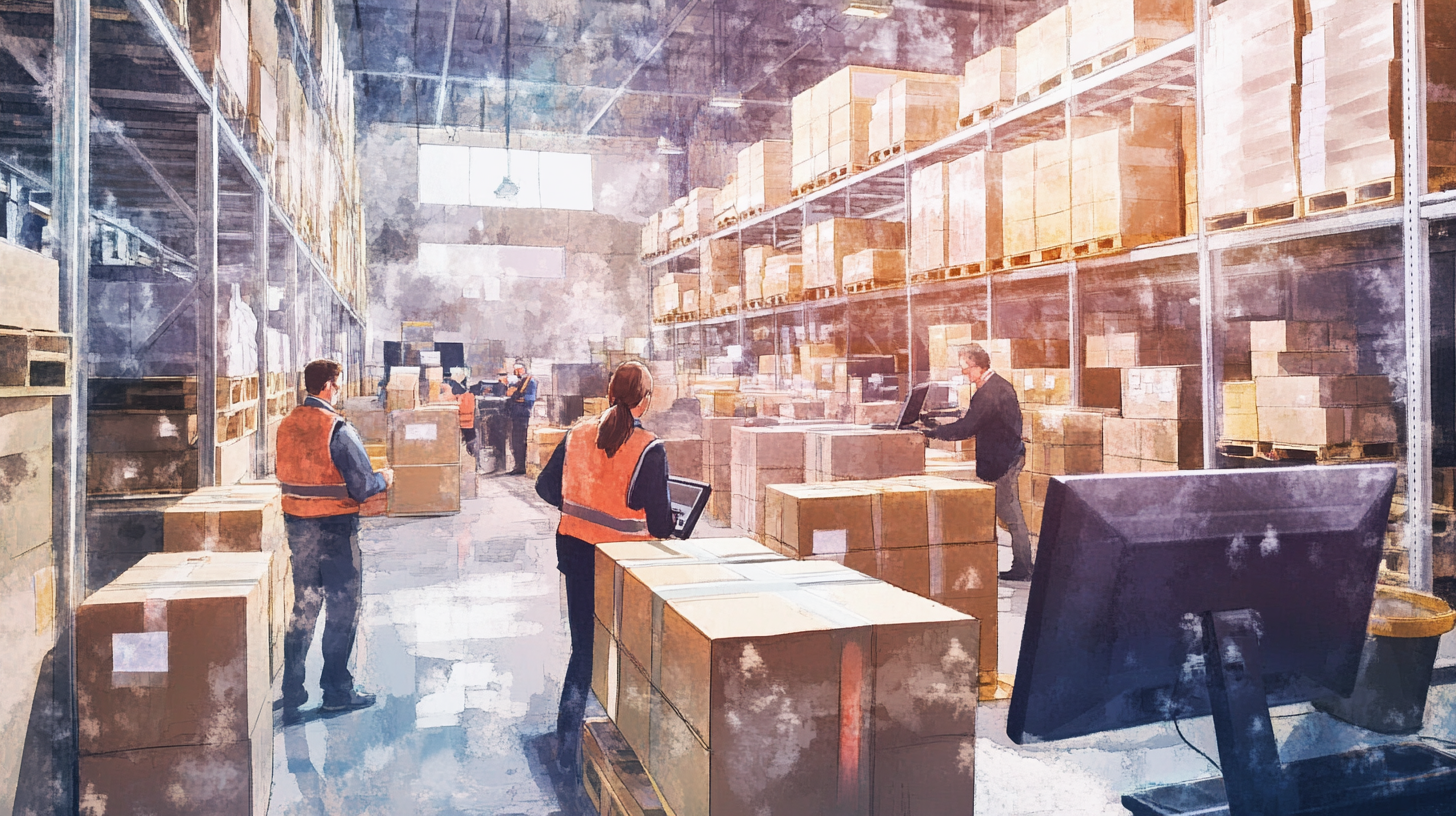
A warehouse management system (WMS) is the brain of your distribution operation, the backbone of your supply chain. The right WMS improves inventory visibility, optimizes picking processes, helps boost labor efficiency, and reduces errors. And while there are many different types of warehouse management systems, there is only one that is right for your operation. There are several important steps in the WMS selection process, such as planning, defining business requirements, and identifying Key Performance Indicators (KPIs). However, one step we believe holds particular value is learning from real-world examples of warehouse management system implementations.
In this article, we’ll cover:
- The importance of warehouse management system examples in your search
- What makes a WMS example successful?
- How to vet WMS references and examples
- Best-in-class warehouse management system examples
The Importance of Warehouse Management System Examples in Your Search
With the vast array of warehouse management system (WMS) vendors available today, selecting the right one can be challenging. Resources like the Gartner Magic Quadrant for Warehouse Management Systems can help you identify top-ranked providers, while revisiting vendors you’ve previously worked with or seeking recommendations from your network can also be valuable. One of the most effective strategies is to speak with references currently using the system you’re considering. This approach provides first hand insights into the system’s performance, user-friendliness, and overall operational impact.
Leverage the experiences of others to make an informed decision. Prioritize speaking with current users in your industry to gain relevant, practical insights into how the system performs in real-world scenarios. Engaging with references allows you to:
- Gain a thorough understanding of operational fit. Real-life examples in warehouses with similar product types, order volumes, and workflows will demonstrate how the system works in specific settings.
- Get a first-hand account of how the system performs under pressure and how it handles disruptions.
- Gauge WMS strengths and weaknesses in light of real-life events, not simulated demonstrations.
- Understand the tangible benefits other companies have achieved, and give you a realistic idea of the system’s potential ROI.
- Gather potential best practices and lessons learned during the implementation that you can use to your advantage.
With a thorough understanding of real-life warehouse management examples, you can feel confident in your decision, knowing that you have found a system proven to work effectively in a setting similar to yours.
What Makes a WMS Example Successful?
What makes a WMS example successful will depend largely on specific operational needs. This is why having a deep understanding of your operational requirements is critical during the selection phase. When looking for examples to learn from, make sure the example you’re reviewing matches your needs. If you require all traditional warehouse WMS functions, plus yard management, dock scheduling, labor reporting, and shipment processing, the reference vetted should be using all those features as well, so you’re comparing apples to apples.
As you evaluate an example you will want to consider:
- If the WMS is integrated seamlessly into processes and workflows
- If there are fewer errors post-WMS implementation
- If the system is stable during peak times or when working through a disruption
- If the system has been able to scale with the business as needed
- How well users have adopted the new technology
- How well the WMS facilitates compliance with industry standards
More importantly, you want to speak to employees on the warehouse floor to learn what their experience has been. They will have a far better, and more honest, review of what works and what needs to improve. Interviewing employees will provide details on whether the WMS has improved service levels, such as faster delivery times, improved accuracy, or better communication.
How to Vet WMS References and Examples
The whole point of this exercise is to get real, timely, and honest feedback on the system you’re evaluating. Visit at least one current customer and make sure they are:
- Using the version of software you are evaluating, best case scenario, the most current version of the software.
- In an industry or operating environment that closely matches your current or end-state goals.
- Open to letting you perform a 360° evaluation of the vendor, including software, infrastructure, implementation, pros/cons, and words of advice.
There may be dozens of different questions you may want to ask. Many of those questions will be informed by your industry, size, and needs, but below are the top five questions we believe are critical to zeroing in on the information you need to make an informed decision you can feel good about.
WMS Example Question #1: How easy was the implementation process and how long did it take?
This is your chance to hear the full implementation story—not just the sales pitch. Was the project completed on time and within budget? Were there any delays or overspending, and how did the vendor handle and communicate those challenges? This insight provides valuable information about how the vendor operates under pressure and what you can expect in similar situations.
WMS Example Question #2: What kind of support does the WMS provider offer?
Implementing a WMS is a significant investment, and with it comes the expectation of reliable support and expertise during the transition. Hearing first-hand accounts of the vendor’s support can help you determine if they’re the right fit. If dependable, responsive assistance is a priority for you, and a reference indicates the vendor was largely unavailable, that could be a dealbreaker. Don’t hesitate to dive into the details of what you can expect.
WMS Example Question #3: What are their response times?
Equally important to receiving support is the timeliness of the vendor’s response. Your operations need to run seamlessly, and prolonged delays in resolving errors can bring them to a standstill. Ensure the vendor can be relied upon for prompt troubleshooting and quick fixes.
WMS Example Question #4: How well does the system handle exceptions or disruptions?
While understanding how a WMS performs under normal conditions is valuable, its true measure lies in how it handles exceptions and disruptions. Learning how the system operates during unexpected events is critical, and reference users may even share tips or lessons learned to smooth your implementation process. Since exceptions are inevitable in any operation, it’s essential to assess whether the system can manage them effectively. For many organizations, this capability becomes a deciding factor in determining whether the investment is worthwhile.
WMS Example Question #5: How much maintenance does the WMS require?
You want to understand the true level of ongoing maintenance or updates needed to keep the system running smoothly. While routine updates and maintenance are expected, frequent disruptions or overly complex processes could negatively impact your productivity and operations. Ask whether maintenance requires downtime and, if so, how long it typically lasts. If the maintenance burden is too high, it may outweigh the benefits of the system.
Best-in-class Warehouse Management System Examples
There is no substitute for a direct conversation with an operation that can answer your questions in real-time. However, equally as beneficial are case studies highlighting how the system operates in a particular setting. We’ve had the pleasure of working with a variety of businesses spanning a slew of verticals that we’re sure will answer some of your most pressing questions.
WMS Example: eCommerce Operations
“Since we implemented Made4net’s WMS, we’ve been able to meet our customers’ needs and ship out orders for one-day delivery at a high accuracy rate. The platform is easy to use and to train new users on, making it an ideal solution for our fast-paced environment.”
— Torion Todd, Business Operations Manager, Material Bank
When Material Bank, the world’s largest material resource library for architects and designers, began scaling its operations, it faced growing challenges in meeting its commitment to ship all samples ordered by midnight for next-day delivery. Struggles with inventory management, order processing efficiency, and complex, custom workflows prompted them to implement Made4net’s WarehouseExpert Warehouse Management System (WMS).
Since adopting the WMS, Material Bank has improved its order accuracy by 10-20%, ensuring next-day delivery commitments are met with greater consistency. Warehouse productivity has increased by 20-30%, and the system’s robust design has significantly enhanced their ability to manage large order volumes. These improvements have not only streamlined operations but also elevated customer satisfaction and loyalty, reinforcing Material Bank’s reputation for reliability and precision.
WMS Example: Food & Beverage
“The positive effects of having the Made4net solution in our distribution centers were immediate in terms of quality control, labor productivity, absolute inventory control, and better fulfillment service to our stores.”
— Vice President of Supply Chain, Sprouts Farmers Market
When Sprouts reached the 40-store milestone, their paper-based processes became increasingly cumbersome, struggling to manage growth, higher volumes, and the complexity of warehouse operations. They aimed to guarantee next-day delivery for all orders while addressing pressures related to inventory accuracy, labor efficiency, and quality control. That’s when they turned to Made4net.
Since implementing Made4net’s WMS, Sprouts has achieved a 32% improvement in inventory accuracy within a six-month period compared to the previous year. Picking efficiency has increased by up to 25%, and the most significant benefit has been the ability to handle higher fulfillment volumes across all distribution centers while maintaining productivity gains with their existing workforce. Today, Sprouts operates three distribution centers servicing more than 215 retail locations nationwide.
WMS Example: 3PL
“We’ve gotten exceptional service from the Made4net team, from super user training to asking questions daily. We’ve been able to move forward, working with a truly exceptional software company.”
— Ryan Connor, Arctic Logistics, Head of Sales and Operations
When Arctic Logistics, a 3PL specializing in refrigerated warehousing for Fortune 500 and Fortune 100 companies, outgrew their existing WMS, they recognized the need for a transformative solution to manage their 150,000 square feet of storage and 20,000 pallet positions. After careful evaluation, they implemented Made4net’s Synapse 3PLExpert.
Since adoption, Arctic Logistics has achieved significant operational improvements. Picking accuracy has increased, shipping processes have been streamlined, and they’ve maintained perfect inventory management—without a single pallet expiring. The system’s capabilities have enabled proper product rotation, enhancing customer satisfaction while safeguarding their bottom line.
Conclusion
If you’ve been tasked with the responsibility of selecting a new WMS, embark on the journey with knowledge. You can request a demo, work with a WMS consultant, and speak to references to discover what system works best for you. We’re here to answer any questions you might have, just reach out to speak to an expert.