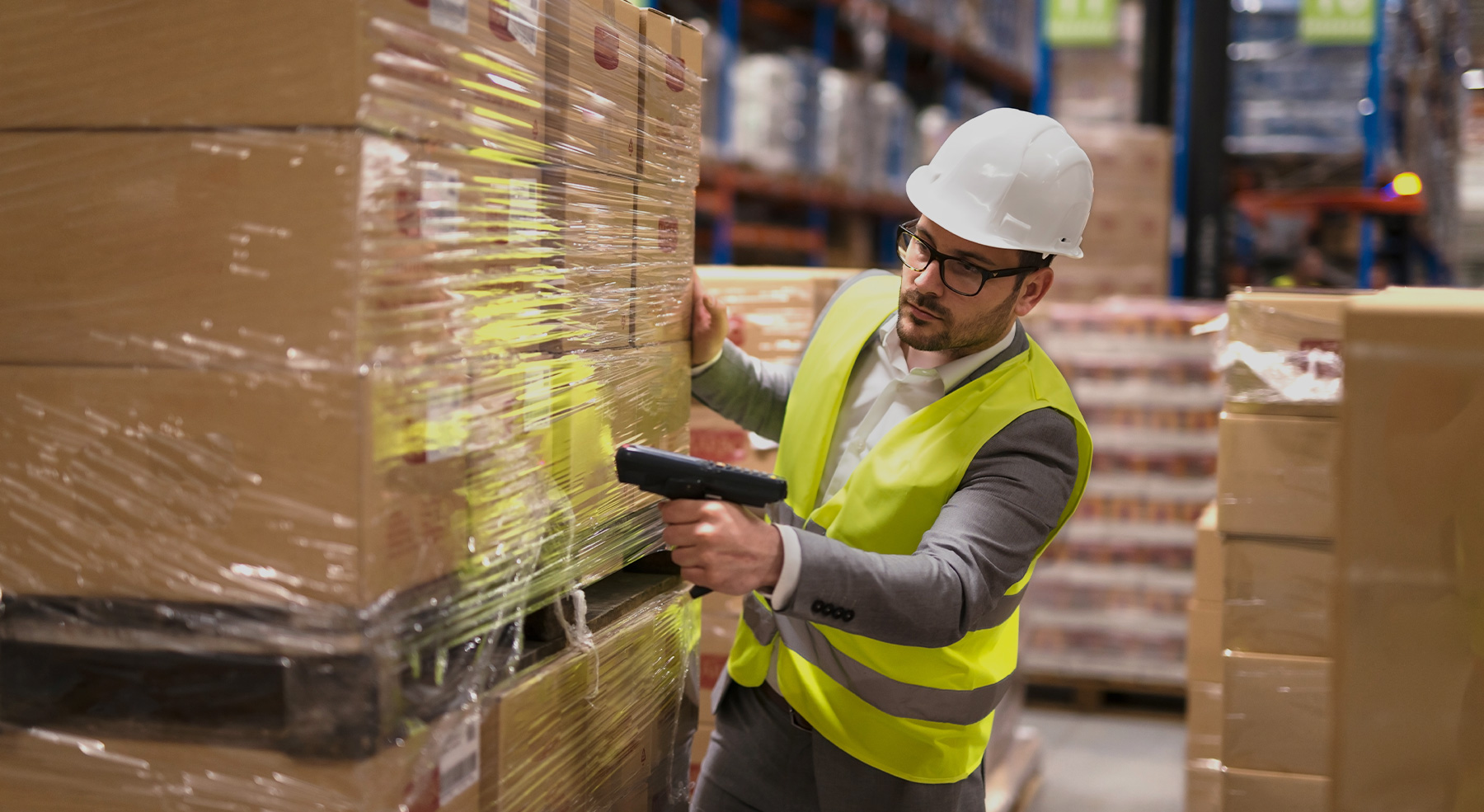
What Supply Chain Experts Have to Say About Labor
Whether you’re a supply chain expert, small business owner, or a Fortune 500 CEO, you’re keenly aware of current labor challenges. In the warehouse space, where labor costs are one of the largest expenses, labor challenges are extreme. Today it’s not only hard to hire labor, it’s hard to retain it and even harder to be sure you’re maximizing it. That’s why we recently turned to a few industry experts for their tips on how to improve productivity and labor efficiencies in the warehouse. Here’s what they had to say…
Drew Eubank, EVP & Co-Founder, Zion
According to Drew, the big trend now is investing in automation to help with labor challenges, but that can’t be done on a whim. It’s important to first determine what kind of technology is best suited for your business needs, because what works for one warehouse may not necessarily work for yours. But the one strategy that holds true for all in the supply chain space is implementing automation to assist your current workforce. Drew believes, “You have to have something to supplement that activity so that your employees are empowered to be the best employees they can be, freeing them up to be more productive and contribute more valuable work in the warehouse.”
Tyler Linderman, Director of Services and Alliances, Bricz
Tyler agrees with that sentiment, adding that assigning low-value tasks to automation will not only give employees a morale boost but will give them time and incentive to perform high-value tasks they can be proud of. In fact, he has noticed different retailers and distributors have been able to pay their employees more by replacing low-value skill workers with robots because of the quick ROI associated with automation.
But what Tyler is really excited about is the increased use of gamification within the warehouse. He thinks “finding a way to gamify the labor management space is also going a long way to incentivize employees to show up.” And why not? If a workplace can be more fun while improving efficiency, all the better! Labor challenges are ever-present, so finding creative ways to address them is one solution we can all get behind.
Mike Raboy, Client Relations Manager, Voodoo Robotics
One aspect of addressing the labor challenges lies in finding ways to keep the labor force engaged and content. As Mike shares, many labor surveys have shown that “as more automation occurs within the business, the labor force is happier. They find that they can do their work very effectively, and as a result, they want to stay with that organization when that automation is applied because it shows the organization has their needs in mind.”
Retaining labor is critical, as we all know, and hiring and re-training employees is not only a challenge on its own, but it’s expensive to boot! According to the Association for Talent Development, companies spend an average of $1,252 per employee on training and development initiatives. Thus, the reduction of turnover is an obvious step to take in managing labor costs while maintaining productivity.
Steve Simmerman, Head of Global Alliance, Locus Robotics
And while labor scarcity and rising wage rates for warehouse workers are a big reason for adopting automation, Steve is focused on advantages related to workforce safety. “We reduce work-related injuries because I’m not pulling a cart, I’m not pulling a heavy pallet jack, etc. So the soft side savings, and workforce safety, and injury reductions are a big factor, as well.”
In Summary
Clearly, we have a lot of faith in technology and what it promises to solve when it comes to labor, but we mustn’t forget the human aspect of the industry. At the end of the day, people want to be appreciated, respected, and rewarded. Without reliable strategies in place to ensure employees feel valued, no technology will be able to fill the gap to avoid turnover. If you’re looking to find the right technology for your operational needs, get in touch, we can help. And if you’re hoping for more expert advice on current and future supply chain issues, check out our Ask the Expert Series recorded at ProMat.