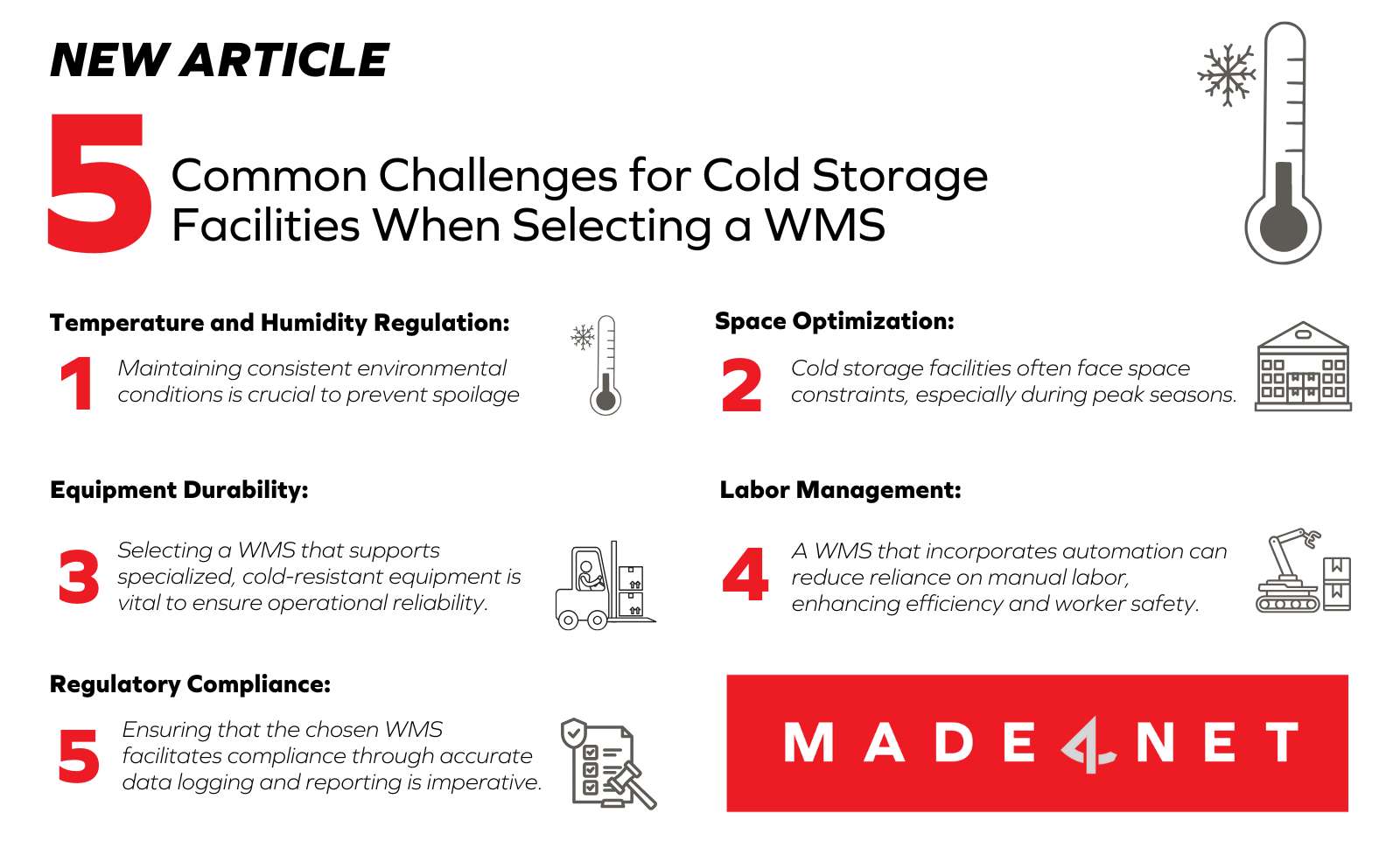
Industries handling temperature-sensitive products—such as food, beverage, and pharmaceuticals— need a robust and dependable food and beverage Warehouse Management System (WMS) to keep up with ever-changing standards and regulations. This is where a cold storage WMS shines, empowering providers to stay on the right side of compliance without compromising functionality. But what makes a cold storage WMS right for the job?
In this article, we’ll find out, by exploring:
- What is a cold storage warehouse management system (WMS)?
- How does a cold storage warehouse management system work?
- What are the most important features of a cold storage WMS?
- What are the benefits of a cold storage warehouse management system?
- What are common challenges for cold storage facilities when selecting a WMS?
What is a Cold Storage Warehouse Management System (WMS)?
A cold storage WMS is a specialized software solution designed to optimize the operations of warehouses that store temperature-sensitive products, including perishable foods, beverages, and pharmaceuticals that require precise environmental control. These systems address the unique challenges of managing perishable goods, ensuring that products are stored and handled under appropriate conditions to maintain quality and safety. In addition to standard WMS features, cold storage WMSs include temperature and humidity tracking, lot and expiration date management, real-time cold chain monitoring, automated compliance documentation for food safety regulations (e.g., FDA, USDA, FSMA), multi-zone temperature mapping, and workflow optimizations to minimize dwell time outside of temperature-controlled areas. These systems also support specialized picking and replenishment strategies to maintain product integrity and reduce spoilage.
How Does a Cold Storage Warehouse Management System Work?
A WMS ensures all aspects of warehouse management are optimized, from receipt of goods and storage, all the way to outbound shipping. The operation of a Cold Storage WMS can be delineated into several key stages:
- Receiving:
- Data Capture: Upon arrival, goods are inspected and relevant data—such as product type, quantity, lot numbers, and expiration dates—are recorded into the WMS.
- Temperature Logging: For perishable items, initial temperature readings are taken to ensure compliance with required storage conditions.
- Storage:
- Allocation: The WMS assigns storage locations based on product-specific temperature requirements, optimizing space and ensuring efficient retrieval.
- Environmental Monitoring: Continuous tracking of storage conditions, including temperature and humidity, is maintained to preserve product integrity.
- Order Fulfillment:
- Order Processing: Customer orders are received and processed by the WMS, which identifies the required products and their storage locations.
- Picking and Packing: Guided by the WMS, staff retrieve items, ensuring adherence to First-In-First-Out (FIFO) or First-Expired-First-Out (FEFO) principles to minimize spoilage.
- Shipping:
- Preparation: Products are consolidated, packed, and labeled according to customer specifications and regulatory standards.
- Dispatch: The WMS schedules shipments, generates necessary documentation, and updates inventory records to reflect the outgoing goods.
While it’s not an absolute requirement, integrating sensors significantly enhances the functionality of a cold storage WMS, allowing for real-time monitoring, automated alerts, data logging, and compliance. Through a systematic sequence of receiving, storage, order fulfillment, and shipping processes, a cold storage WMS empowers food and beverage providers to improve operational efficiency, enhance productivity, reduce waste, and ensure the integrity of temperature-sensitive goods.
What are the Most Important Features of a Cold Storage WMS?
The goal of any WMS is to enhance overall operational efficiency. For a cold storage WMS, this also means maintaining the integrity of the cold chain, which is achieved through these key features:
Cold Storage WMS Feature #1: Temperature & Humidity Monitoring
A cold storage WMS continuously tracks and records temperature and humidity levels in real time. Automated alerts and notifications trigger corrective actions when conditions deviate from required thresholds, preventing product degradation and ensuring compliance.
Cold Storage WMS Feature #2: Inventory Control & Expiration Management
With lot tracking, batch management, and expiration date monitoring, a cold storage WMS ensures proper stock rotation (FIFO, FEFO) to reduce waste and maintain compliance. This is especially critical for food and pharmaceuticals, where temperature-sensitive products must remain safe and effective.
Cold Storage WMS Feature #3: Regulatory Compliance & Audit Readiness
Cold storage operations must adhere to strict FDA, USDA, FSMA, and other industry regulations. A cold storage WMS automates compliance documentation, maintains audit trails, and generates detailed reports, ensuring all storage conditions meet regulatory standards with minimal manual effort.
Cold Storage WMS Feature #4: Order Fulfillment & Picking Optimization
By automating order processing, picking, and packing, a cold storage WMS ensures timely and accurate deliveries while minimizing the time products spend outside controlled environments. Advanced picking strategies (batch, wave, or zone picking) improve efficiency while reducing labor costs.
Cold Storage WMS Feature #5: Cold Chain Visibility & Transportation Integration
A cold storage WMS integrates with transportation management systems (TMS) and real-time tracking solutions to monitor product conditions during transit. This ensures end-to-end cold chain visibility, enabling proactive intervention if temperature deviations occur.
Cold Storage WMS Feature #6: Seamless System Integrations
An advanced cold storage WMS seamlessly integrates with ERP, TMS, IoT sensors, and third-party compliance systems to ensure data-driven decision-making, streamline operations, and enhance visibility across the entire supply chain.
By leveraging these specialized features, a cold storage WMS helps operations maintain compliance, reduce waste, optimize workflows, and safeguard product integrity throughout the supply chain.
What are the Benefits of a Cold Storage Warehouse Management System?
A cold storage WMS offers several advantages from inventory accuracy to regulatory compliance. Let’s explore the key advantages of implementing the solution.
Cold Storage WMS Benefit #1: Enhanced Inventory Control
A robust cold storage WMS ensures precise inventory control with lot tracking, batch management, and expiration date monitoring, enabling proper stock rotation to reduce waste and maintain product quality.
Cold Storage WMS Benefit #2: Real-TimeTraceability
With a documented record of every product movement, a cold storage WMS provides end-to-end visibility from receipt to shipment. This traceability is critical for batch recalls, allowing operations to quickly and efficiently remove affected products, ensuring safety and compliance.
Cold Storage WMS Benefit #3: Regulatory Compliance
A cold storage WMS simplifies compliance by automatically logging product conditions, generating detailed reports, and facilitating audits to meet industry regulations. This is especially crucial for pharmaceuticals, where stringent oversight demands precise documentation of storage conditions and chain of custody.
Cold Storage WMS Benefit #4: Reduced Waste
By leveraging temperature monitoring and automated alerts, a cold storage WMS helps maintain ideal conditions for perishable goods, minimizing spoilage and ensuring food safety.
Cold Storage WMS Benefit #5: Optimized Labor Utilization
With automated workflows for picking, packing, and replenishment, a WMS improves labor efficiency by aligning with engineered labor standards, reducing manual efforts, and maximizing workforce productivity.
Cold Storage WMS Benefit #6: Cost Savings
By reducing food waste, enhancing operational efficiency, and streamlining delivery processes, a cold storage WMS helps operations protect their bottom line while ensuring product integrity.
What are Common Challenges for Cold Storage Facilities When Selecting a WMS?
WMS selection is a complicated process, and the unique needs of a cold storage facility adds its own brand of complexity to account for. Operations looking to implement a cold storage WMS are usually looking to address these five common challenges:
- Temperature and Humidity Regulation: Maintaining consistent environmental conditions is crucial to prevent spoilage. Fluctuations can compromise product integrity, necessitating a WMS capable of real-time monitoring and control.
- Space Optimization: Cold storage facilities often face space constraints, especially during peak seasons. Implementing high-density storage solutions and efficient layout designs is essential to maximize capacity within the limited footprint.
- Equipment Durability: Low temperatures can adversely affect both human health and equipment performance. Selecting a WMS that supports specialized, cold-resistant equipment is vital to ensure operational reliability.
- Labor Management: Working in cold environments poses challenges for staff, including health risks and decreased productivity. A WMS that incorporates automation can reduce reliance on manual labor, enhancing efficiency and worker safety.
- Regulatory Compliance: Cold storage operations must adhere to stringent industry standards and regulations. This is particularly true for pharmaceuticals, where regulatory bodies such as the FDA and EMA require precise documentation, controlled access, and traceability. Ensuring that the chosen WMS facilitates compliance through accurate data logging and reporting is imperative.
Is a Cold Storage WMS Right for You?
If your operation handles temperature-sensitive products, a cold storage WMS can be a game-changer, ensuring efficiency, compliance, and product integrity. Made4net customer, Arctic Logistics, a leader in temperature-controlled warehousing, faced challenges with manual processes, inventory inaccuracies, and the need for better cold chain visibility. After implementing Synapse 3PL Expert from Made4net, they saw faster operations, reduced errors, and improved customer service, all while maintaining strict temperature controls. By automating workflows, enhancing inventory accuracy, and reducing waste, Arctic Logistics now operates more efficiently while keeping costs in check.
Whether you’re managing perishable food, pharmaceuticals, or other climate-sensitive goods, a WMS provides real-time monitoring, seamless integrations, and compliance tracking to protect your products and streamline operations. Contact the experts at Made4net to explore how a cold storage WMS can transform your operations.
If you’re exploring WMS solutions, check out this guide to selecting a cold storage WMS.