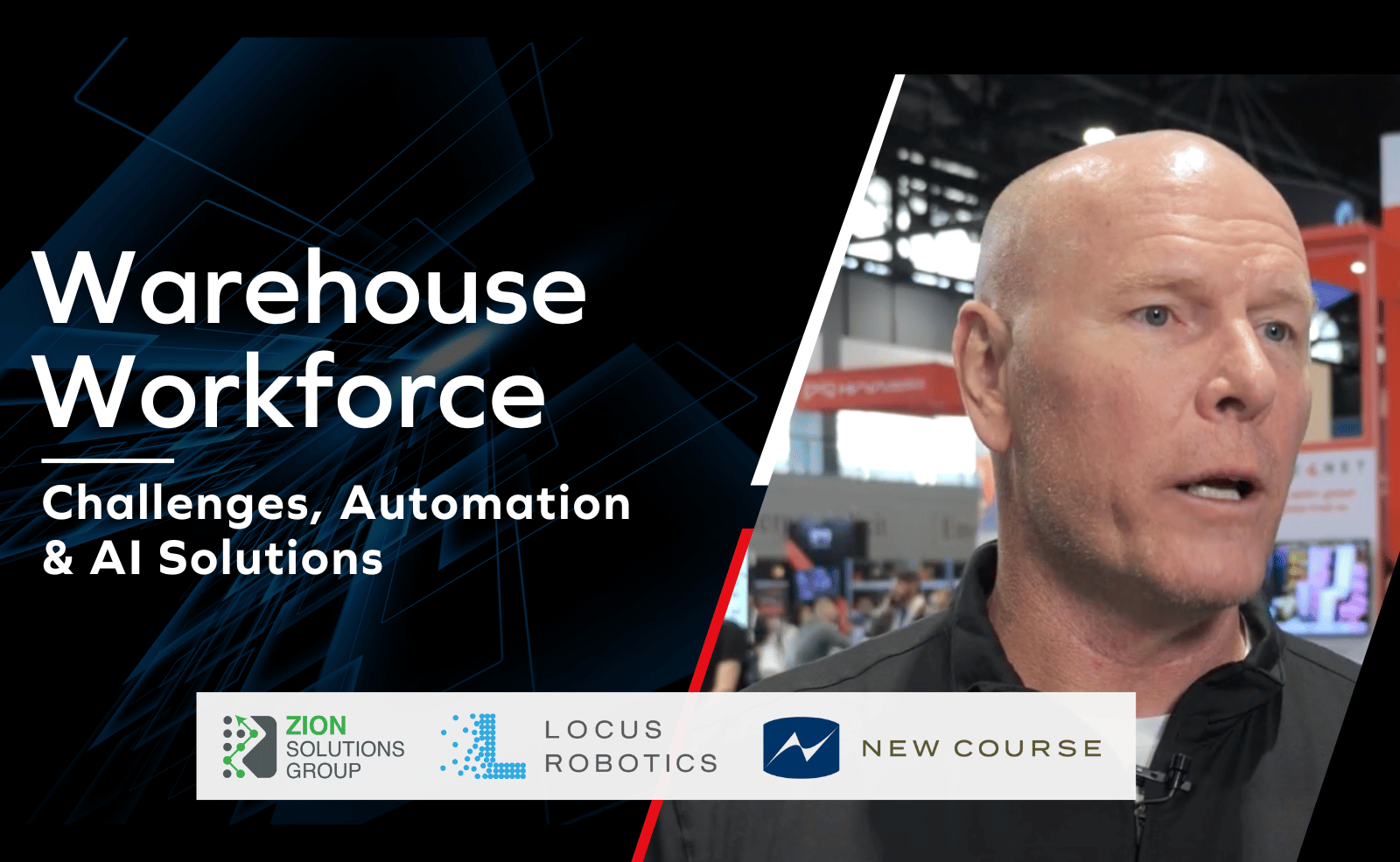
From rising costs and a shrinking labor pool to intensifying competition and market saturation, the warehouse industry is under pressure. Companies across the country are struggling to attract and retain warehouse talent while maintaining service levels and staying profitable. As we look to the future, one thing is clear: labor as we’ve known it is no longer a given. The path forward demands fresh thinking—about automation, labor management software, and the role of humans in the warehouse.
In this Q&A-style roundup, supply chain leaders dive into the current labor market and share how forward-thinking companies are addressing workforce challenges in 2025—with smart, scalable solutions that deliver real results.
What’s driving labor challenges in warehouses today?
Drew Eubank, Co-Founder and EVP – Engineering and Execution at Zion Solutions Group, doesn’t mince words: “Labor challenges are real—everyone’s pulling from the same talent pool. It’s market saturation.” As more distribution centers (DCs) pop up in the same regions, often within a few miles of each other, it’s become increasingly difficult to recruit and retain hourly associates.
And the economics have changed dramatically. “Five years ago, a full-time warehouse employee might cost $50K per year. Now it’s closer to $80K,” Eubanks says. He’s not exaggerating. The average warehouse worker hourly wage has jumped to nearly $19 as of late 2024, according to DC Velocity—up nearly 50% over the past half-decade.
That’s if companies can find workers at all. The warehousing sector faces a persistent labor shortfall—one recent estimate cited a shortage of more than 35,000 warehouse workers across the U.S. Meanwhile, turnover remains sky-high, especially as temp agencies compete on hourly rates and shift flexibility.
“Let’s be honest,” Eubanks adds. “Most people don’t grow up dreaming of working in a warehouse. So companies are getting creative with technology and innovation to attract people who actually want to be there.” The message is clear: culture, perks, and modern tools are becoming competitive differentiators—especially in dense markets where every warehouse is hiring.
How are companies addressing labor shortages?
Steve Simmerman, Vice President – Global Alliances at Locus Robotics sees no surprise in today’s labor crunch. “We’ve been talking about this for years. It’s here. It’s not going away,” he says. In fact, the industry has been leaning on temp labor for far too long, and it’s catching up with them.
More companies are taking action—specifically, by investing in automation. Simmerman notes that many are retrofitting their current DCs with simple, scalable automation that either enhances or replaces manual labor in certain zones. “You can redeploy associates to more critical tasks, or in some cases, just remove the need for human labor altogether in highly repetitive areas.”
That shift is happening in both small and large operations. In fact, research indicates that more than a quarter (26%) of warehouses are expected to be automated by 2027, from 14% just a decade earlier.
What trends are you seeing in automation adoption to counteract labor shortages?
John Sidell, CEO and Managing Principal at New Course Group, says the biggest trend he sees is the adoption of flexible automation—especially by mid-tier companies. “With flexible automation, you don’t need an 18-month deployment plan or massive capital investment. You can test and scale quickly,” he explains. “The ROI proves itself out faster, which gives leadership confidence to invest further.”
This agility is helping companies mitigate risk in uncertain labor markets. Sidell sees more companies trying robotics-as-a-service (RaaS) models or piloting mobile robotics in one zone before rolling it out across the DC. “It’s not just the giant Fortune 100 companies doing this anymore. Mid-sized operations are getting smarter and faster.”
And it’s not just physical automation. The integration of AI into warehouse workflows is accelerating too. According to Global Market Insights, the AI in warehousing market surpassed $8.3 billion in 2023 and is growing nearly 27% year-over-year. From AI-powered labor planning to intelligent task interleaving and real-time exception handling, companies are leaning on algorithms as much as physical robots to boost efficiency.
At the same time, collaborative robotics—or cobots—are transforming the human-machine dynamic. Rather than replacing workers outright, many systems are designed to support associates in picking, packing, and replenishment tasks, which not only improves productivity but reduces strain and injury.
Final Takeaway: Tech is the Talent Strategy
Warehouse leaders are no longer asking if they should automate—they’re asking how soon and how much. As wages rise and the talent pool tightens, automation and AI are quickly becoming the new frontline of labor strategy.
The key for most organizations will be to strike a balance: empower existing workers with better tools, redeploy labor where it adds the most value, and automate the tasks that drag productivity. Those who wait will find themselves outpaced not only by labor shortages but by competitors who are already operating faster, smarter, and leaner.
The warehouse workforce of 2025 is being shaped right now—and the smartest companies are building it with a powerful blend of human ingenuity and intelligent automation. Reach out to our experts for support.