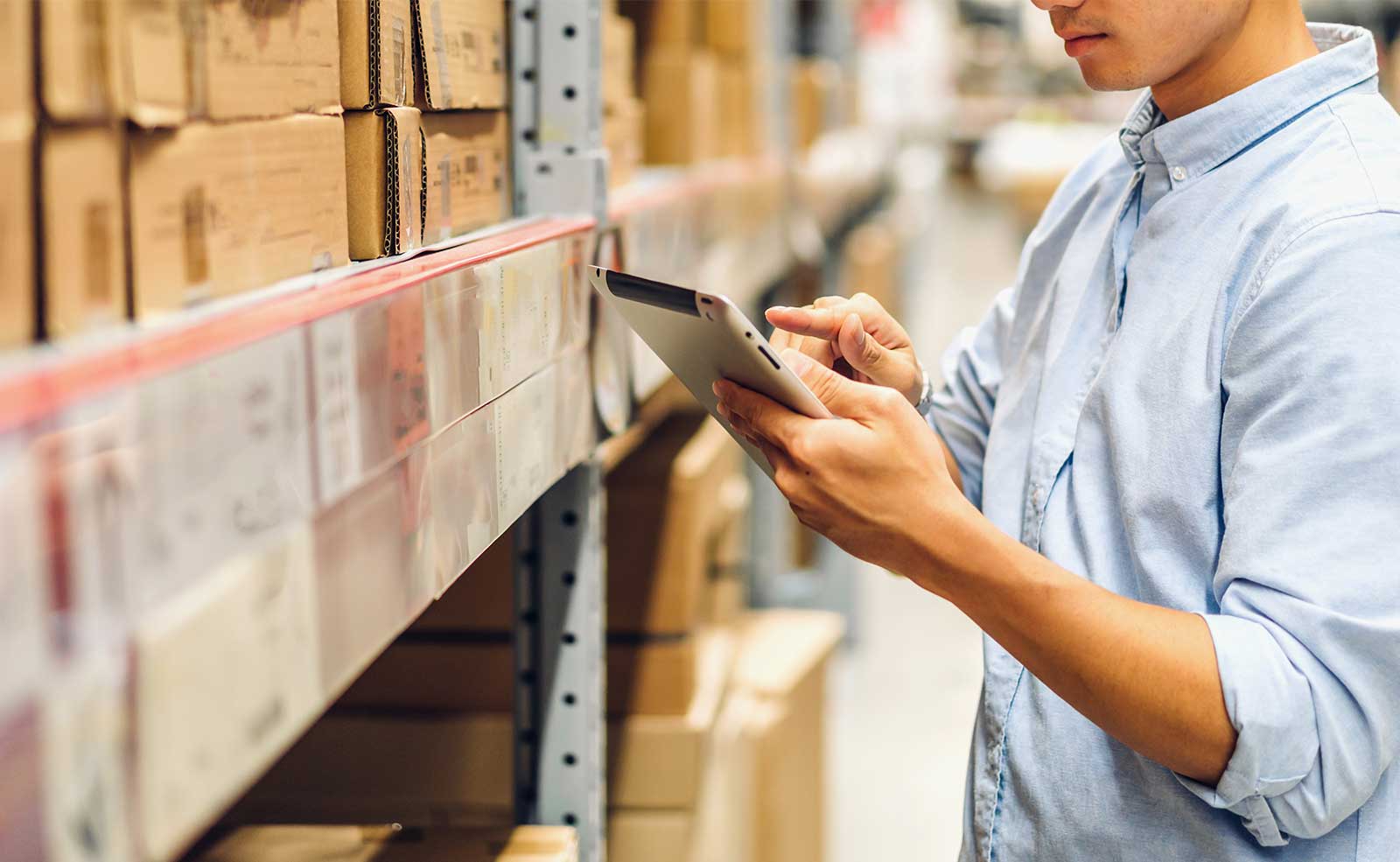
The emergence of advanced supply chain solutions has the potential to transcend the traditional limitations of warehouse optimization. Technology like a tier-one warehouse management system can optimize warehouse operations by streamlining processes, improving inventory accuracy, reducing cycle times, and enhancing customer satisfaction. Leveraging the best WMS for you can significantly enhance your warehouse efficiency an capacity.
In this article, we’ll cover:
- What is warehouse optimization?
- What are the six warehouse operations?
- How can you make warehouse operations more efficient?
- How do you optimize warehouse capacity?
- Top 5 tips for optimizing your warehouse
- How to measure success
- Final thoughts on warehouse optimization
What is Warehouse Optimization?
Warehouse optimization is a strategic process of utilizing the space and resources in a warehouse to ensure customer satisfaction. The main goal is to carry out warehouse operations while minimizing costs and improving speed and accuracy.
What are the Six Warehouse Operations?
Warehouse operations can vary significantly based on factors such as the type of goods stored, the scale of the operation, and the specific needs of the business. However, there are six fundamental warehouse processes that you will find at most facilities. These are:
- Receiving: Unloading incoming trucks, identifying, registering, and possibly repackaging goods.
- Putaway: Moving goods from the receiving dock to their designated storage location
- Storage: Placing goods in their most suitable storage spaces.
- Picking: Selecting items, either automatically or manually, based on customer orders for packing.
- Packing: Consolidating all picked items from a sales order and preparing them for shipment.
- Shipping: Dispatching packed orders to their respective customers as the final warehouse process.
How Can You Make Warehouse Operations More Efficient?
Top WMS systems enhance efficiency across the six fundamental warehouse processes by automating and streamlining each step.
Receiving
The main goal of optimizing the receiving process is to avoid the accumulation of received goods at the receiving dock. A WMS provides real-time tracking and receipt of goods, reducing errors and improving accuracy.
Putaway
When inventory is put away in the right place, it improves warehouse workflow. The travel time to reach the goods is less and the risks of damaged goods and accidents are significantly reduced. A WMS optimizes storage locations based on key item attributes, ensuring goods are placed in the best possible locations.
Storage
A WMS organizes the warehouse into zones and locations, enabling systematic putaway and easy access to items.
Picking
With a WMS you can deploy batch and wave picking. This means you can group similar orders or items to be picked together, reducing the time and effort required to fulfill orders. A WMS also enables pick path optimization meaning it will calculate the most efficient routes for pickers, minimizing travel time and increasing picking speed. Integrating wearables and wireless mobile devices with your WMS also increases picking speed and reduces errors.
Packing
A WMS consolidates picked items for each order, guides packers through optimized packing workflows, and provides real-time validation to ensure that the correct items are packed according to customer specifications. The system can also generate and print shipping labels, packing slips, and documentation, reducing errors and streamlining the entire process from picking to shipping.
Shipping
A WMS facilitates the organization of packed orders, assigns them to the correct carriers, and schedules shipments based on delivery priorities and customer requirements. The system also generates shipping labels, tracking information, and necessary documentation, reducing errors and streamlining the final stage of order fulfillment. Additionally, a WMS provides real-time visibility into shipment status, enabling better management of logistics and improved customer communication.
How Do You Optimize Warehouse Capacity?
Warehouse capacity can fluctuate due to factors like business growth, seasonal demand, and product line changes. Expanding inventory or entering new markets often necessitates additional space, while peak seasons and supply chain adjustments can alter capacity needs. Technological advancements and operational efficiency initiatives can improve space utilization, and shifts in regulations, economics, or customer demands may require further adjustments. Mergers, acquisitions, or divestitures can also impact capacity requirements. Understanding these dynamics is crucial for managing warehouse space effectively to meet evolving needs.
Here are a few tips to help you optimize your warehouse capacity.
Evaluate your current warehouse setup
Assess your warehouse layout to identify potential hazards and inefficiencies. Consider modernizing equipment or redesigning the layout to enhance safety and space utilization.
Define your objectives and pain points
Clearly articulate your goals, such as accommodating increased customer demand, reducing “just in case” inventory or reducing warehouse accidents. Specific objectives will guide your strategies for optimizing warehouse capacity.
Implement smart shelving systems
Upgrade from static shelving to dynamic solutions like mobile racking and gravity flow racking. For instance, pallet flow racking uses inclined rails and rollers to efficiently move pallets to the front for easier picking.
Enhance warehouse layout design
Optimize your physical layout by placing high-turnover goods near the shipping area to reduce picking times. Designate specific areas for returns to streamline reverse logistics and improve overall efficiency.
Top 5 Tips for Optimizing Your Warehouse
The ultimate aim of warehouse optimization is to reduce costs, improve speed and accuracy, and increase overall productivity while maintaining safety, complying with regulations and meeting your Service Level Agreements. The following 5 tips can help you meet these goals:
1. Implement a WMS for Warehouse Optimization
Savvy operators understand the importance of a warehouse management system. Implementing a WMS optimizes a warehouse by automating key processes such as inventory tracking, order picking, and stock replenishment, leading to increased accuracy and efficiency. It provides real-time visibility into inventory levels and order statuses, which helps streamline operations and reduce errors. Additionally, a WMS enhances space utilization and productivity through advanced data analytics and optimized workflow management.
2. Invest in Warehouse Automation and Robotics
Unlike traditional warehouses that rely on workers’ physical strength and speed, warehouse and 3PL automation offers high flexibility, consistency and reliability. Robotic order picking can automate product handling from receiving to shipping. When order volumes or business needs change, robotics can adapt easily without sacrificing speed or accuracy.
3. Integrate IoT (Internet of Things) Devices
IoT devices like asset-tracking devices can pinpoint the exact location of goods saving time during picking. Sensors can monitor temperatures and humidity levels to assess the condition of perishable goods. Such insights can save on losses that could have occurred from damaged goods.
4. Organize Inventory Based on Product Velocity
By organizing inventory based on product velocity, warehouses can improve picking efficiency, reduce handling costs, and enhance overall operational performance. To achieve this you must first classify products by velocity then use an ABC analysis to organize and optimize storage locations. A-Class Items will be high-velocity, high-value items that should be placed in easily accessible locations. B-Class Items will be moderate velocity and value items that need reasonable accessibility. And, C-Class Items will be low-velocity, low-value items that can be stored in less accessible locations.
5. Practice Regular Training & Development
Training warehouse staff optimizes processes by ensuring that employees are proficient in using systems and following WMS best practices, which reduces errors and increases efficiency. Well-trained staff can handle tasks such as inventory management, order picking, and packing more effectively, leading to faster processing times and improved accuracy. Additionally, training helps in maintaining safety standards and adapting to new technologies or procedures, further enhancing overall operational performance.
How to Measure Success: 9 KPIs to Track Success of Warehouse Optimization
Warehouse KPIs are often unique to an operation, and not all metrics apply to all operations. But, in our opinion, there are 9 KPIs for an Efficiently Managed Warehouse. They are:
- Order Fulfillment: Measures the percentage of customer orders completed and delivered on time, reflecting efficiency in processing and shipping.
- Inventory Accuracy: Tracks the precision of inventory records compared to actual stock, ensuring reliable data for effective management.
- Overall Throughput: Indicates the total volume of goods processed through the warehouse, assessing the efficiency of operations.
- Replenishment: Monitors the timely restocking of inventory to maintain optimal levels and prevent stockouts.
- Order Accuracy: Evaluates the percentage of orders picked and shipped correctly, ensuring customer satisfaction and minimizing returns.
- Inventory Turns: Measures how often inventory is sold and replaced over a period, indicating the effectiveness of inventory management.
- Dead Stock: Represents inventory that has not moved or sold over a specific period, highlighting potential issues with product demand or stock management.
- Supplier KPI: Assesses supplier performance based on criteria such as delivery timeliness, quality, and compliance, impacting overall supply chain efficiency.
- Customer Satisfaction: Gauges the level of satisfaction customers have with their orders and service, reflecting the effectiveness of warehouse operations and fulfillment processes.
Final Thoughts on Warehouse Optimization
Learning how to optimize warehouse operations means embracing cutting-edge technology to create an optimized ecosystem. Leveraging the power of WMS can help your business achieve warehouse optimization, unlocking benefits such as enhanced efficiency and accuracy to improve customer experiences and cost savings. To learn more about Made4net’s WarehouseExpert WMS solution, schedule a demo with us.