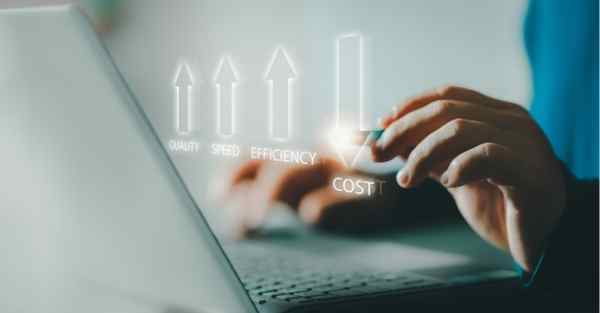
A 3PL warehouse management system serves as the backbone for efficient operations, enabling seamless management of inventory, orders, and warehouse activities. While these systems are essential for business, understanding their true cost is critical for justifying the investment and ensuring a positive return on investment (ROI). The cost of a WMS goes beyond just the software license—it includes upfront expenses, ongoing fees, and potential hidden costs that can significantly impact the total investment. This article breaks down the key elements that contribute to the overall cost of WMS software for 3PL providers, helping companies make informed decisions when selecting the best WMS for their unique needs.
- Variables That Affect Your 3PL Software Pricing
- What are 3PL Fees?
- What is the Best WMS Software for 3PL providers?
- SaaS vs. Perpetual: What’s the Best 3PL Software Pricing Option for You?
- Next Steps: 3PL Software Pricing
Variables That Affect Your 3PL Software Pricing
3PLs face several challenges. As service providers handling the supply chain functions of other businesses—such as shipping, storage, packing, inventory management, customer service, and freight brokerage—they must be equipped to offer a wide range of services. Multiple factors directly impact the pricing of 3PL software, depending largely on the complexity of operations.
When it comes to 3PL Warehouse Management Systems (WMS), there are three levels of sophistication that affect pricing:
- Tier 1 3PL WMS: Ideal for operations with advanced needs, high volumes, and automation interfaces.
- Tier 2 3PL WMS: An intermediate solution offering comprehensive functionality.
- Tier 3 3PL WMS: A basic system providing simple inventory control.
3PL software pricing also depends on specific capabilities related to operational complexity. Examples include:
- Enhanced Automation: Automation tools such as AGVs, robotics, and AS/RS can help 3PLs efficiently manage multi-client warehouses with high-volume and high-frequency tasks.
- Integration Capabilities: Connections with Transportation Management Systems (TMS), Enterprise Resource Planning (ERP) systems, and Customer Relationship Management (CRM) tools.
- Real-Time Data and Analytics: Advanced real-time data analytics and reporting capabilities.
- Advanced Inventory Management: Features like RFID tracking, barcode scanning, and cycle counting.
- Labor Management: Tools for optimizing workforce productivity.
Beyond these options and customizations, 3PLs should also budget for additional fees.
What are 3PL Fees?
When considering 3PL software pricing, it’s important to understand all the costs that will come into play, including implementation, integration, training, maintenance, and even some unforeseen costs. These fees can be significant and should be factored into your budget.
- Implementation: Implementation costs for a 3PL WMS can range from $65,000 to $150,000. This fee includes initial system configuration, data migration, and testing. However, subsequent warehouse setups become more affordable as your team gains experience from the initial implementation.
- Integration: Integrating with existing systems like a TMS or ERP can range from $10,000 to $80,000, and integration with automation and robotics incurs a separate fee, usually between $30,000 to $150,000. Data migration also costs extra, usually between $10,000 and $30,000. For many 3PLs, these are unavoidable costs as integrating with these systems is essential for handling the complexity of the operation.
- Training: The success of any new system deployment is largely dependent on the team that runs and manages it, so training is critical. Training costs may be included in the implementation fee, but some vendors charge additional fees in the range of $5,000 to $50,000, depending on the number of users and the depth of training required. You want to ensure all users are proficient and able to address any issues as they arise.
- Maintenance: Complex software like an on-premise WMS requires ongoing maintenance and support to cover updates, upgrades, security patches, and tech support. As such, most WMS packages include the additional cost of this ongoing support, which is part of the contract.
- Hidden fees: It’s not always easy to determine what hidden costs there may be, so be sure to ask your software vendor about them during the selection process. 3PL software pricing will vary by provider, as will the many fees, but you can learn if there are:
- Additional fees associated with extra users, devices, or modules
- Infrastructure costs associated with new servers or networking equipment
- Scaling costs
- Upgrade costs
- Ongoing user training fees
- Fees associated with data migration issues
- The cost of underutilized features
The fees will also change based on the kind of WMS software chosen. There are over 200 different types of 3PL solutions that fall under four main categories: Standalone, Supply chain management (SCM) module, Enterprise resource planning (ERP) module, and Cloud-based. So, how do you know which is the best for your operation?
What is the Best WMS Software for 3PL providers?
In this fast-paced and competitive supply chain landscape, 3PL providers need efficient warehouse management to succeed. While every operation will have a varied set of needs, there are certain WMS features we believe 3PLs need if they want to stay ahead.
- Detailed billing: A 3PL WMS should support detailed billing capabilities, particularly for value-added services (VAS) such as repackaging, custom labeling, or kitting, ensuring these are accurately tracked and aligned with client agreements.
- Analytics and reporting: Detailed, flexible, and thorough reporting capabilities are necessary for informed decision-making. This includes access to real-time data and comprehensive performance history information.
- Detailed inventory insights: Comprehensive inventory tracking, especially for industries like cold storage or hazardous materials is essential for efficient recall management and billing accuracy.
- Seamless integration: 3PLs should easily integrate with other enterprise software solutions, like CRMs, ERPs, and automation systems.
- Customer access: Providing clients with a web-based portal to access inventory and orders, along with intuitive user interfaces that simplify navigation, boost operational efficiency, and the quality of customer service.
Ultimately, the best 3PL WMS will depend on your business requirements, IT infrastructure, budget, and growth plans. For example, Made4net’s 3PLExpert includes these essential features and more. For 3PLs aiming to balance cost-efficiency and scalability, choosing between SaaS (Software-as-a-Service) and Perpetual licensing models is also an additional consideration.
SaaS vs. Perpetual: What’s the Best 3PL Software Pricing Option for You?
SaaS and Perpetual licensing models differ fundamentally in how software is purchased, accessed, and maintained.
A quick comparison is as follows:
Aspect | SaaS | Perpetual |
Cost | Subscription (lower upfront) | One-time (high upfront) |
Maintenance | Vendor-managed | User-managed |
Access | Internet-based | Local installation |
Scalability | Flexible | Limited without new purchases |
Updates | Automatic | Requires additional purchase |
Long-tern Cost | Higher over time | Lower if used long-term |
Choosing between SaaS and perpetual depends on factors like budget, scalability needs, IT infrastructure, and the organization’s preference for ownership versus flexibility.
Next Steps: 3PL Software Pricing
With the right WMS, 3PLs can achieve seamless operations and enhance customer satisfaction. By considering all aspects of WMS pricing—including solution tiers, key features, integration requirements, implementation costs, hidden fees, and more—3PLs can ensure a good fit and a strong return on investment (ROI). If you need help finding the best WMS for your 3PL needs, reach out to one of our experts.
And, to learn how to effectively cover your operational costs and achieve profitability, check out our 3PL pricing strategies blog post.