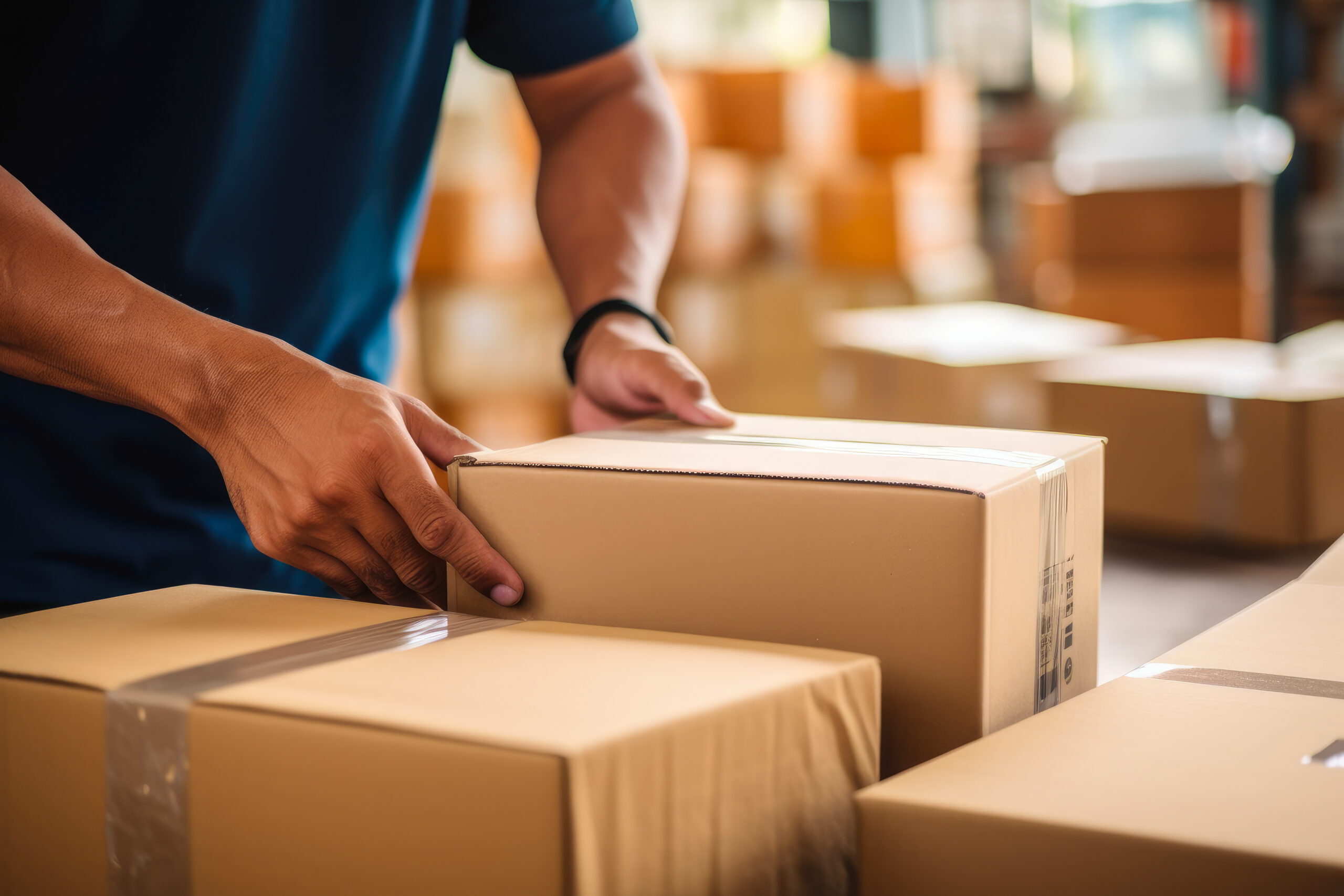
A Warehouse Management System (WMS) is the core of your warehouse operations, serving as the central hub that orchestrates all activities within the facility. However, it’s crucial to understand that a WMS does not operate in isolation. To fully unlock its potential and ensure the success of your warehouse operations—especially in the fast-paced world of e-commerce—WMS integration is key. The best WMS seamlessly integrates with other critical business systems, such as:
- Enterprise Resource Planning (ERP) Systems
- Various Sales Channels also known as e-Commerce or Digital Commerce Solutions
- Order Management Systems (OMS)
- Warehouse Hardware and Automation Solutions
- Electronic Data Interchange (EDI) Systems
- Shipping Carriers
- Transportation Management Systems (TMS)
- Customer Relationship Management (CRM) Systems
- Time & Attendance Systems (T&A)
Understanding WMS integration and the value it delivers is essential in guiding the WMS selection and WMS implementation process.
WMS Integration #1: ERP Systems
An ERP system provides a centralized platform that collects, stores, and manages data from various business functions, including finance, human resources, supply chain, manufacturing, procurement, and more. This integration allows for better coordination, improved accuracy of information, and streamlined operations across the entire organization. Traditionally, an ERP and a WMS will share the following data:
- Inventory Data: Stock levels, locations, movements, and adjustments.
- Order Information: Sales orders, purchase orders, order status, and shipping details.
- Financial Data: Cost of goods sold, inventory valuation, and financial reporting metrics.
- Supplier and Customer Data: Information related to procurement, shipping, and customer orders.
- Operational Metrics: Warehouse performance metrics such as order accuracy, picking rates, and warehouse capacity utilization.
Real-time data sharing between an ERP and a WMS empowers operations to achieve accurate financial reporting, efficient order fulfillment, optimized inventory management, improved forecasting, and streamlined procurement processes.
WMS Integration #2: Sales Channels
In e-commerce, sales channels refer to the platforms and methods through which products or services are marketed and sold to customers. These include online marketplaces, like Amazon, company websites, social media platforms, shopping carts and more. Integrating these channels with a WMS optimizes the supply chain from order placement to fulfillment.
- Marketplaces: Businesses selling on multiple marketplaces benefit from a WMS as it centralizes order processing and manages inventory across all platforms, synchronizing stock levels from various channels. This includes returns and exchange management.
- Websites: The WMS uses website information to ensure all product details are accurate and up to date, such as stock levels, descriptions, and pricing. After order placement, the WMS provides the website with tracking information for the customer.
- Social Media: The WMS integrates with social media platforms to manage all orders originating from these channels. They can also track customer engagement and preferences to improve their forecasting based on social media trends.
- Shopping Carts: The WMS will automatically update inventory levels as a customer adds items to their cart, ensuring stock availability. Once the order is complete, the order is then automatically sent to the WMS for picking, packing, and shipping.
Integrating your WMS with your sales channels allows your business to offer a seamless shopping experience, improve order accuracy, and optimize inventory management, ultimately enhancing customer satisfaction and operational efficiency.
WMS Integration #3: OMS
An order management system (OMS) is a digital platform that helps businesses track and process customer orders from placement to fulfillment. It centralizes order information, inventory management, and shipping details, allowing companies to efficiently handle orders across multiple sales channels. Traditionally, an OMS and a WMS will share the following data:
- Order Details
- Inventory Levels
- Picking and Packing Information
- Shipping Information
- Returns Information
- Performance Metrics
- Capacity and Workload Information
An OMS is crucial for managing inventory and orders, and integration with your WMS enhances operational efficiency, accuracy, and customer satisfaction.
WMS Integration #4: Warehouse Hardware and Automation
There are a variety of warehouse hardware and automation solutions that supplement the overall functioning of a warehouse for superior productivity, such as:
HARDWARE | AUTOMATION |
|
|
Amit Levy, executive vice president of sales and strategy at Made4net, explains that a “WMS has always been seen as the warehouse control tower for everything that takes place within the four walls of the warehouse, the difference being that in the past, it was mostly about controlling people. Now, it’s about controlling people, hardware and automation.”
A WMS integrates with hardware like scanners, conveyors, and forklifts through real-time data exchange and automated task management. Scanners communicate directly with the WMS to capture and validate data, while conveyors and forklifts are integrated via control systems that the WMS uses to automate and optimize material handling, ensuring efficient and accurate warehouse operations.
A WMS integrates with automation like AGVs, AMRs, and Automated Picking Systems through communication protocols and real-time data exchange. The WMS sends tasks and routing instructions to these systems, coordinating their movements and operations to optimize material handling, order picking, and replenishment processes. The automation systems feed real-time status and completion data back to the WMS, allowing for seamless coordination, increased efficiency, and reduced human intervention in warehouse operations.
This integration ensures that warehouse operations are accurate, efficient, and aligned with the overall business goals.
WMS Integration #5: EDI Systems
EDI systems allow businesses to exchange documents and data in a standardized electronic format between different computer systems, replacing paper-based documents like purchase orders, invoices, and shipping notices with digital files. By using standardized formats, data can be easily interpreted between the sender and receiver regardless of software.
Integration between EDIs and WMSs allows for:
- Automated data exchange, facilitating order processing while providing real-time updates. Once an order is placed, the EDI system sends the purchase order to the WMS, which it then processes. The WMS then updates the EDI as the order progresses, providing insight into shipment tracking information, and inventory status.
- Inventory management, like Vendor Managed Inventory (VMI) and stock replenishment, is facilitated by EDI integrations. It allows suppliers to receive real-time data directly from the WMS, allowing them to replenish stock as needed.
- Advanced Shipping Notices (ASNs) where a supplier’s WMS can use the EDI to send an ASN to the receiving company’s WMS. The receiving WMS can use the provided information, like weight and delivery time frame, to prepare to receive the goods.
- Receipt confirmation, where the WMS confirms product receipt via EDI back to the supplier.
The integration ensures that the data exchanged between trading partners and the WMS is accurate and consistent. In industries with strict regulatory requirements, the EDI ensures all necessary documentation is accurate and compliant.
WMS Integration #6: Shipping Carriers
The integration between a WMS and shipping carriers streamlines the process of shipping and logistics operations. It’s how orders are processed efficiently, shipping information is accurate, and both the warehouse and customer have real-time visibility of the shipment status. The integration allows for a series of critical steps in the fulfillment process.
- Carrier selection and rate shopping
- Label generation and documentation
- Shipment tracking and notifications
- Shipping cost management
- Inventory updates
- Order management
- Returns management
Shipping carriers and WMSs may be integrated using APIs to connect directly with carrier systems. Others may use EDI integrations, to transmit shipping information between the WMS and carriers. This integration leads to improved efficiency, cost savings, enhanced customer experience, and accurate reporting.
WMS Integration #7: Transportation Management System (TMS)
A TMS helps businesses plan, execute, and optimize the physical movement of goods. With insight into day-to-day transportation operations and documentation compliance, it ensures timely delivery at the lowest possible cost. A TMS is especially important for companies with complex supply chains. The integrations of a WMS and TMS work together to provide:
- Seamless order transmission
- Coordinated picking and shipping
- Real-time tracking
- Proactive issue management
- Accurate inventory management
- Optimized load planning
- Freight cost allocation
- Comprehensive reporting
With streamlined processes between warehouses and transportation, businesses are empowered to reduce manual work and minimize errors, thus increasing throughput. This leads to enhanced customer service and cost savings.
WMS Integration #8: Customer Relationship Management (CRM) Software
A CRM is a software solution that allows businesses to manage and analyze customer data throughout their lifecycle. Its goal is to improve business relationships with customers, foster customer retention, and drive sales growth. Key functions of a CRM include customer data management, sales and pipeline management, marketing automation, customer service support, and analytics and reporting.
The integration of a WMS and CRM creates a more cohesive workflow by linking customer data with inventory and order fulfillment processes. The integration provides operations with:
- Order tracking and history
- Personalized customer experience
- Real-time inventory data
- Backorder management
- Order confirmations and updates
- Targeted marketing campaigns
- Return processing
- Customer support
- Sales forecasting and inventory planning
- Cross-functional collaboration
These features help enhance customer satisfaction, lead to increased operational efficiency, and empower operations to rely on data-driven decision-making, all of which may lead to increased sales and retention.
WMS Integration #9: Time & Attendance (T&A) Systems
A Time & Attendance (T&A) system is a software solution or tool used to track and manage the working hours of employees. It records when employees start and end their workdays, as well as any breaks or absences they take. These systems can range from simple time clocks to advanced software that integrates with other business systems, such as payroll, human resources, and in this case, a Warehouse Management System (WMS).
A Warehouse Management System (WMS) should integrate with a Time & Attendance (T&A) system for several important reasons:
- 1. Labor Cost Management
- 2. Improved Workforce Planning
- 3. Enhanced Operational Efficiency
- 4. Compliance and Payroll Accuracy
- 5. Performance Metrics and Incentive Programs
- 6. Enhanced Security and Access Control
- 7. Reduced Absenteeism and Increased Accountability
Benefits of WMS Integration
A WMS is a critical component of a larger ecosystem of business systems. Its ability to integrate seamlessly with multiple systems, including Enterprise Resource Planning (ERP) Systems, Various Sales Channels, Order Management Systems (OMS), Electronic Data Interchange (EDI) Systems, Warehouse Hardware and Automation Solutions, Shipping Carriers, Transportation Management Systems (TMS), and Customer Relationship Management (CRM) Systems is essential for optimizing warehouse performance, supporting business growth, and maintaining a competitive edge in today’s fast-paced supply chain environment. Made4net provides a full suite of supply chain execution solutions that companies of all sizes can use to improve their supply chain operations, like WarehouseExpert, a robust real-time WMS that improves productivity, service levels, and order fulfillment times while reducing overall operational costs. Learn more about WMS integration by speaking with one of our supply chain execution experts today.
Integrations are just one of the top warehouse management system features to look for in your next partner. Check out the full list here.