Food & Beverage WMS
Fresh, Fast, Flawless: Deliver the goods with Made4net’s Food & Beverage WMS
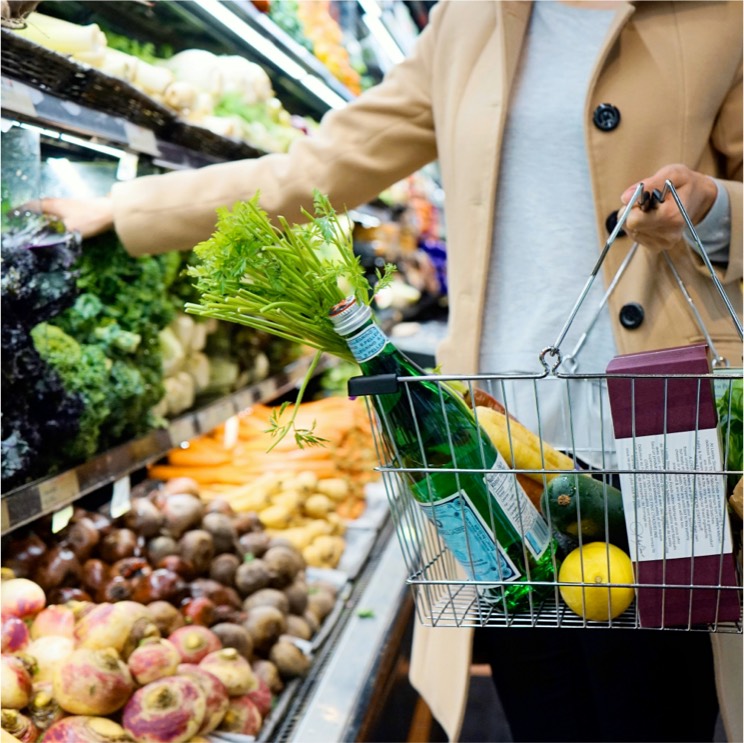
Move Fast. Stay Compliant. Maximize Every Margin.
Tight margins. Ever-changing regulations. Rising customer expectations. In the food and beverage industry, the pressure is constant and the stakes are high. From managing perishable inventory and tracking expiration dates to ensuring compliance and meeting aggressive SLAs, your supply chain has to run with speed, accuracy, and total visibility.
Made4net’s Food & Beverage WMS is built to handle it all. Our deep industry expertise is woven into every feature—rules-based shipping, shelf-life tracking, optimized picking, and real-time KPI monitoring—so you can move faster, stay compliant, and protect every ounce of ROI.
We help businesses like yours turn complexity into control—and challenges into competitive advantages.
Built for Precision: Accuracy, Compliance, and Speed in Every Workflow
Advanced Inventory Control
Track lot, batch, expiration, and shelf life using FIFO/LIFO logic to ensure freshness and reduce spoilage.
Compliance-Ready Workflows
Meet food industry standards with built-in support for PTI, GS1, EDI, and customizable labeling and documentation.
Recall & Traceability Management
Enable full end-to-end traceability for fast, accurate recalls and stronger regulatory compliance.
Integrated Voice Picking
Boost picking speed and accuracy with voice-enabled workflows tailored to high-volume, fast-moving inventory environments.
Made4net Food & Beverage Customers See Real Results
- Reduced inventory and fulfillment errors
- Increased labor efficiency with engineered standards
- Lower shrinkage, spoilage, and waste
- Continuous cost savings across the operation
- Smooth handling of seasonal and promotional surges
- Scalable workflows that support ongoing growth
Run Your Entire Operation on a Single Platform
What our customers are saying
Warehouse Management System FAQs
Food and beverage operations involve unique challenges like managing perishable goods, ensuring traceability, and meeting strict regulatory requirements. A specialized WMS helps streamline receiving, storage, picking, packing, and shipping while ensuring temperature control, inventory rotation, and real-time visibility. This reduces waste, prevents spoilage, and supports compliance with FDA, HACCP, PTI, and GS1 standards.
The system supports full traceability and end-to-end tracking, including lot and batch control, expiration date management, and compliance with food safety regulations like HACCP, FSMA, and PTI. It also facilitates proper labeling and documentation using GS1 and EDI standards, making it easier to prepare for audits and handle recalls quickly and efficiently.
The platform offers robust integration capabilities with ERP, TMS, and other third-party systems. This ensures seamless data exchange across the supply chain, supports streamlined workflows, and enables a unified view of operations—making it easier to manage inventory, orders, and transportation in real time.
Yes! The Made4net WMS is designed to manage inventory across various temperature-controlled zones, including ambient, refrigerated, and frozen areas. It supports temperature and humidity tracking to ensure product integrity and safety throughout the warehouse. Items can also b
The system supports intelligent order picking methods such as wave and batch picking, and incorporates tools like voice picking for hands-free operation in cold or gloved environments. It also manages FIFO, LIFO, and FEFO picking rules to minimize spoilage and ensure freshness while maintaining high throughput and customer satisfaction.
Absolutely. The WMS is built to support flexible workflows that accommodate seasonal surges, promotional activities, and demand variability. Its rules-based engine allows businesses to adapt quickly to changes in volume, product mix, or customer expectations without sacrificing speed or accuracy.