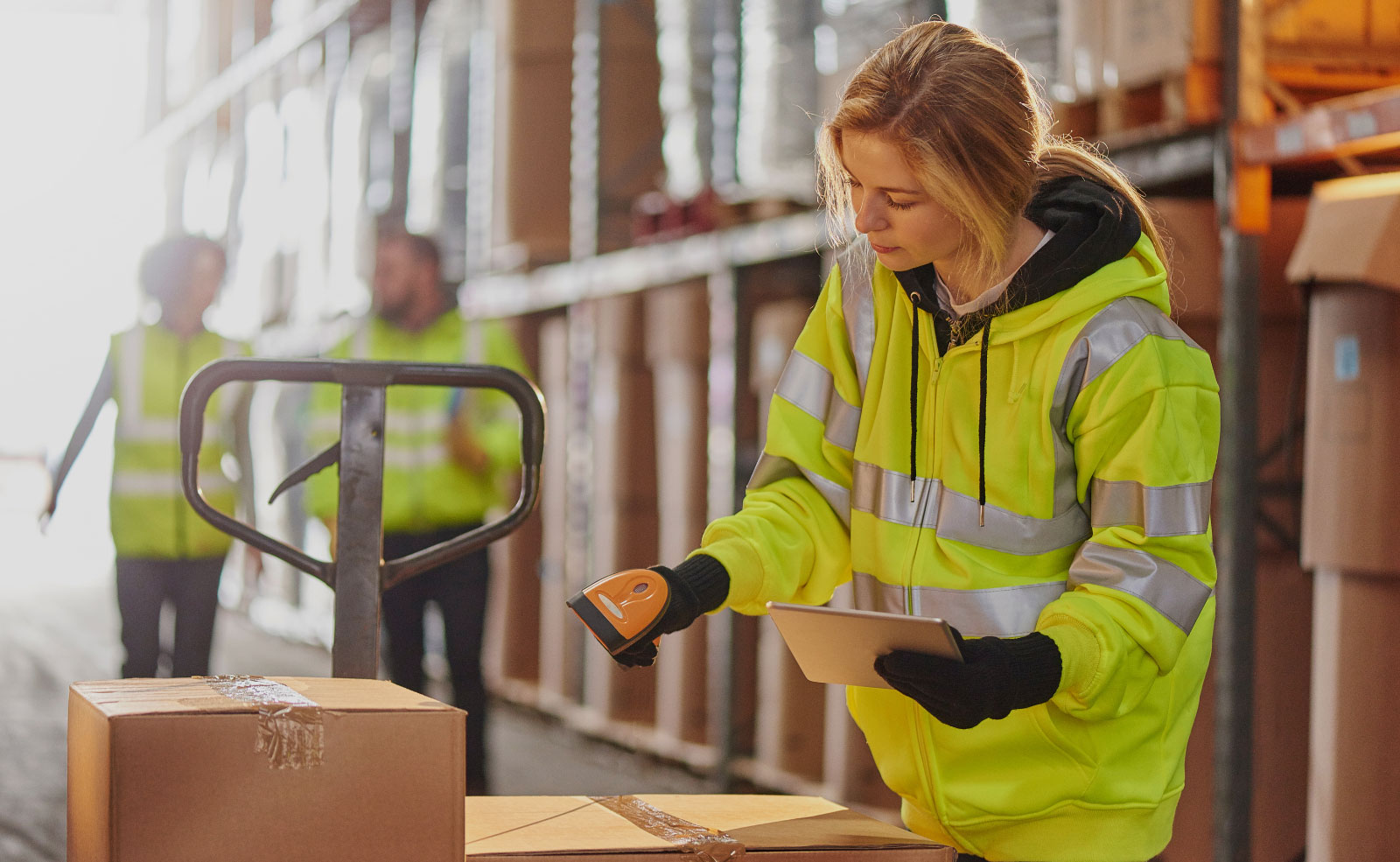
Today’s operations teams are constantly challenged to work more efficiently and productively to increase their overall profitability. To optimize their supply chain, savvy operators are conducting WMS Best Practice Assessments (BPAs) to identify areas of opportunity in their business and strategies for how to improve in these areas. The article below outlines how to conduct a BPA, and specific functions to audit for best practices and improvements, including:
- What is a WMS best practice assessment?
- How does a best practice assessment work?
- What’s the value of a best practice assessment?
- WMS best practices and key areas of focus
- Conclusion: Why the Time is Right for a WMS Best Practice Assessment
What is a WMS Best Practice Assessment?
According to Alpine Supply Chain’s Managing Principal, Michael Wohlwend, “A Best Practice Assessment (BPA) is a great exercise to help organizations uncover opportunities for improvement while benchmarking their operations against competitive, best-in-class operations. They’re a great fit for companies seeking to define WMS requirements, estimate costs and quantify ROI.”
How Does a Best Practice Assessment Work?
Most companies seeking a BPA have either never had a WMS before or have been running a legacy, home-grown solution for 10+ years. They’re looking to get a good handle on the cost and benefits of buying or replacing a WMS. As such, a BPA will vary by client and objective, but a standard engagement ensures that all business processes and areas of operation are fully reviewed and assessed. By diving deep into the details, a BPA can uncover capital and non-capital improvements across all operational areas including inventory, space, equipment, labor, and systems.
A standard engagement is a four-week process and will look as follows:
WMS BPA Week 1: Data Collection
Our data-driven methodology leverages a deep dive into metrics in every area of your operations including procurement and receiving; putaway; restocking and replenishment; order processing and selection; shipping, staging, loading, VAS; and more.
WMS BPA Week 2: Data Validation
We validate initial data findings during an onsite visit and cross reference our findings against WMS best practices from market leaders such as WERC, ROFDA, and ISO.
WMS BPA Week 3: Qualification
We share initial findings to prioritize the initiatives that streamline business processes to increase operational performance, improve customer service, and reduce cost.
WMS BPA Week 4: Final Results
We create and deliver a plan of actionable improvement recommendations and associated ROI.
What’s the Value of a Best Practice Assessment?
The value of a BPA varies by the initial objective of the exercise. Generally, a BPA enables the supply chain leadership team to confidently respond and present what a WMS would cost, how long an implementation would take, internal and external resources that are necessary for successful implementation, and when you could expect to see benefits.
WMS Best Practices and Key Areas of Focus
As operators begin their WMS Best Practice Assessment, they typically will audit four main parts of the fulfillment process: labor, automation, planning, and supply chain integration.
Labor
Labor generally accounts for 60–65% of the total operating cost of warehouse and fulfillment operations. While hourly labor rates have increased from 10% to 15% in the past five years, overall DC productivity has remained flat—so the cost per unit worked has increased. As a result, we must continue to invest in our human resources but also augment people with the right technology. Augmenting labor with technology will help you create less dependency on human resources. This could be in the area of selection, packing, storage, sortation, and so forth.
How to Measure Labor Best Practices: Overall Throughput
One KPI you can measure to track labor optimization is warehouse throughput—the number of units that are processed and moved through your facility on a daily basis. To calculate your throughput rate, track the movement of goods through the warehouse for a given period of time. For example, if you want to measure how many orders are processed by your warehouse within an eight-hour shift, you can track the number of orders received in that amount of time, and how long it takes each product to move from the picking stage to packaging and labeling.
Automation
No discussion of warehouse technology can avoid the mention of automation. Research indicates that the use of automation in warehouses is growing. In the past 10 years, we’ve seen more intelligent robots, like Autonomous Mobile Robots (AMRs) and Automated Guided Vehicles (AGVs) working together to move goods around the warehouse.
As the automation market continues to grow, so does the need for an additional layer of technology, one that coordinates all the different types of automation components that live and operate in a warehouse, known as a multi-agent orchestration platform. Experts agree this includes all types of automation, including bots and assets like elevators or conveying systems in the warehouse. It’s all about having a single platform that manages and optimizes all the components.
How to Measure Automation Best Practices: Accuracy
One KPI you can use to measure the success of automation is picking accuracy and ensuring customers get the goods they ordered within the desired time frame. Warehouse operations can target order accuracy between 99.5% to 99.9%.
Planning
It’s no secret that planning is essential in any industry, and yet we cannot emphasize this enough. Both short and long-term planning can help with improving labor efficiencies, warehouse space utilization, achieving sustainability goals, and fostering customer satisfaction. In the supply chain space, experts agreed that better connectivity between planning and execution can be achieved with dependable integration between your WMS and other order management and supply chain systems.
As you audit the success of your planning, you’ll want to review dead stock. Dead stock is inventory that is not moving due to lack of demand. It sits in the warehouse occupying space and eating up capacity. It includes stock that is damaged, expired, or unsellable for any reason. Dead stock metrics are important to monitor because dead stock creates avoidable inventory costs and blocks up space for other, more profitable goods.
Supply Chain Integration / Visibility
To succeed today, we need fully integrated supply chains with visibility into customers, vendors, and partners. We need to move past solutions that were built for linear supply chains that result in confusing segmentation. Instead, we need connected systems, like Proof of Delivery (POD) software and other technologies, that let customers know if their orders have been picked, shipped, when they will be delivered, and more. Experts were quick to add that visibility is only half the equation, workflows need to be implemented to make that visibility actionable.
How to Measure Integration Best Practices: On Time, In Full
The success of integrations and visibility should map to the overall success of a fulfillment process. Even if all the above best practices are achieved, if the goods are not delivered on time, it will negatively affect business. Typical on-time shipments should be between 98-99%. Anything over this average is considered excellent.
Conclusion: Why the Time is Right for a WMS Best Practice Assessment
Over the past few years, supply chain leaders have faced more complex, changing conditions than ever before. Enterprises of all shapes and sizes are seeking to shake up their supply chain strategies to become more resilient, collaborative, and networked with customers, suppliers, and other stakeholders. A BPA offers a great method for understanding which supply chain Best Practices will significantly improve product quality, customer service levels, market share and return on assets, and as a result, your company’s overall performance.
For more details on the best practices these experts recommend, listen to our discussion and download our white paper, Leveraging Supply Chain Execution Solutions to Navigate Ongoing Uncertainty.
Interested in learning more about how a Best Practice Assessment from Alpine Supply Chain could help you? Visit the Alpine website https://alpinesupplychain.com/warehouse-consulting/ or reach out to [email protected] to learn more.
Thank you to our partner, Alpine Supply Chain Solutions, for this guest post on a WMS Best Practice Assessment (BPA).